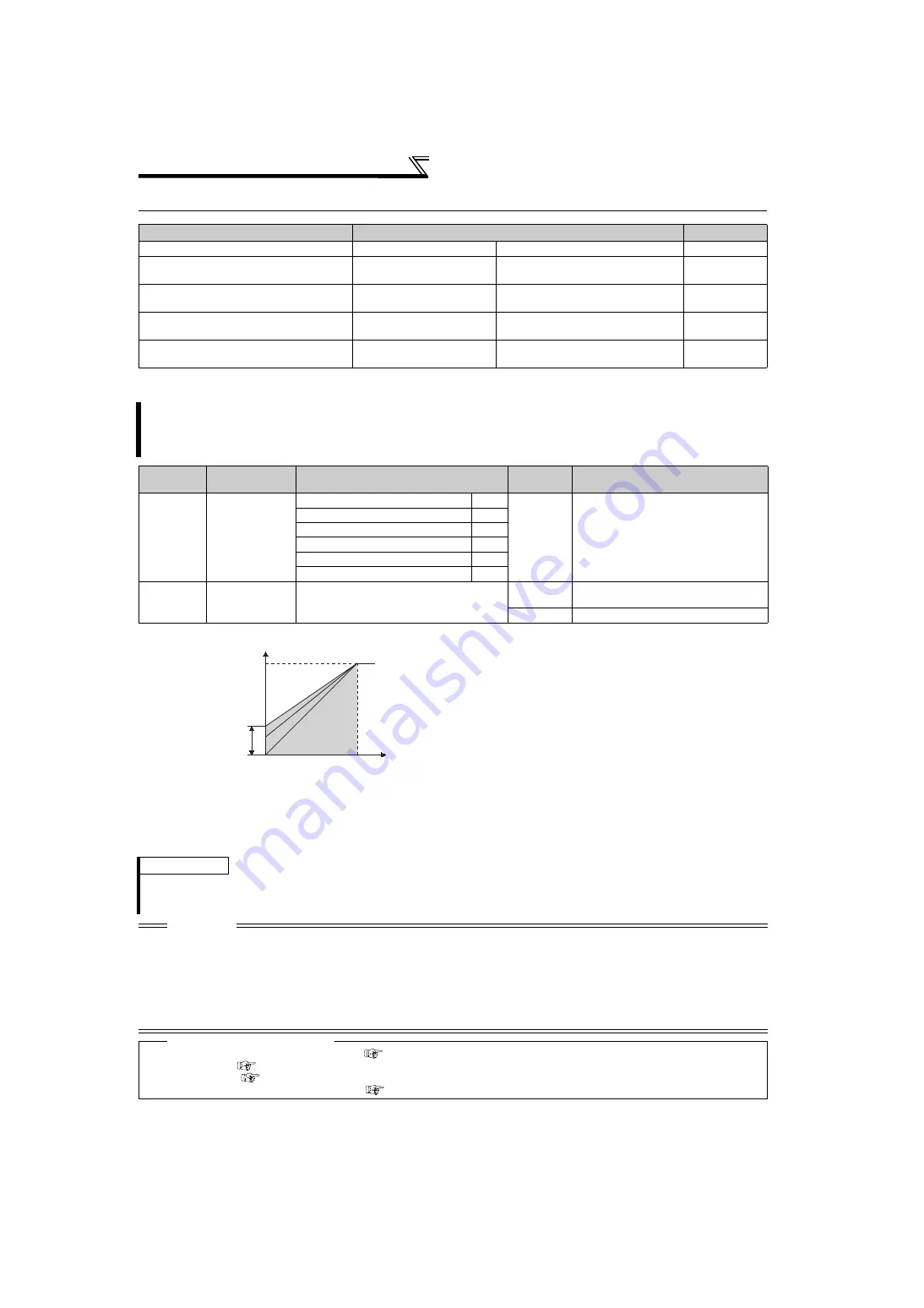
78
Adjustment of the output torque (current) of the motor
4.3 Adjustment of the output torque (current) of the motor
4.3.1
Manual torque boost (Pr. 0, Pr. 46)
(2) Set multiple torque boost (RT signal,
Pr. 46
)
⋅
Use the second torque boost when changing the torque boost according to application or when using multiple
motors by switching between them by one inverter.
