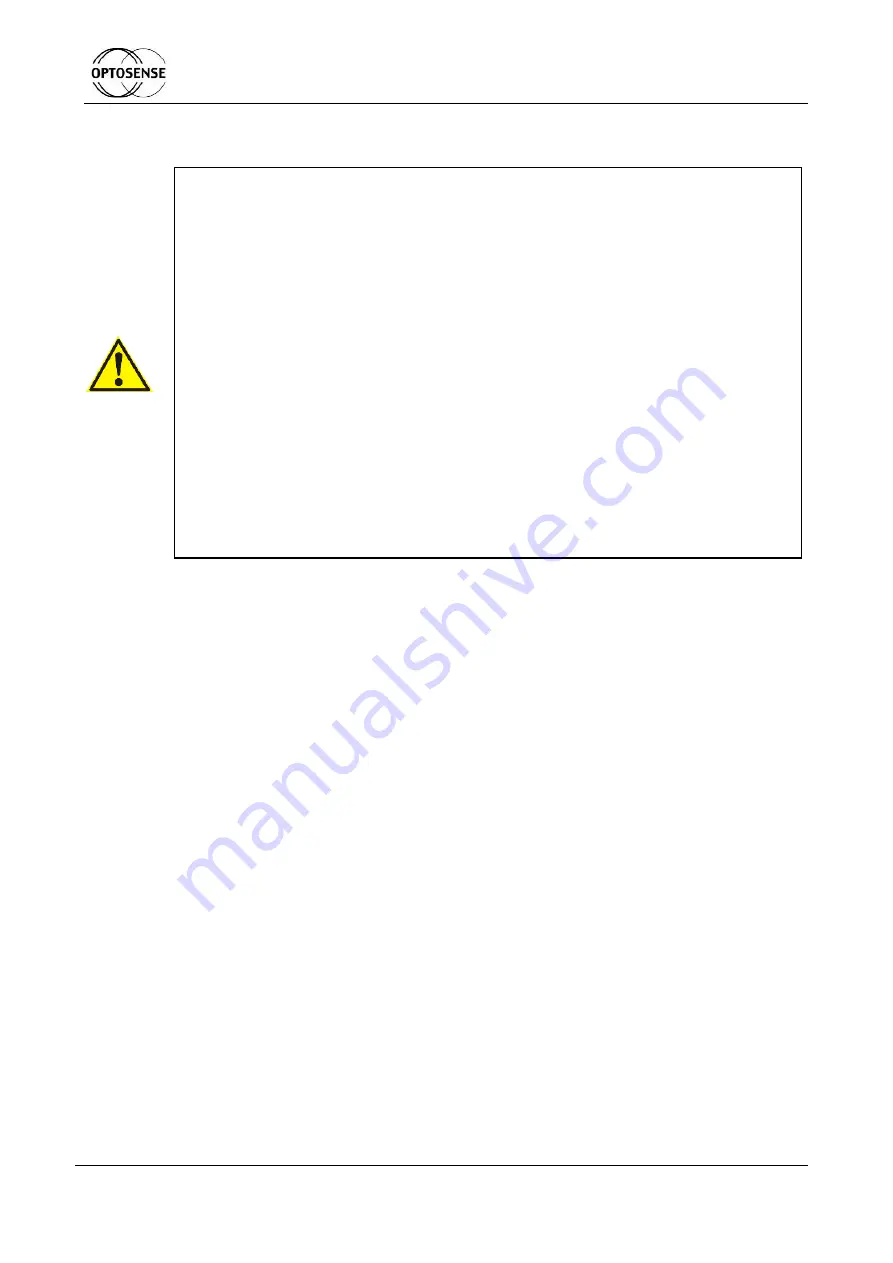
OPTOSENSE LLC
Design Department
USER
MANUAL
SMALL-SIZE EXPLOSIVE GAS MEASURING SENSOR MIPEX-02-
Х-X-X.1 X
File name: ESAT.413347.006 UM v.2.0.docx
Revision 2.0 27 August 2015
Page. 10 of 38
THE SOLE PROPERTY OF OPTOSENSE LLC.
ANY REPRODUCTION
WITHOUT THE WRITTEN PERMISSION OF OPTOSENSE LLC IS PROHIBITED.
5. INSTALLATION AND SERVICES
5.1
Preparation
5.1.1 If the sensor has been kept in the transportation package at temperature lower than
0
0
C, hold it at temperature of 10
–35
0
C for at least one hour.
5.1.2 Remove the packing. Check presence of the certification marking, ensure absence
of mechanical injuries.
5.2
Installation
Use intrinsic safety connection (see Appendix B for details).
5.2.1 Use the following recommended sockets for the sensor connection or similar:
Cambion 450-3729-01-06-00;
Harwin H3183-05;
Harwin H3182 (for the MIPEX-02-X-X-X.1 A modification).
Sensor pinout is shown in Fig. 1 of Appendix A.
5.2.2 Provide intrinsically safe power supply to the sensor from power sources featuring
nominal range of output DC voltage of not less than 3 V and not more than 5 V,
output power (P0)
– not less than 0.02 W and not more than 0.25 W in accordance
with requirements of standards IEC 60079
–0:2004, IEC 60079–11:2006.
5.2.3 The transceiver of UART interface should meet the requirements of standards
IEC 60079
–0, IEC 60079–11.
Communication parameters of UART- transceiver are following:
- HIGH logic level for transmit line
TxD
is 2.8V;
- HIGH logic level for receive line
RxD
should be in range between 2.8V and 3.3 V;
Models MIPEX-02-X-X-3.1 X are potential electrostatic charging hazard
–
clean them with a damp cloth only. Take it into account during installation
and operation of the sensor in end-user equipment.
The MIPEX-02-X-X-1.1 X and MIPEX-02-X-X-2.1 X models of the
equipment were tested and found to hold 17.4pF maximum capacitance.
Connection should be made via PCB sockets. Soldering to the pins will
seriously damage the sensor.
Excessive force on sensor housing is not allowed. For the metal housing -
no more than 2 MPa applied to reflecting cover center or on at any point of
middle part side surface and no more 100 MPa applied to boundary of
reflecting cover. For the plastic housing - no more than 20 kPa applied to
reflecting cover center or on at any point of side surface and no more 2
MPa applied to boundary of reflecting cover.
Metrological properties are not supported in ambient temperature gradient
faster than 0.6
⁰
C/min.
Set manual zeroing procedure after continues storage or transportation.