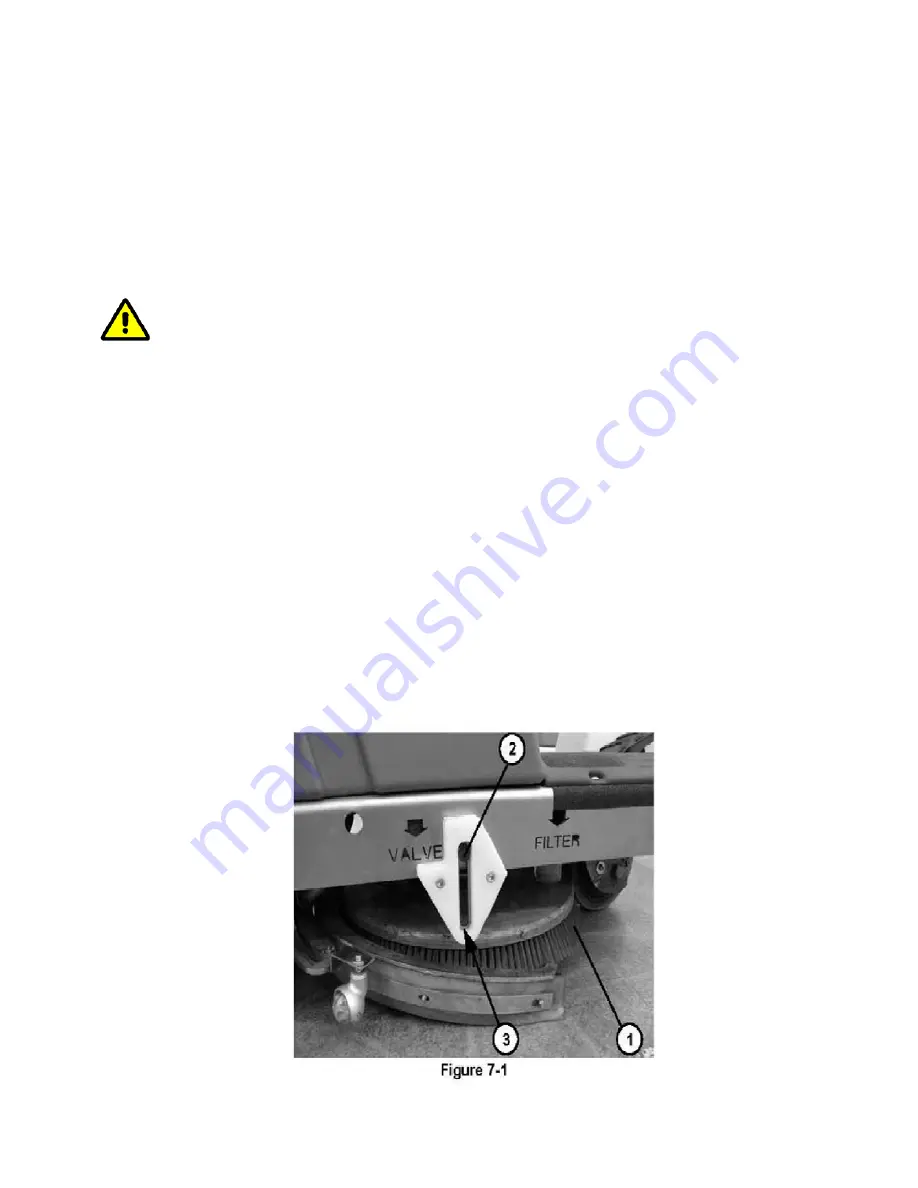
CHAPTER 7
BRUSH SYSTEM
•The significant maintenance/replacement procedures relating to the Brush
system are described in this chapter.
•In addition troubleshooting is described in the final section.
7.1 CLEANING DISC BRUSHES
CAUTION! The use of work gloves is
recommended when cleaning the disc brush, due to the
possible presence of sharp debris.
1
Remove the disc brush (See the procedure in the User and Maintenance
1.
Remove the disc brush (See the procedure in the User and Maintenance
Manual ).
2.
Wash and clean the disc brush (1,
Figure 7-1
) of dirt and debris; use
water and detergent solution.
3.
Fit the disc brush (See the procedure in the User and Maintenance
Manual ).
Manual ).
4.
The disc brush must be replaced due to excessive wear, when in the
condition of brush lowered, the side pins (2,
Figure 7-1
) rest on the lower
ends (3) of the slots.
Summary of Contents for ERide 21
Page 12: ......
Page 14: ...Figure 3 2 ...
Page 15: ......
Page 16: ......
Page 17: ......
Page 19: ......
Page 22: ......
Page 26: ......
Page 28: ......
Page 34: ......
Page 39: ......
Page 42: ......
Page 46: ......
Page 49: ......
Page 55: ......
Page 59: ......
Page 62: ......
Page 65: ......
Page 67: ......
Page 71: ......
Page 81: ...11 4 Fuses ...
Page 84: ......
Page 87: ...11 9 ALARM CODES ...
Page 89: ......
Page 90: ...12 Relays and Drive Controller ...
Page 91: ...13 Notes ...