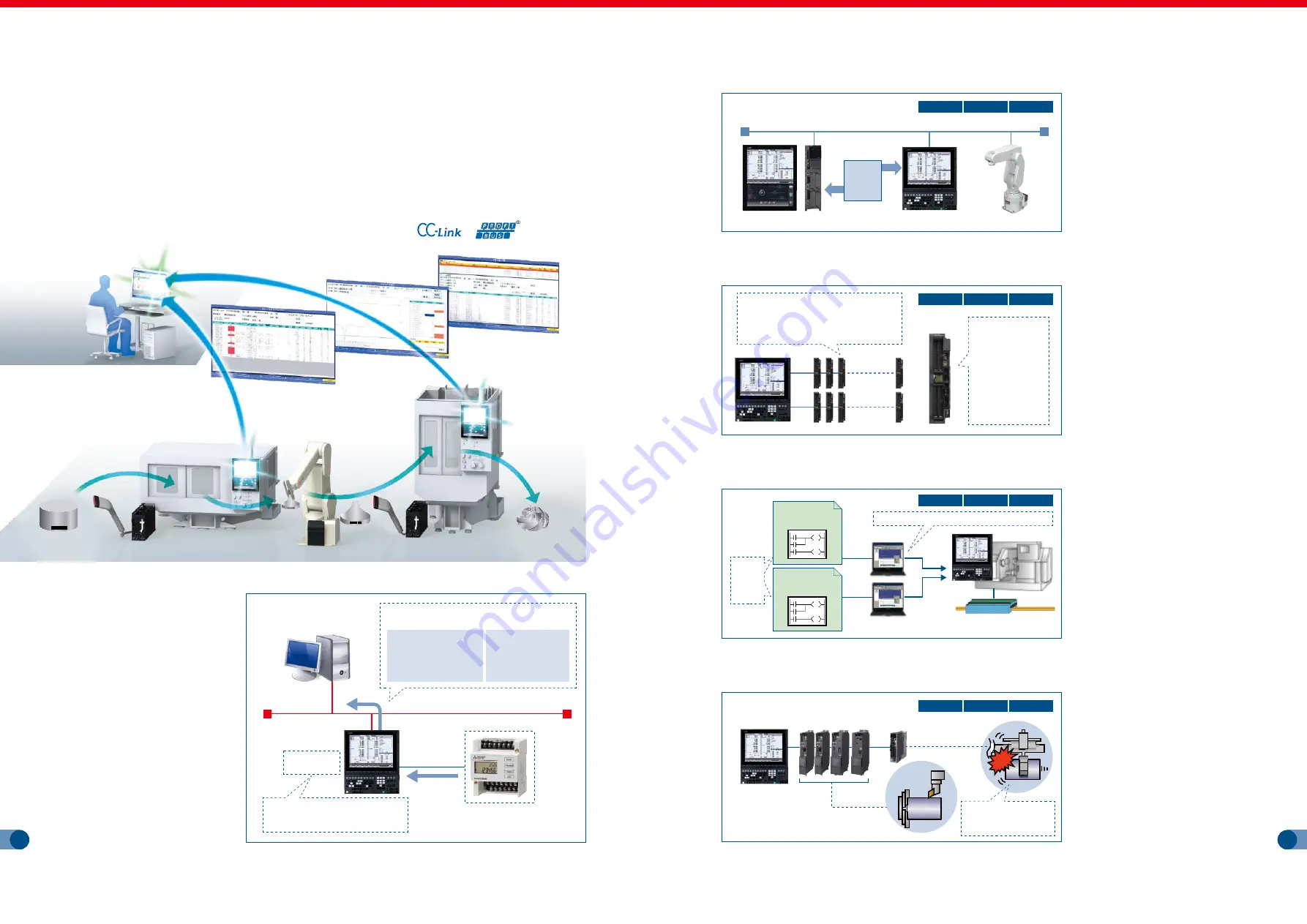
17
18
SUPPORT FOR AUTOMATION
SUPPORT FOR AUTOMATION
SUPPORT FOR AUTOMATION
ENHANCED TRACEABILITY
M800/M80 Series CNCs are equipped with
the MES interface function, through which
the CNC automatically sends SQL
statements to the production control system
database upon completion of cutting or
occurrence of an alarm. This can significantly
increase traceability throughout the factory.
