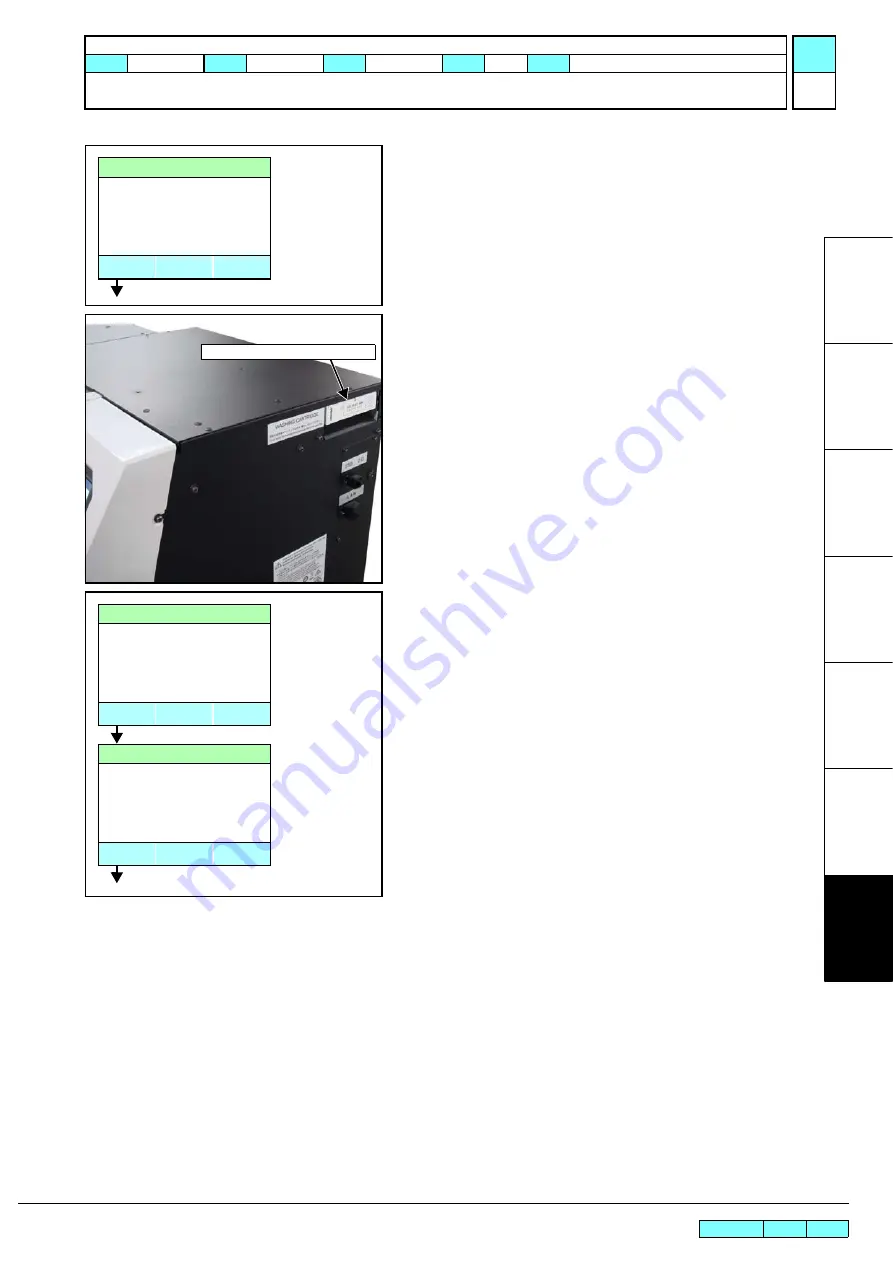
© 2014 MIMAKI ENGINEERING CO.,LTD.
7.1
P.5
7.1 Performing the Initial Ink Fill
R.1.2
14. Select whether or not to fill up the maintenance liquid.
(Displayed only when [AQUA] is selected for ink type)
If you selected cancel, proceed to Step 18.
15. Set the removed filling maintenance washing cartridge to the
washing cartridge of the right side of main unit.
16. Press the [ENTER] key, and start fill up the rout of the
maintenance washing liquid.
Fill up MAINT.LIQUID
○
EXECUTE
○
CANCEL
A confirmation screen is
displayed only when
[AQUA] is selected for
ink type.
Maintenance washing cartridge
Fill up MAINT.LIQUID
Start
Fill up MAINT.LIQUID
Filling up
Please wait…
INSTALLATION GUIDE > Outputting Plots > Performing the Initial Ink Fill
Model
JV300
Issue
2014.04.11
Revised 2014.06.19 F/W ver. 1.00 Remark
1.2
Summary of Contents for JV300-130 A
Page 2: ......
Page 57: ...MEMO ...
Page 58: ...MEMO ...
Page 59: ...MEMO ...
Page 60: ...D500939 13 19062014 2014 MIMAKI ENGINEERING CO LTD IT FW 1 3 ...