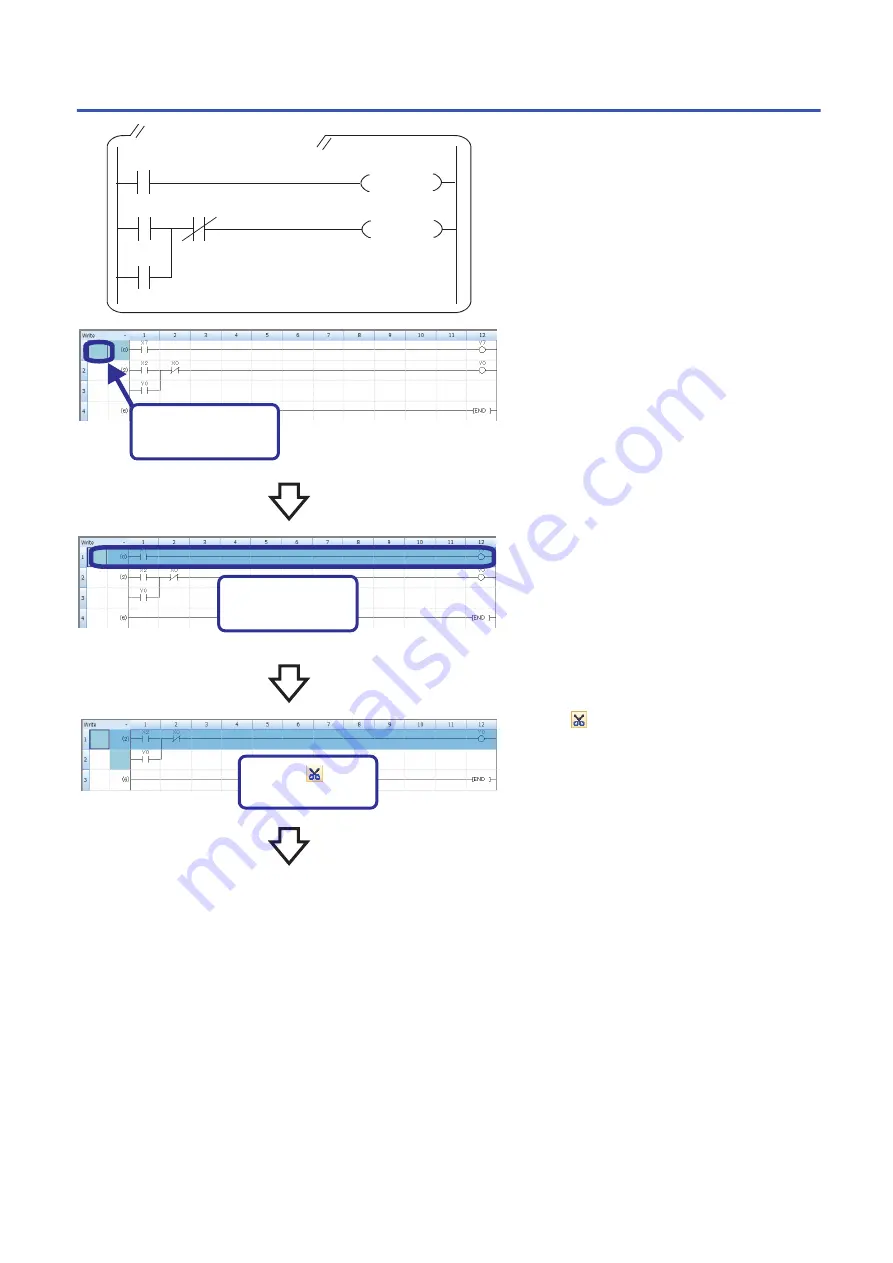
Cutting or copying a ladder
This section describes how to cut or copy a part of
the ladder program shown on the left and paste the
cut part or the copy of the part to any desired
location in the ladder.
1.
Click and move the cursor to the position
where a part of the ladder program is to be cut.
2.
Drag the mouse to specify the cutting range.
The color of the specified range is highlighted.
To easily specify the range in units of ladder blocks,
click the position where a step number is displayed
and drag the mouse vertically.
3.
Click on the toolbar, or select [Edit] → [Cut]
(
+
) to cut the ladder in the specified
range.
(To the next page)
X2
X100
Y0
Y0
A ladder program to be modified
Y7
1.
Click and move
the cursor!
2.
Drag to specify
the range!
3.
Click to cut
the range!
X7
41
Summary of Contents for FX5U Series
Page 1: ...FX5U Training Manual ...