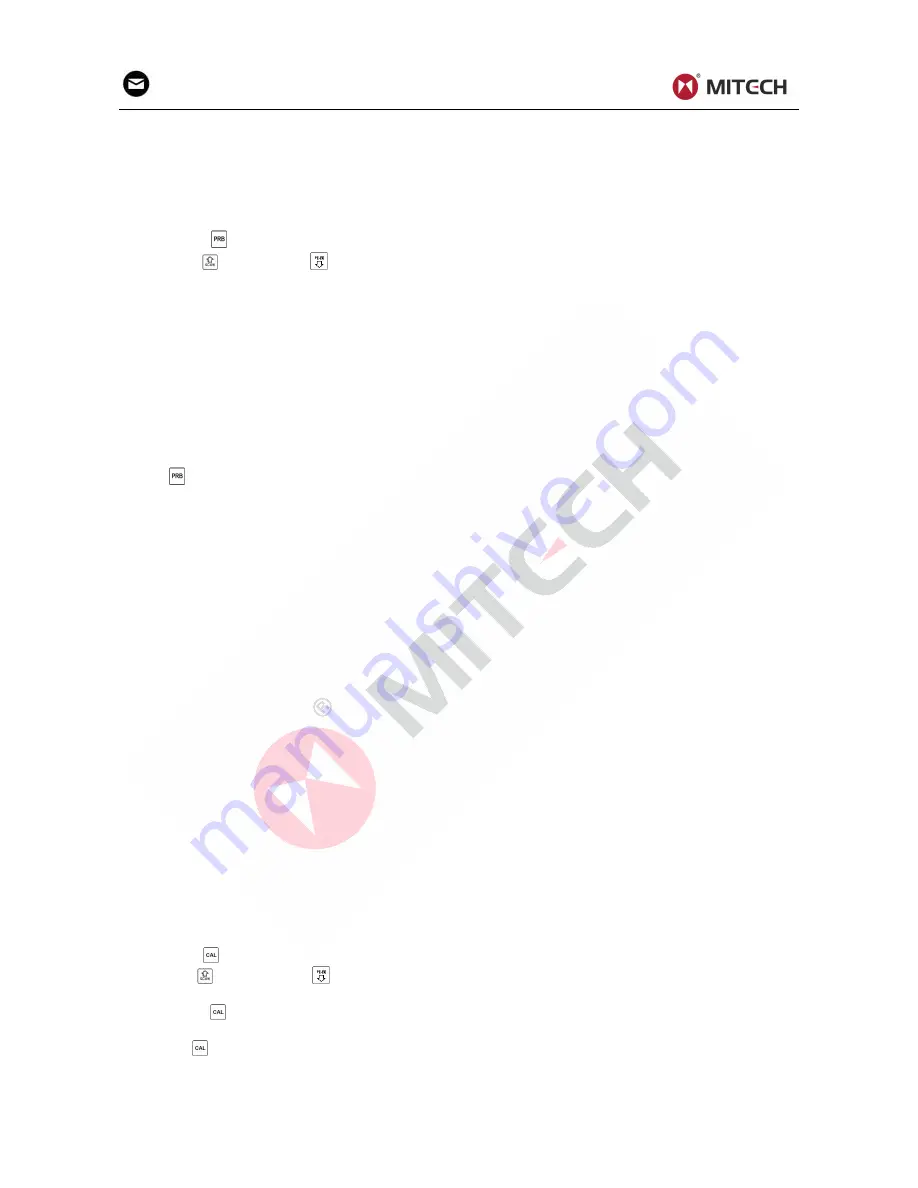
7
zeroed. If the gauge is not zeroed correctly, all the measurements that the gauge makes may be in error
by some fixed value. When the instrument is “zeroed”, this fixed error value is measured and
automatically corrected for all subsequent measurements. The instrument may be “zeroed ” by
performing the following procedure.:
①
Plug the transducer into the instrument. Make sure that the connectors are fully engaged. Check that
the wearface of the transducer is clean and free of any debris.
②
Press the
key to activate the probe zero mode.
③
Use the
key and the
key to scroll to the probe model currently being used. Be sure to set the
right probe model to the instrument. Otherwise, there will be erroneous.
④
Apply a single droplet of ultrasonic couplant to the face of the metal probe-disc.
⑤
Press the transducer against the probe disc, making sure that the transducer sits flat against the
surface.
⑥
Remove the transducer from the probe disc.
At this point, the instrument has successfully calculated its internal error factor, and will compensate for
this value in any subsequent measurements. When performing a “probe zero”, the instrument will always
use the sound velocity value of the built-in probe-disc, even if some other velocity value has been
entered for making actual measurements. Though the instrument will remember the last “probe zero”
performed, it is generally a good idea to perform a “probe zero” whenever the gauge is turned on, as well
as any time a different transducer is used. This will ensure that the instrument is always correctly zeroed.
Press
while in probe zero mode will stop current probe zero operation and return to the
measurement mode.
4.4 Sound Velocity Calibration
In order for the gauge to make accurate measurements, it must be set to the correct sound velocity for
the material being measured. Different types of material have different inherent sound velocities. If the
gauge is not set to the correct sound velocity, all of the measurements the gauge makes will be
erroneous by some fixed percentage. The One-point calibration is the simplest and most commonly used
calibration procedure optimizing linearity over large ranges. The Two-point calibration allows for greater
accuracy over small ranges by calculating the probe zero and velocity.
Notes
:
One and Two point calibrations must be performed on material with the paint or coating removed.
Failure to remove the paint or coating prior to calibration will result in a multi material velocity
calculation that may be different from the actual material velocity intended to be measured.
4.4.1 Calibration to a known thickness
Notes:
This procedure requires a sample piece of the specific material to be measured, the exact
thickness of which is known, e.g. from having been measured by some other means.
①
Perform a Probe-Zero.
②
Apply couplant to the sample piece.
③
Press the transducer against the sample piece, making sure that the transducer sits flat against the
surface of the sample. The display should show some thickness value, and the coupling status indicator
should appear steadily.
④
Having achieved a stable reading, remove the transducer. If the displayed thickness changes from the
value shown while the transducer was coupled, repeat step 3.
⑤
Press the
key to activate the calibration mode. The MM (or IN) symbol should begin flashing.
⑥
Use the
key and the
key to adjust the displayed thickness up or down, until it matches the
thickness of the sample piece.
⑦
Press the
key again. The M/S (or IN/
μ
S) symbols should begin flashing. The gauge is now
displaying the sound velocity value it has calculated based on the thickness value that was entered.
Press the
key once again to exit the calibration mode and return to the measurement mode. The
gauge is now ready to perform measurements.