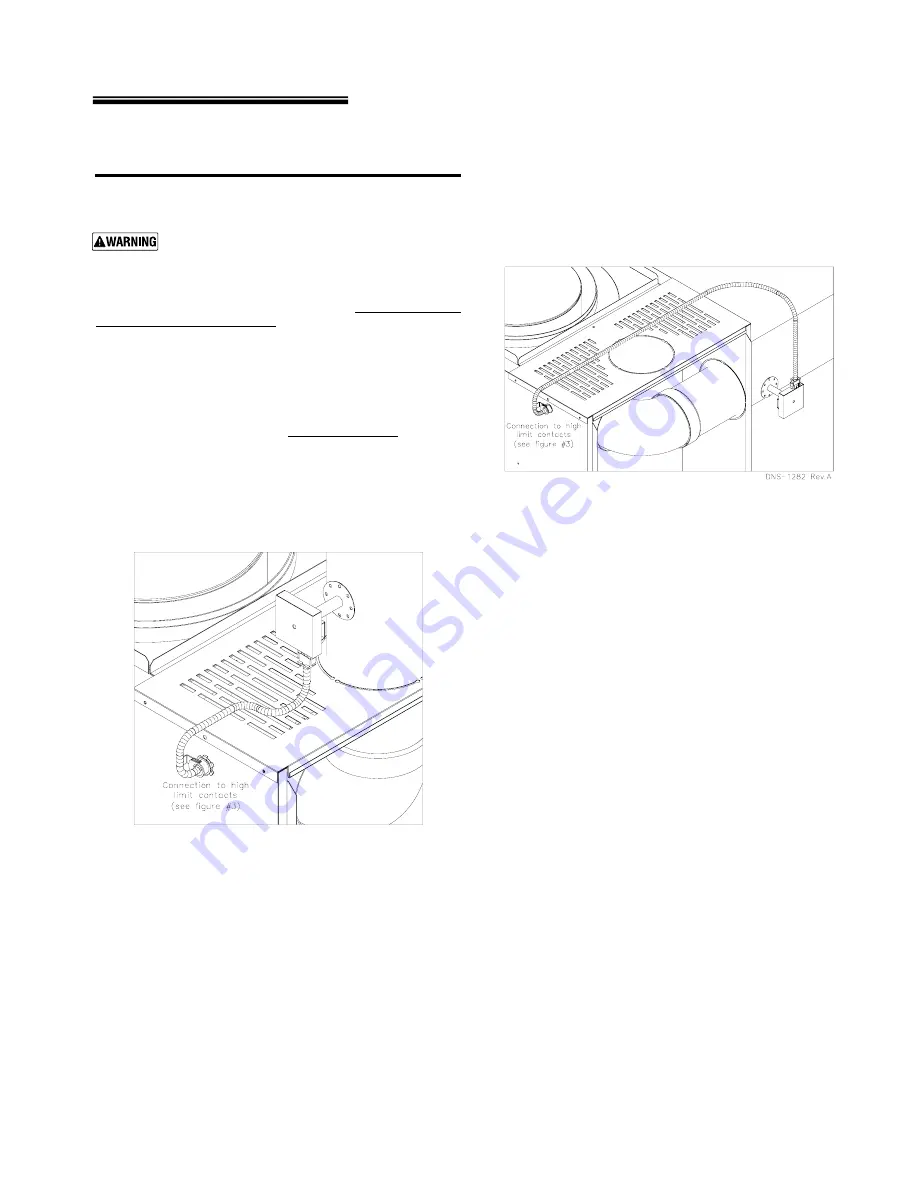
THB & TLB
Oil Furnaces
–
Furnace Manual
670-000-005/1010
7
2
Prepare furnace and place in position
Blocked Vent Shut-Off (BVSO) for chimney venting
(OPTIONAL)
It is imperative that this device be installed by a
qualified agency.
This device is designed to detect the insufficient evacuation of
combustion gases in the event of a vent blockage. In such a case
the thermal switch will shut down the oil burner. The device will then
need to be re-armed MANUALLY.
In the event that the BVSO repetitively shuts down the oil burner, a
qualified technician needs to evaluate the cause of this shut down.
Refer to the figures 3 to 5 at section 6, Wiring Diagrams and detailed
instructions supplied with the BVSO for the installation and wiring
procedures.
It is also essential the the BVSO be maintained annually.
For more details refer to the instructions supplied with the device
itself, as well as the Maintenance Section.
Figure 1
Blocked Vent Shutt-Off device wiring
Installation : Upflow with Vertical exhaust
(Optional)
Figure 2
Blocked Vent Shutt-Off device wiring
Installation : Upflow with Horizontal exhaust
(Optional)
Summary of Contents for THB High Boy series
Page 35: ......
Page 36: ...THB TLB Oil Furnaces Furnace Manual X40108 Rev J ...