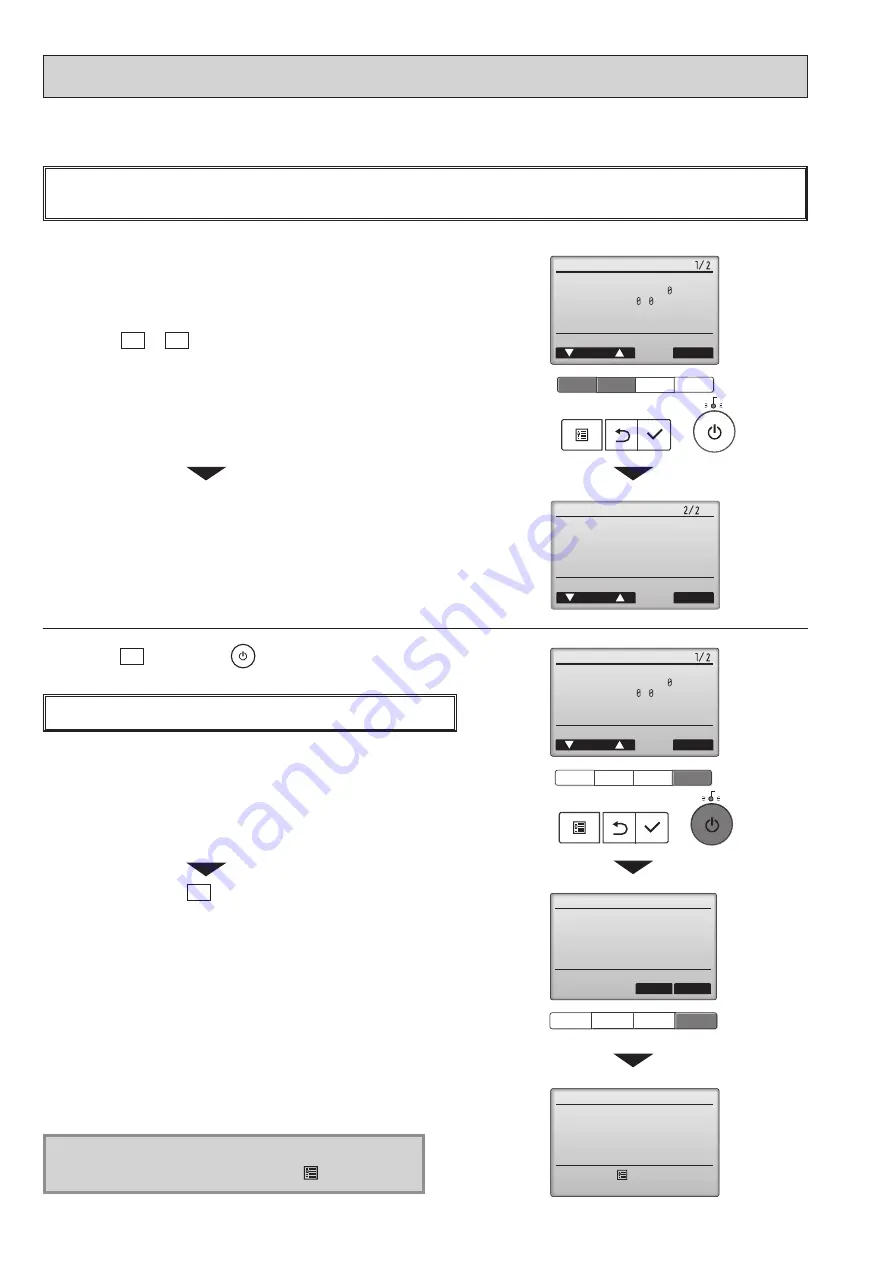
44
OCH758
Error information
Error code A3
Error unit IU
Time Occurred
Model name
Serial No.
Reset
Page
2/ 1
Unit#1
4:48
Reset error: Reset button
Error information
Error code A3
Error unit IU
Time Occurred
Model name
Serial No.
Reset
Page
2/ 1
Unit#1
4:48
Reset error: Reset button
Error information
Contact information
Dealer
Tel
Reset
Page
Reset error: Reset button
Error reset
Error reset
Main menu:
Error reset
Reset current error?
OK
Cancel
F1
F2
F3
F4
1. Check code, error unit, refrigerant address, date and time of occur-
rence, model name, and serial number will appear.
The model name and serial number will appear only if the informa-
tion have been registered.
Press the F1 or F2 button to go to the next page.
When an error occurs, the following screen will appear.
Check the error status, stop the operation, and consult your dealer.
Contact information (dealer's phone number) will appear if
the information has been registered.
2. Press the F4 button or the
button to reset the error
that is occurring.
Errors cannot be reset while the ON/OFF operation is prohibited.
Select ˝OK˝ with the
F4 button.
Navigating through the screens
• To go back to the Service menu .......... [
]
button
13-2. ERROR INFORMATION
blinks
F1
F2
F3
F4
blinks
F1
F2
F3
F4