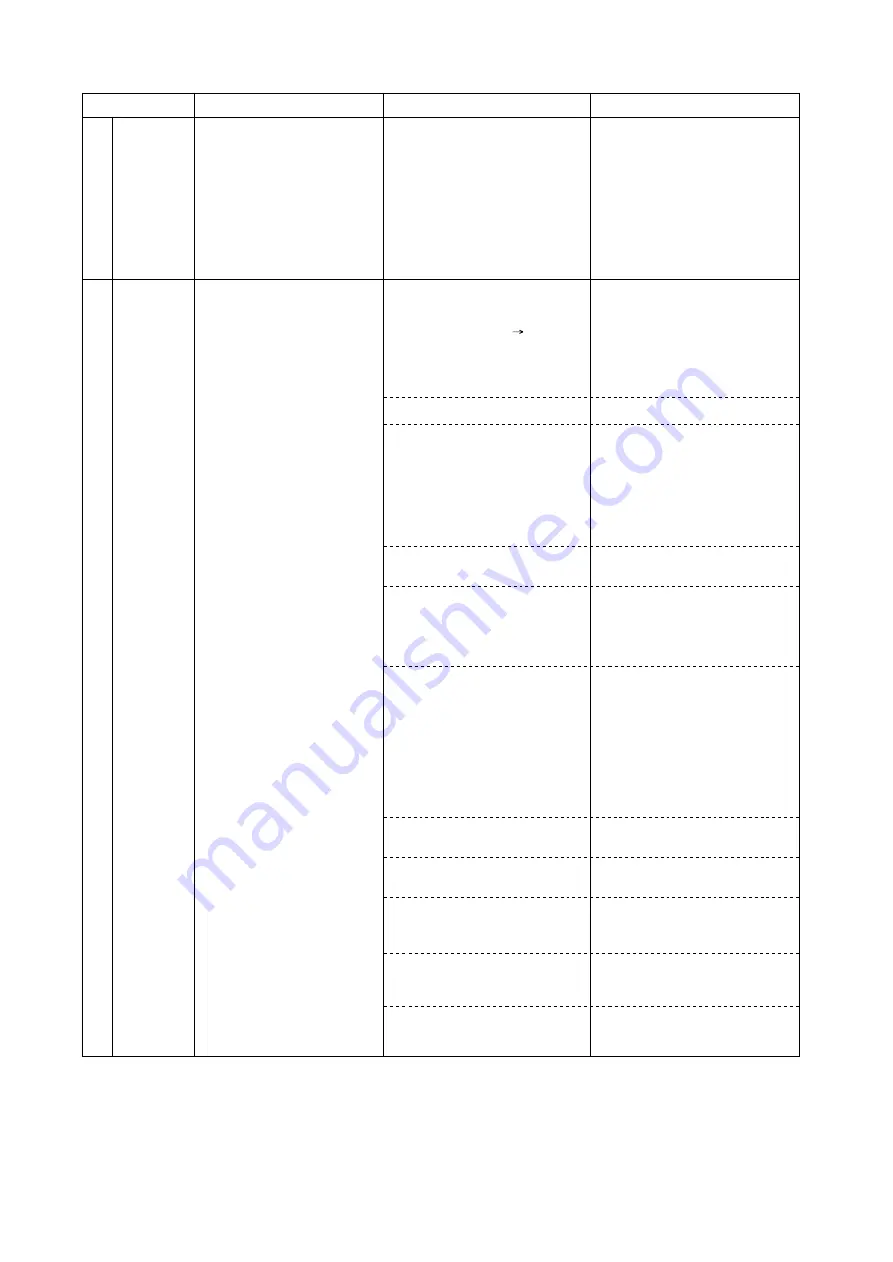
-154-
Checking code
Meaning, detecting method
Cause
Checking method & Countermeasure
1301
1302
Low pressure
abnoramlity
High pressure
abnoramlity 1
(Outdoor unit)
When starting from the stop mode
for the first time, (if at the start of bind
power transmission, the end of bind
power transmission, and in the mode
when the thermostat goes OFF im-
mediately after the remote control
goes ON, the following compressor
start time is included), if the low pres-
sure pressure sensor before start-
ing is at 0.098MPa,operation stops
immediately.
1. When press. sensor detects
2.47MPa or more
operations (the first time),
outdoor unit stops once,
mode is changed to restart
mode after 3 minutes, then the
outdoor unit restarts.
2. When 2.94MPa or more
pressure is detected again
(the second time) within
minutes after stop of outdoor
unit,error stop is observed with
code No. “1302” displayed.
3. When 2.47MPa or more
pressure is detected 30 or
more minutes after stop of
outdoor unit, the detection is re-
garded as the first time and the
process shown in 1 is observed.
4. 30 minutes after stop of outdoor
unit is intermittent fault check
period with LED displayed.
5. Error stop is observed immediately
when press. switch
(2.94
MPa) operates in addition to
pressure sensor.
1) Internal pressure is dropping due
to a gas leak.
2) The low pressure pressure sensor
is defective.
3) Insulation is torn.
4) A pin is missing in the connector,
or there is faulty contact.
5) A wire is disconnected.
6) The control board’s low pressure
pressure sensor input circuit is de-
fective.
Refer to the item on judging low pres-
sure pressure sensor failure.
+0
-1.5
Perform actual operation of cooling
and heating and check operating sta-
tus.
Cooling - SV5B, 21S4b
Heating - indoor unit LEV
Refer to Trouble check of LEV and
Solenoid valve.
Check if ball joint is fully open.
Check indoor unit and take measures
to trouble.
Inspect outdoor unit and repair nec-
essary areas.
Inspect outdoor fan.
Refer to Trouble check of outdoor
unit fan.
Refer to Trouble check of Solenoid
valve.
Check resistance of thermistor.
Refer to section on determining if pres-
sure sensor has failed.
Check whether or not sensor pick-up
heat and pressure using the LED
monitor.
Check whether or not sensor pick-up
heat and pressure using the LED
monitor.
Check whether or not sensor pick-up
heat and pressure using the LED
monitor.
1) Defective operation of indoor unit
LEV.
2) Defective operation of solenoid
valve 21S4b, SV5B
Cooliing.
3) Defective ball joint operation.
4) Short cycle of indoor unit.
5) Plugged filter of indoor unit.
6) Reduced fan flow due to dirty fan.
7) Dirty indoor heat exchanger.
8)
Defective indoor fan block, motor,
Note: For 4) to 8) there is a drop in
condensor performance due to a rise
in high pressure during heating.
9) Short cycle of outdoor unit.
10)Dirty outdoor unit heat exchanger.
11)Defective outdoor fan block, motor,
defective fan microcomputer opera-
tion, defective Note: 9) to 11) is drop
in condensor performance during
cooling due to rise in high pressure.
12)Defective operation of solenoid valve
SV22/32.
(Full load operation during unload.
500 YBM only.)
13)Defective operation of solenoid valve
contactor52C2 (No. 2 compressor op-
erating when it should be stopped).
14)Defective operation of solenoid valve
SV1, 4. (Cannot control high pres-
sure rise with bypass valve (SV1,4).)
15)Defective thermistor. (TH2, TH5,
TH6)
16)Defective pressure sensor.
17)Defective input circuit for thermistor
and pressure sensor on main circuit
board.
18)Defective mounting of thermistor.
(TH2, TH5, TH6)
19)Missing or disconnected pressure
switch connector (63H).
during
30