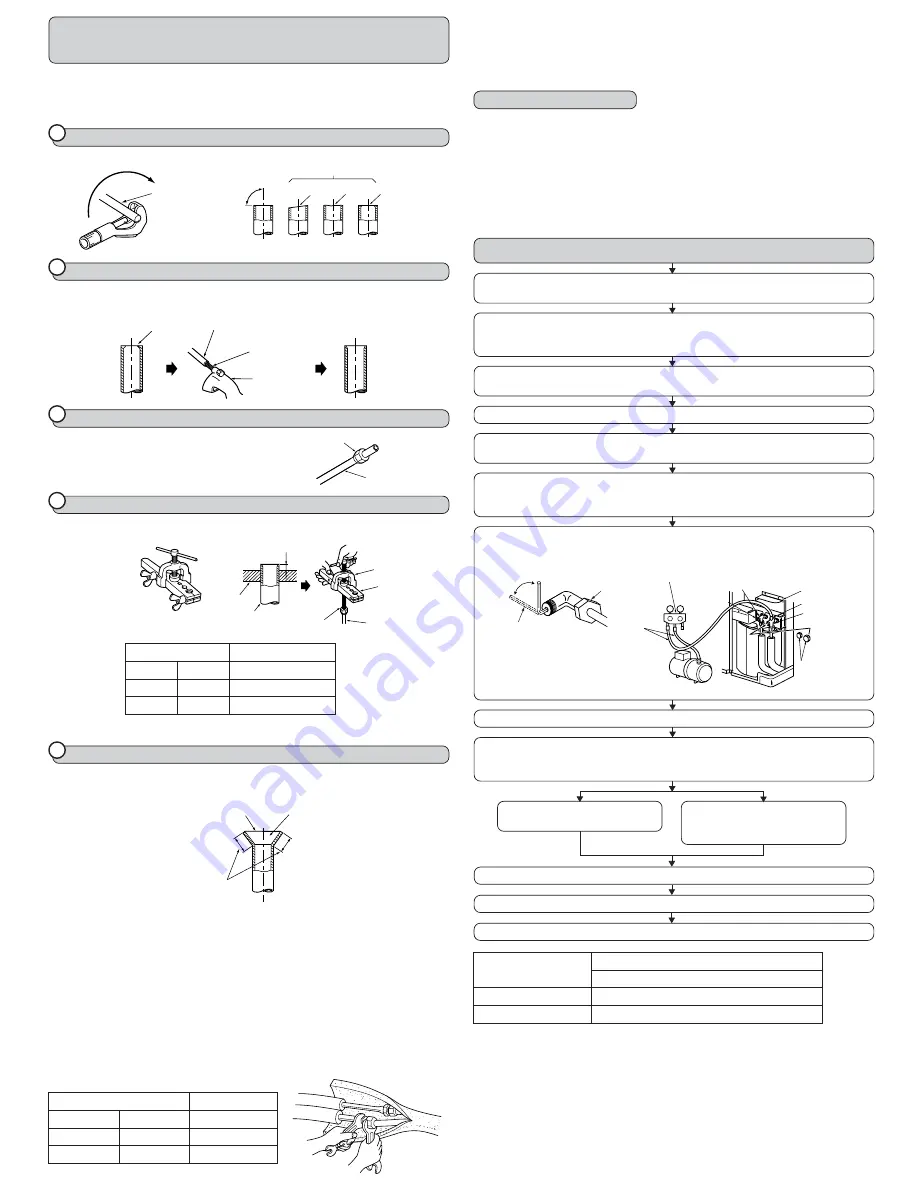
Copper pipe
Good
No good
Tilted
Uneven Burred
90
°
A
Tightening torque
ft. · Ibs
Cap for service port
10 to 13
Cap for stop valve
15 to 22
6-2 PIPE CONNECTION
Note:
When bending the pipe, a specified tool should be used.
1
Indoor unit connection
Connect both liquid pipe and gas pipe to indoor unit.
•
Apply a thin coat of refrigeration oil
J
on the seat surface of pipe.
