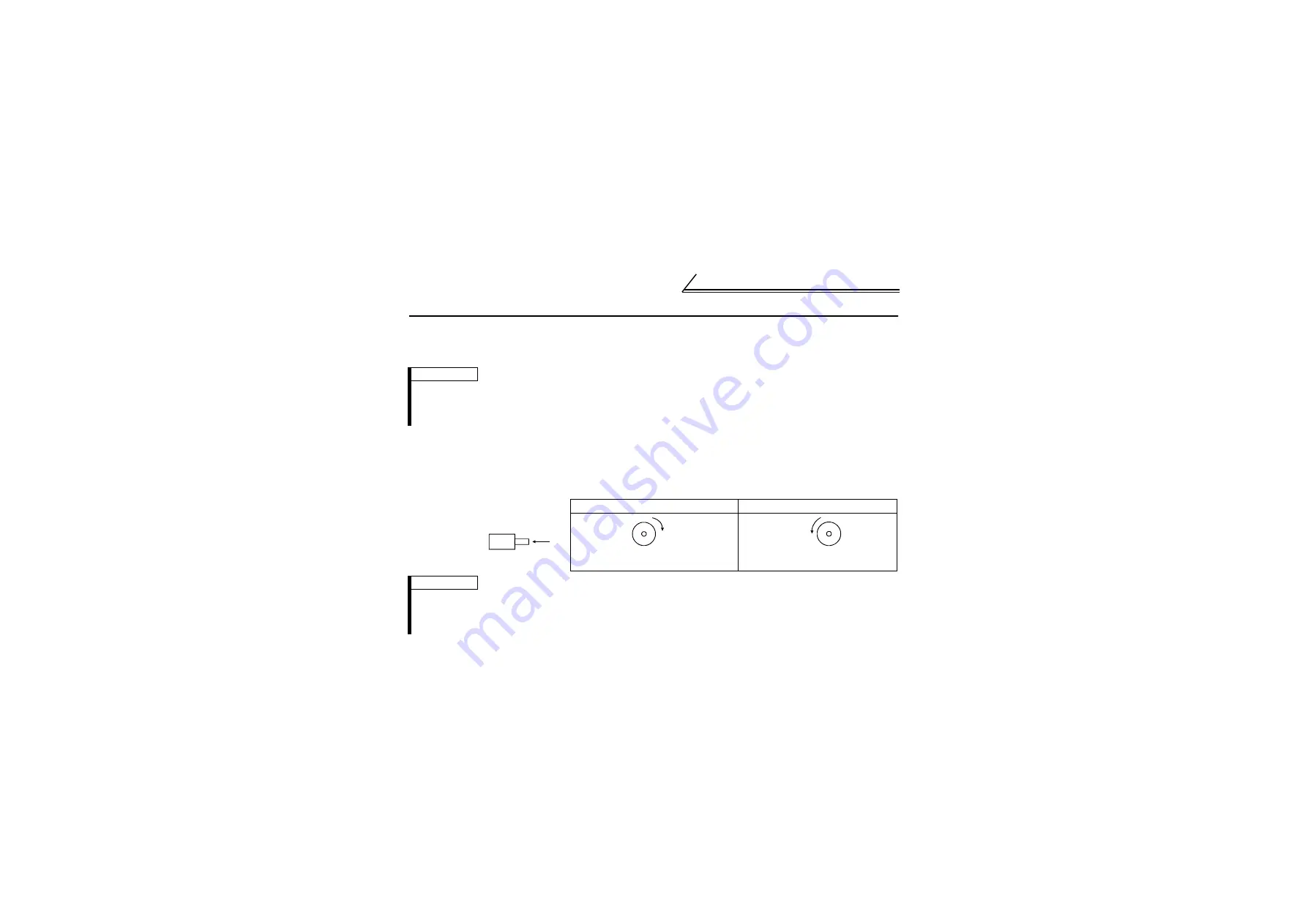
39
ENCODER FEEDBACK CONTROL—A500(L)
4.5 Pre-Operation Settings
(1) Pr. 144 "number of motor poles (encoder)". (factory setting: 4)
The either of the following motors may be used. Set the number of motor poles according to the motor used:
•
Standard motor (with encoder)
: SF-JR 0.2kW to 55kW
•
Constant-torque motor (with encoder)
: SF-JRCA 0.4kW to 55kW
(2) Pr. 369 "number of encoder pulses". (factory setting: 1024)
Set the number of encoder pulses.
Set the number of pulses before it is multiplied by 4.
Example: Set "1024" for 1024 pulses per revolution (ppr).
(3) Pr. 359 "encoder rotation direction". (factory setting: 1)
(4) Indicates the direction in which the encoder rotates.
REMARKS
1.
For vector control, this parameter value is made invalid and the setting of Pr. 81 "number of motor poles" is made
valid.
2.
If you set this parameter value to "0, 10 or 110" and operate the inverter, any of E.OP1 to E.OP3 occurs.
3.
If you set "102, 104, 106 or 108", that value minus 100 is set as the number of poles.
Pr. 359=0
Pr. 359=1 (factory setting)
Forward rotation is clockwise rotation
when viewed from A.
Forward rotation is counterclockwise
rotation when viewed from A.
REMARKS
When the FR-A5AP is fitted and encoder feedback control or vector control is selected, the PU (FR-DU04/FR-PU04)
shows the rotation direction of the encoder.
Make the setting so that FWD is displayed when the STF signal switches on or REV displayed when the STR signal
switches on.
A
encoder
CW
CCW