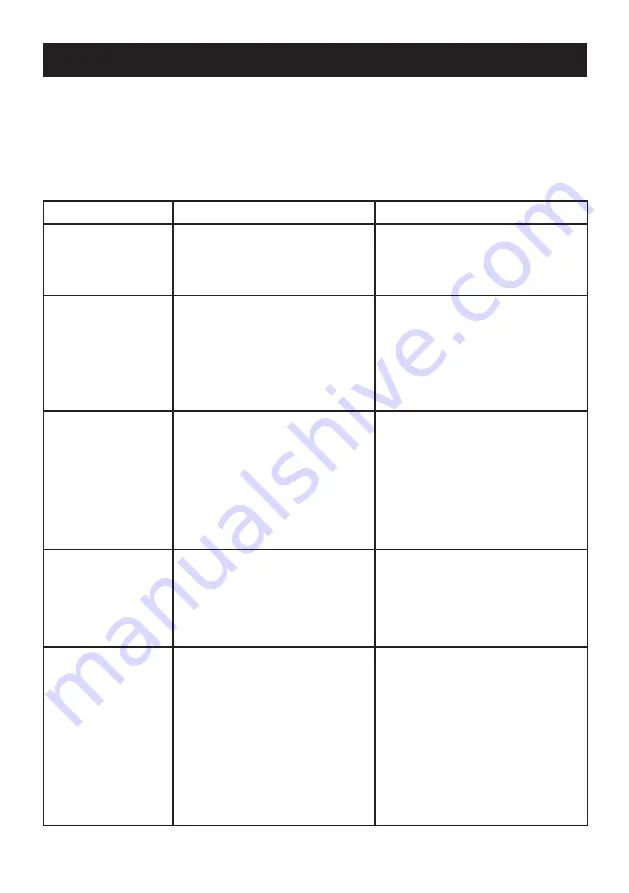
23
1079321-W2-G
OPERATION
with an adjustable maximum temperature
setting. This must be checked and adjusted
as necessary to suit both site conditions
and user’s comfort.
1.
Turn the outer flow control knob
until the desired flow of water is
obtained. The flow of water will
increase the further the control is
turned
anticlockwise
.
2.
Turn the inner temperature control
anticlockwise for warmer water
and clockwise for cooler water,
the numbers indicate the relative
temperature:
1
= cold,
4
= tepid,
7
= Hot
Warning!
Operation of the override
button will allow a shower temperature
above the preset maximum.
3.
To override the preset maximum
temperature press the override button
and turn the inner temperature control
knob anticlockwise.
4.
clockwise
Outer Flow Control Knob
Inner Temperature Control Knob
Cooler
Warmer
Press the Override Button and turn
the Inner Temperature Control Knob
anticlockwise.
Outer Flow Control Knob
Off Position
For safety reasons this appliance is fitted
Turn the outer flow control knob fully
to stop the flow of water.
FAULT DIAGNOSIS
Fault Diagnosis - User Maintenance
The appliance is fully performance tested after assembly. Providing it has been
unlikely event that you experience problems with your appliance then the following
person responsible for installing your shower.
Malfunction
Cause
Remedy
Maximum
showering
temperature too
hot.
Maximum temperature
incorrectly set.
Reset maximum temperature,
refer to
COMMISSIONING
.
Shower
temperature too
cold.
Hot water cylinder
temperature less than 12 °C
above shower temperature.
Maximum temperature
incorrectly set.
Adjust cylinder temperature.
Note!
It is recommended
stored water temperatures do
not exceed
65 °C
.
Reset maximum temperature,
refer to
COMMISSIONING
.
Blend temperature
unstable.
Spray plate blocked.
Isolating valve partially
closed.
Plumbing system fault.
Clean spray plate, refer to the
instruction manual supplied
with the
Contact your installer.
Open valve.
Contact your installer.
Pump does not
operate.
Electrical supply failure.
PCB or Potentiometer failure.
Motor overheated, thermal
switch operated.
Contact your installer.
Contact your installer.
If the thermal switch operates
repeatedly contact customer
support for further advice.
Low or no water Isolating valves closed.
Appliance sited above cold
water storage cistern.
Plumbing system fault
(airlock).
Open the isolating valves.
Contact your installer.
Contact your installer.
The appliance is not suitable
for negative head installations,
refer to
INSTALLATION
REQUIREMENTS
.
Contact your installer.
correctly installed and is operated as advised, difficulties should not arise. In the
procedure will enable you to undertake basic fault finding before contacting the
Inlet filters blocked.
shower fittings.
flow.
Inlet filters blocked.
Check valve fitted incorrectly.
Summary of Contents for 1.1532.327
Page 30: ...30 1079321 W2 G NOTES...
Page 31: ...31 1079321 W2 G NOTES...