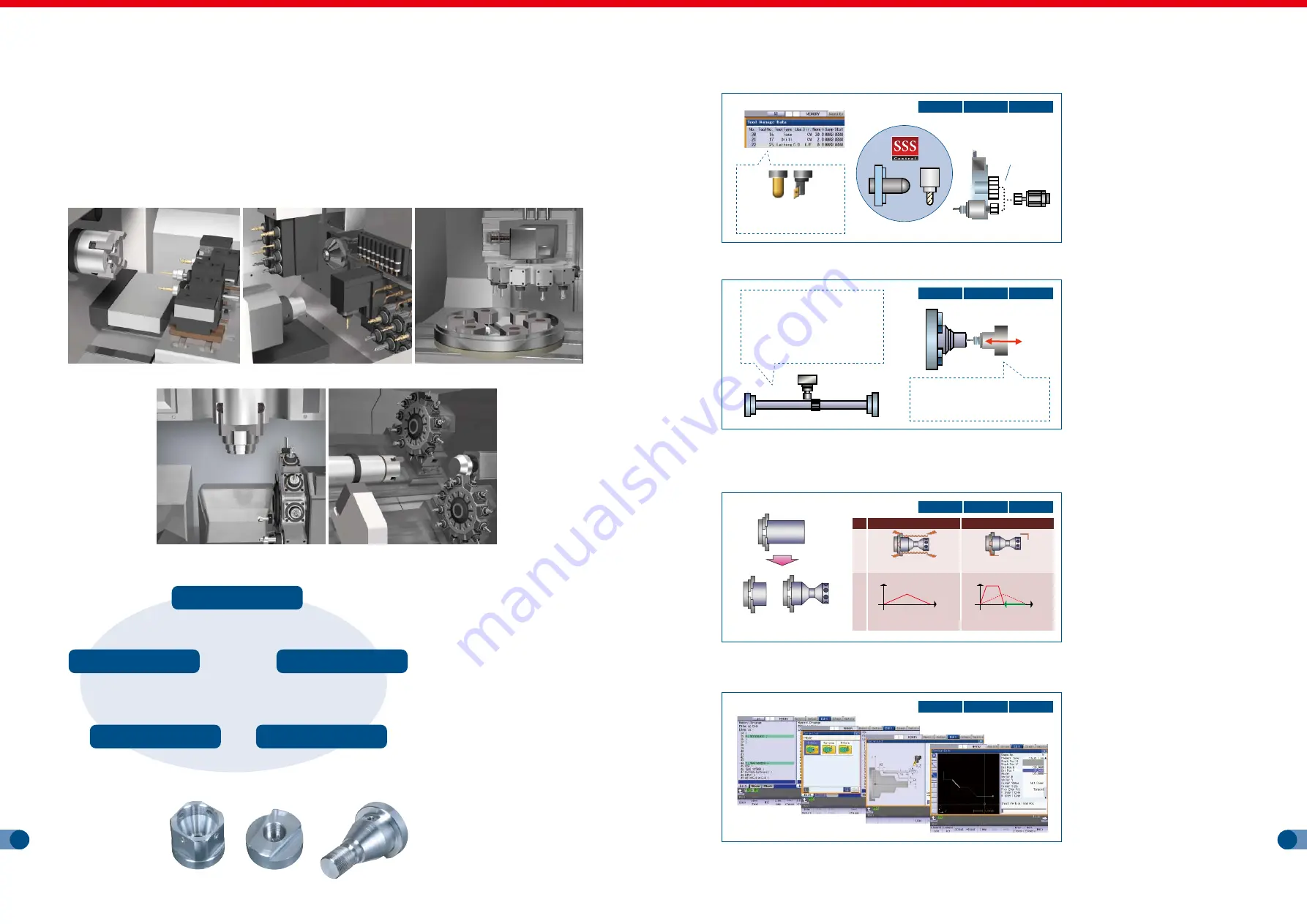
Lathe
Automatic lathe
Vertical lathe
Inverted lathe
Multi-tasking lathe
11
12
ENHANCED LATHE SYSTEM
ENHANCED LATHE SYSTEM
High-speed high-accuracy control
features accumulated originally for
machining centers are now available in
lathe system. Fine milling can be
implemented at high speeds on a
lathe.