•
For connection, align the center of both pipe and union, then tighten the first 3 to 4
turns in flare nut by hand.
•
For tightening the union part of the indoor unit side, use the table below as a standard
and tighten the flare nut using two wrenches. Excessive tightening damages the flare
section.
Pipe diameter
Tightening torque
mm
inch
ft. · Ibs
9.52
3/8
25 to 30
15.88
5/8
54 to 58
Burr
Copper pipe
Spare
reamer
Pipe
cutter
Flare nut
Copper pipe
Flaring tool
Die
Copper pipe
Flare nut
Die
Copper pipe
York
Smooth all around
Even length
all around
Inside is shining without any scratches.
Close
Open
Hexagonal wrench
Stop valve
PURGING PROCEDURES
Connect the refrigerant pipes (both liquid pipe and gas pipe) between the indoor
and the outdoor unit.
Remove the service port cap of the stop valve on the gas pipe side of the outdoor
unit. (The stop valve will not work in it initial state fresh out of the factory (totally
closed with cap on).)
Connect the gauge manifold valve and the vacuum pump to the service port of the
stop valve on the gas pipe side of the outdoor unit.
Run the vacuum pump. (Vacuumize for more than 15 minutes.)
Check the vacuum with the gauge manifold valve, then close the gauge manifold
valve and stop the vacuum pump.
Leave as it is for one or two minutes. Make sure the pointer gauge manifold valve
remains in the same position. Confirm that the pressure gauge shows -0.101 Mpa
[Gauge] (-30 in. Hg).
Pipe length up to 25 ft.
No gas charge is needed.
Pipe length exceeding 25 ft.
Charge the prescribed amount
of gas. (refer to 3)
Remove the gauge manifold valve quickly from the service port of the stop valve.
After refrigerant pipes are connected and evacuated, fully open all stop valves on
both sides of gas pipe and liquid pipe.
Operating without fully opening lowers the performance and this causes trouble.
Tighten the cap to the service port to obtain the initial status.
Retighten the cap.
Leak test
2
Outdoor unit connection
Connect pipes to the pipe joint part of the stop valve in the same method as the indoor
unit.
•
For tightening, use the same tightening torque applied for indoor unit and tighten the
flare nut with torque wrench or spanner.
INSULATION AND TAPING
1
Cover piping joints with pipe cover.
2
For outdoor unit side, surely insulate every piping including valves.
3
Using piping tape
G
, apply taping starting from the entry of outdoor unit.
•
Fix the end of piping tape
G
with adhesive tape.
•
When piping has to be arranged through above ceiling, closet or area where the
temperature and humidity are high, wind additional commercially sold insulation for
prevention of condensation.
6-3 PURGING PROCEDURES·LEAK TEST
6. INDOOR/OUTDOOR UNIT CONNECTION
FINISHING AND TEST RUN
6-1 FLARING WORK
•
Main cause of gas leakage is defect in flaring work.
Perform flaring work correctly in the following procedure.
1 Pipe cutting
•
Cut the copper pipe correctly with pipe cutter.
2 Burrs removal
•
Completely remove all burrs from the cut cross section of the pipe.
•
Put the end of the copper pipe downward to prevent burrs from dropping in the pipe.
3 Putting nut on
•
Remove flare nuts attached to indoor and outdoor
units, then put them on pipe having completed
burr removal.
(not possible to put them on after flaring work)
4 Flaring work
•
Perform flaring work using flaring tool as shown below.
Outside diameter
A
mm
inch
inch
9.52
3/8
1/8
15.88
5/8
5/32
•
Firmly hold copper pipe in a die in the dimension shown in the table above.
5 Check
•
Compare the flared work with figure below.
•
If flare is noted to be defective, cut off the flared section and perform flaring work
again.
Gauge manifold valve
Stop valve
(Liquid)
Hexagonal
wrench
Caps
Stop valve (Gas)
Vacuum pump
Charge
hose
* Remove the GUARD before air purge,
and reinstall the GUARD after servicing.
GUARD
Service port