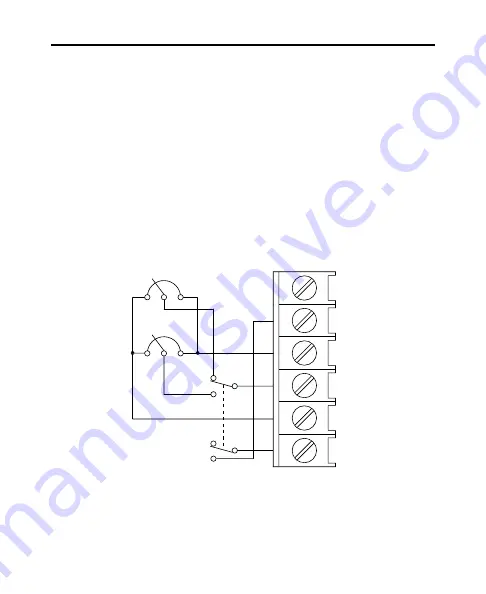
51
Application Notes
Independent adjustable speeds with DIR switch
Replace the speed adjust potentiometer with two single-
pole multi-position switches, and two or more
potentiometers in parallel, with a total parallel resistance of
10K ohms. Figure 25 shows the connection of two
independent speed adjust potentiometers that can be
mounted at two separate operating stations.
E2
E1
S1
S2
D (DIRECTION)
S3
FORWARD
REVERSE
TB501
REVERSE
SPEED
FORWARD
SPEED
20K OHM
20K OHM
Figure 25. Independent Adjustable Speeds