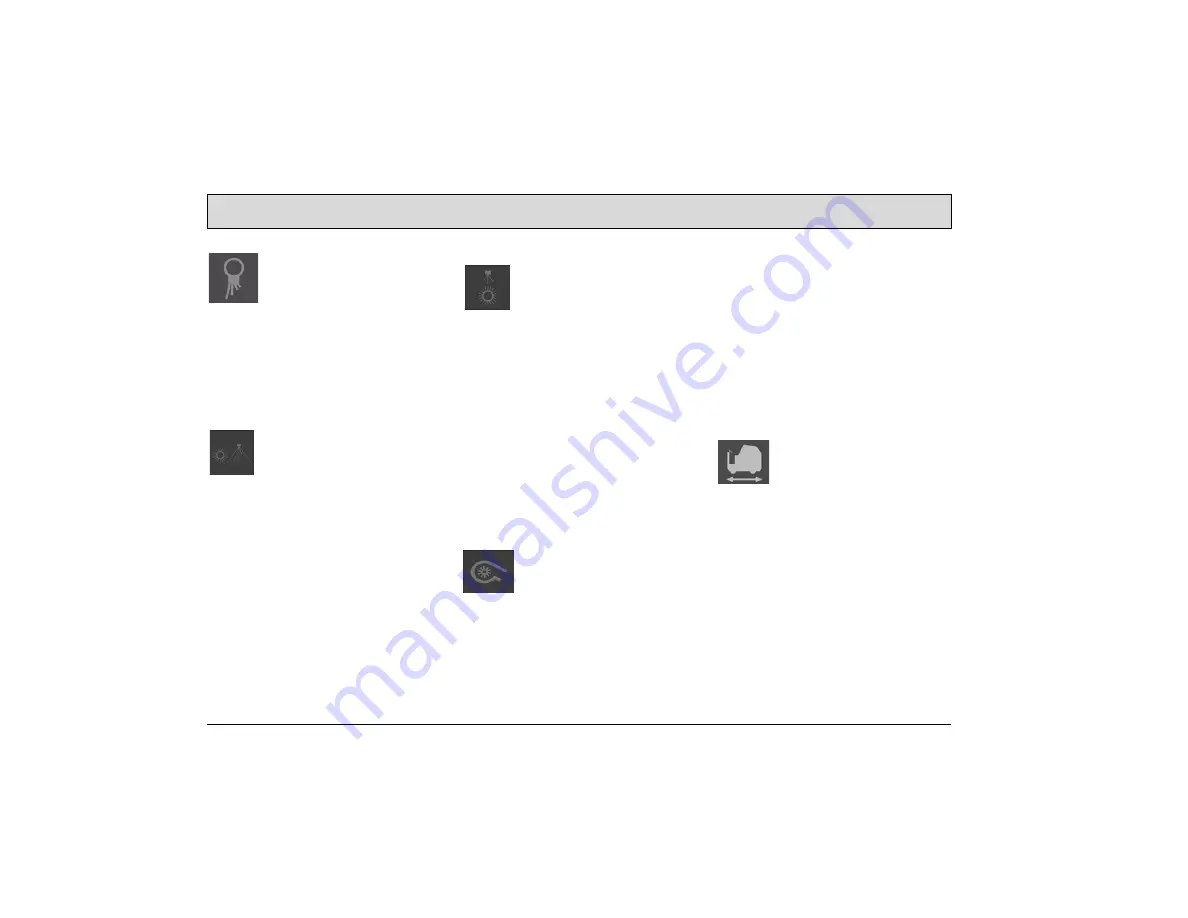
18
Operating and Indicating Elements
Off Aisle Wand mode(Fig. 5/9)
This mode is for cleaning areas that can
not be reached with the machine. When
selected, the vacuum motors will turn
on and the solution pump will run when
the triger of the off aisle wand is activat-
ed. The machine will not move.
Restorative Clean mode(Fig. 5/8)
When this mode is selected the solution
will pump to the four spray jets in front
of the scrub deck. When the operator
selects
forward
and presses the accel-
erator the scrub deck will automatically
come down, the brush motors will turn
on, the vacuum motors will turn on, the
solution pump and interim solenoid will
turn on. If the operator selects
reverse
the scrub deck will raise, the brush mo-
tor, solution pump and interim solenoid
will turn off. The vacuum motors will
continue to run for 20 seconds to clear
the vacuum hoses.
Interim Clean mode(Fig. 5/7)
When this mode is selected the solution
will pump to the single spray jet aimed
on to the front scrub brush. When the
operator selects
forward
and presses
the accelerator the scrub deck will auto-
matically come down, the brush motors
will turn on, the vacuum motors will turn
on, the solution pump and interim sole-
noid will turn on. If the operator selects
reverse
the scrub deck will raise, the
brush motor, solution pump and interim
solenoid will turn off. The vacuum mo-
tors will continue to run for 20 seconds
to clear the vacuum hoses.
Vacuum only mode(Fig. 5/11)
This mode is recommended for solution
removal after double scrubbing, but can
also be used to pick up spills. When the
accelerator pedal is activated with the
direction selector in the forward posi-
tion, the rear brush deck will lower to the
floor as the vacuum motor turns on pull-
ing the dirty solution water from the vac-
uum shoes into the recovery tank. If the
machine stops moving and the direction
selector is switched to reverse, the
brush deck will raise (protecting it from
damage) and the vacuum motor will
turn off after a delay. If the machine
stops moving in either direction, the
brush deck will automatically raise and
the vacuum motor will shut off after a
delay.
Transport mode(Fig. 5/12)
When this mode is selected, none of the
cleaning functions will operate. This
mode is only used to transport the ma-
chine from one location to another.