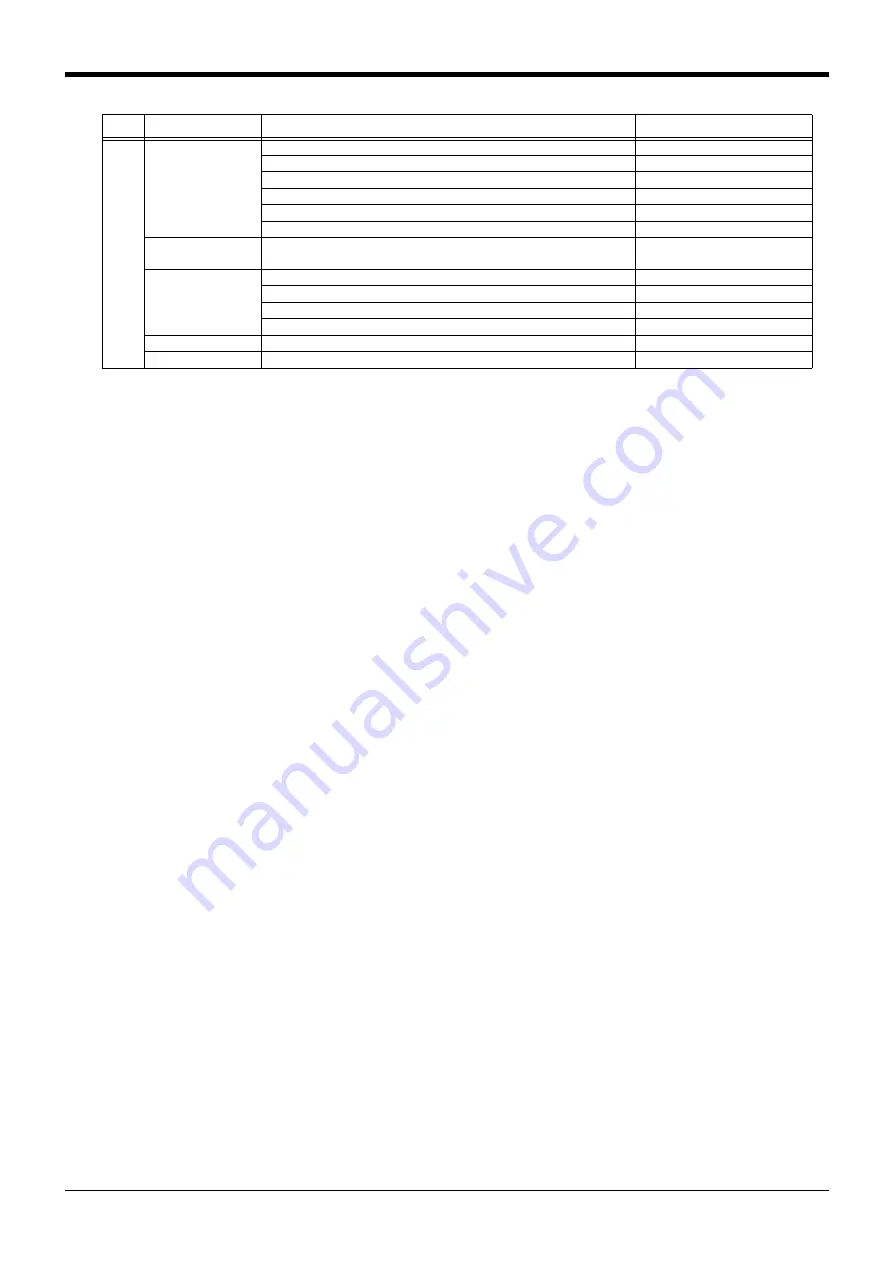
4Software
List of commands 4-92
Others
Definition
Defines the integer type or real number type variable.
Def Inte KAISUU
Defines the character string variable.
Def Char MESSAGE
efines the layout variable. (Up to 3-dimensional possible)
Dim PDATA(2,3)
Defines the joint variable.
Def Jnt TAIHI
Defines the position variable.
Def Pos TORU
Defines the function.
Def FN TASU(A,B)=A+B
Clear
Clears the general-purpose output signal, variables in program, variables
between programs, etc.
Clr 1
File
Opens a file.
Open "COM1:" AS #1
Closes a file.
Close #1
Inputs data from a file.
Input# 1,M1
Outputs data to a file.
Print# 1,M1
Comment
Describes a comment.
Rem "ABC"
Label
Indicates the branching destination.
*SUB1
Type
Class
Function
Input format (example)
Summary of Contents for CR1DA-7A1-S15
Page 2: ......
Page 118: ......
Page 119: ......
Page 120: ......
Page 121: ......
Page 122: ......
Page 123: ......
Page 124: ......
Page 125: ......
Page 126: ......
Page 127: ......
Page 128: ......
Page 129: ......
Page 130: ......
Page 131: ......
Page 132: ......
Page 133: ......
Page 134: ......
Page 135: ......
Page 136: ......
Page 137: ......
Page 138: ......
Page 139: ......
Page 140: ......
Page 141: ......
Page 142: ......
Page 143: ......