This CNC enables a servo motor,
instead of a spindle, to act as a tool
spindle. Any of the servo control axes
driven by multi-hybrid drive can be
used as a tool spindle. This contributes
to the downsizing of machine tools.
Improved milling features
using a tool spindle
M800/M80 Series provides "Spindle
superimposition control, "a feature
that enables simultaneous execution
o f t u r n i n g a n d c e n t e r t a p p i n g ,
although they needed to be executed
individually.
These features are effective in
eliminating idle time, resulting in a
significant reduction in tact time.
This CNC also offers features that
maintain synchronization between
part systems, which is required for
automatic lathes, in particular. These
enable operators to implement ever
more complex machining safely and
securely.
Multi-axis multi-part system
control features help to
reduce cycle time and
maintain synchronization
between part systems
Programming has been made much
easier: program edit screen shows the
synchronization points between part
systems in an easy-to-understand
d i s p l a y, a n d c o n v e r s a t i o n a l
programming allows insertion of
canned cycles. After programming,
operators can check the programs
through 3D work simulation before
actual cutting.
Significantly easier
programming
High-speed high-accuracy control and SSS control are available for milling using lathe system.
A servo motor driven by a servo drive unit can be controlled as a tool spindle.
Conversational programming, tool measurement, work coordinate system shift and
other features have been improved, making the lathe system significantly easier to use.
Milling features have been improved
through high-speed high-accuracy
control and SSS control. Multi-axis,
multi-part system control features have
also been upgraded. A wide array of
these features help ensure high
productivity.
Significant progress has also been
made in frequently used operation as
well as programming, such as tool
offset and workpiece coordinate
system shift, which allows operators to
easily implement ever more complex
machining.
Implement ever more
complex machining in an
easy and efficient manner
ENHANCED LATHE SYSTEM
Milling features and multi-axis, multi-part system control features have been significantly improved.
Progress has been made in operability, enabling operators to implement ever more complex machining
in an easy and efficient manner.
M800W
M800S
M80
M800W
M800S
M80
High-speed high-accuracy control
Super Smooth Surface (SSS) control
Spindle-mode servo motor control
Milling features
Supports up to 8 part systems, 32 axes and 8 spindles
Loader control via sub-part system control
Spindle superimposition control
Multiple spindle synchronization set control
Multi-axis, multi-part system
control features
Re-thread cutting
Thread cutting override
Real-time tuning
Large-sized display
Features for
large-sized lathes
Workpiece coordinate system shift
Easy setup of barrier check parameters
Simple monitor screen showing
narrowed-down information
User operability
Program edit with timing synchronization
between part systems
Interactive cycle insertion
3D program check
Conversational
programming
Milling and turning tools can
be registered in tool
management screen
Gear
change
mechanism
Turret
Tool spindle
Servo motors
M800 Series controls up to 8 part systems, 32 axes and 8 spindles.
This CNC provides the advanced multi-axis, multi-part system control features
including loader control using sub-part system, spindle superimposition
and synchronization of multiple spindle sets.
M800W
M800S
M80
Multiple spindle synchronization set
control
Tool spindle can be synchronized with
the long workpiece held by the front
and back spindles. The spindles can
implement C axis indexing while
holding the workpiece.
Spindle superimposition
(differential speed tap)
Lathe turning and center tapping can
be implemented simultaneously.
Real-time tuning helps maintain the stability of large lathes.
This function detects vibration caused by significant fluctuation of work inertia
and automatically adjusts the control gain.
M800W
M800S
M80
Heavy workpiece
Another
workpiece
Inertia fluctuates widely
After
cutting
Real-time tuning OFF
Tends to vibrate
(control gain is fixed)
Vibration is suppressed
(control gain is automatically adjusted)
Acceleration remains
unchanged whether the
workpiece is heavy or light
Acceleration is suited to the
inertia Acceleration time is
shorter for a lighter workpiece
Real-time tuning ON
Speed
Time
Speed
Time
Stability
Acceleration