⋅
Pr. 46 Second torque boost
is valid when the RT signal turns ON.
Purpose
Parameter that must be Set
Refer to Page
Set starting torque manually
Manual torque boost
Pr. 0, Pr. 46
Automatically control output current
according to load
Simple magnetic flux
vector control
Pr. 71, Pr. 80, Pr. 90
Compensate for motor slip to secure
low-speed torque
Slip compensation
Pr. 245 to Pr. 247
Limit output current to prevent inverter
trip
Stall prevention operation
Pr. 22, Pr. 23, Pr. 66,
Pr. 154, Pr. 156, Pr. 157
Change the overload current rating
specifications
Multiple rating setting
Pr. 570
You can compensate for a voltage drop in the low-frequency range to improve motor torque reduction in the low-
speed range.
Motor torque in the low-frequency range can be adjusted to the load to increase the starting motor torque.
The starting torque boost can be changed by switching terminals.
Parameter
Number
Name
Initial Value
200V class (400V class)
Setting
Range
Description
0
Torque boost
00046 (00023)
6%
0 to 30%
Set the output voltage at 0Hz as %.
00077 to 00167 (00038 to 00083)
4%
00250, 00340 (00126, 00170)
3%
00490 to 01540 (00250 to 00770)
2%
01870,02330 (00930, 01160)
1.5%
03160 (01800) or more
1%
46
*1
Second torque
boost
9999
0 to 30%
Set the torque boost value when the
RT signal is ON.
9999
Without second torque boost
*1
They can be set when
Pr. 160 User group read selection
= "0".
(Refer to page 190.)
(1) Starting torque adjustment
⋅
On the assumption that
Pr. 19 Base frequency voltage
is
100%, set the output voltage at 0Hz in % in
Pr. 0
(
Pr. 46
).
⋅
Adjust the parameter little by little (about 0.5%), and check
the motor status each time. If the setting is too large, the
motor will overheat. The guideline is about 10% at the
greatest.
REMARKS
⋅
The RT signal acts as the second function selection signal and makes the other second functions valid.
(Refer to page 124)
⋅
The RT signal is assigned to the RT terminal in the default setting. By setting "3" to any of
Pr. 178 to Pr. 189 (Input terminal function
selection)
, you can assign the RT signal to the other terminal.
CAUTION
⋅
Increase the setting when the distance between the inverter and motor is long or when motor torque is insufficient in the low-
speed range. If the setting is too large, an overcurrent trip may occur.
⋅
The
Pr. 0
and
Pr. 46
settings are valid only when V/F control is selected.
⋅
When using the inverter dedicated motor (constant-torque motor) with the FR-F720-00250 or 00340 and FR-F740-00126 or
00170, set the torque boost value to 2%. If the initial set
Pr. 71
value is changed to the setting for use with a constant-torque
motor, the
Pr. 0
setting changes to the corresponding value in above.
⋅
Changing the terminal assignment using
Pr. 178 to Pr. 189 (input terminal function selection)
may affect the other functions. Please
set parameters after confirming the function of each terminal.
♦
Parameters referred to
♦
Pr. 3 Base frequency, Pr. 19 Base frequency voltage
Refer to page 89
Pr. 71 Applied motor
Refer to page 111
Pr. 80 Motor capacity
Refer to page 79
Pr. 178 to Pr. 189 (Input terminal function selection)
Refer to page 122
Output
voltage
Pr.0
Pr.46
Setting
range
Base
frequency
0
100%
Output
frequency
(Hz)
Summary of Contents for 700 Series
Page 11: ...MEMO ...
Page 23: ...12 MEMO ...
Page 341: ...330 MEMO ...
Page 365: ...354 MEMO ...
Page 379: ...368 MEMO ...
Page 397: ...386 MEMO ...
Page 414: ...403 MEMO ...