This transparency helps optimize production
planning and management.
Quality control can also be easier through
visualization of alarm history and the
production results based on the basic unit
specific to each workpiece.
In addition, when control is combined with
the EcoMonitorLight power consumption
monitor, operators can monitor not only
CNC status, but also the energy consumed
by the machines.
Improved traceability
helps to visualize
factory-wide operation
With the aim of configuring factory
automation systems, compatibility with
a range of field networks has been
implemented, enabling connection to
peripheral equipment and devices.
Insert the option card into the standard
expansion slot of the M800W Series
CNC or on the back side of the display
for the M800S/M80 Series.
Compatible with a range
of field networks that
facilitate connection to
peripheral equipment
I/O units have been redesigned. The
renewed I/O communication method
makes it possible to significantly
increase the maximum number of
contact points per channel, enabling a
number of peripheral equipment and
devices to be controlled by CNC alone.
In addition, built-in PLC functionality for
I/O control has been improved. This
CNC supports Multi-project PLC, a
feature that enables ladder logics for
peripheral equipment to be managed
separately from those for machine
tools. This creates a more efficient
environment for operators working
together in developing and managing
ladder logics.
Renewed I/O units and
built-in PLC functionality
make it easier to control
and manage peripheral
equipment
M800/M80 Series has a feature called
Machine Group-based Alarm Stop,
which stops operation of individual
machine groups if an alarm occurs
when control is combined with the
MDS-E/EM/EJ Series.
This feature allows continuation of
machining even when an alarm occurs
on a loader, magazine or other peripheral
equipment.
New feature capable of
stopping peripheral
equipment incorporated
Needs for automation are increasing, which can be realized more easily with lower cost.
Compatible with CC-Link (master/slave), PROFIBUS-DP (master) .
Possible to connect to peripheral equipment and devices conforming to a range
of field networks.
During an alarm, operation of individual machine groups can be stopped.
Machining is not interrupted when an alarm occurs on peripheral equipment (e.g., loader).
Needs for automation are increasing, which can be realized more easily
and with lower cost.
Supports automation needs
Connectable to a range of field networks
Traceability
Automation of small-scale line easily realized
Trend graph
Alarm list
Workpiece
M800W
M800S
M80
M800W
M800S
M80
CC-Link
Mount in
expansion slot
Mount on
control unit
CC-Link
card
Renewed I/O communication method allows for the control of up to 64 stations
and 2,048 points per channel.
Various peripheral equipment can be controlled by the CNC alone.
M800W
M800S
M80
Each channel accommodates up to 32
units (64 stations, 2048 points)
Devices can be allocated to each
station using the parameters
The I/O unit makes
it more efficient to
design and build
machine tools
All wiring is on
the front
Possible to be
mounted on DIN
rail
If an alarm occurs on the
loader axis, only the
loader is stopped.
Group 1
Group 2
Loader
LAN
Production control system
Possible to monitor production results based on the basic
unit specific to each workpiece, as well as the alarm history
Upon completion of cutting or occurrence
of alarm, CNC sends the data collected to
the database.
When cutting is complete
Work ID, Cutting start/end
time, Maximum spindle load,
Power consumption, Tool
number, Tool offset, etc.
During alarm
Work ID, Time of alarm
occurrence, Details of
alarm, Tool number,
Tool offset, etc.
MES interface
function
Machining information
EcoMonitorLight
Power
consumption
ModbusRTU
Multi-project PLC enables control of ladder logic for peripheral equipment separately
from that for machine tools. This leads to efficient development and management of
ladder logics for peripheral equipment.
M800W
M800S
M80
M
device
can be
shared
Machine tool
Project 1
Project 2
Conveyor
Ladder logic
for machine tool
Ladder logic for
peripheral equipment
Individual ladder development and management