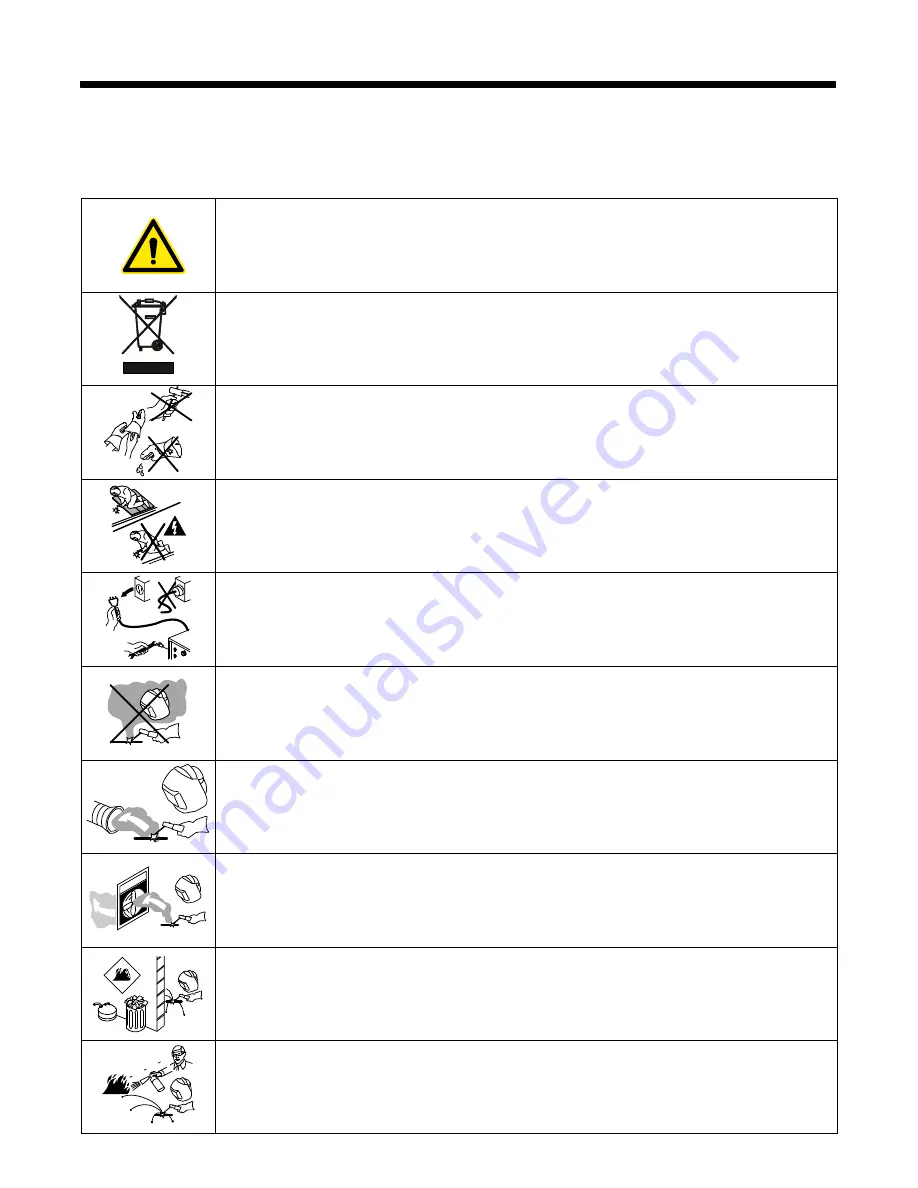
OM-263 706 Page 5
SECTION 2 − DEFINITIONS
2-1.
Additional Safety Symbols And Definitions
.
Some symbols are found only on CE products.
Warning! Watch Out! There are possible hazards as shown by the symbols.
Safe1 2012−05
Do not discard product (where applicable) with general waste.
Reuse or recycle Waste Electrical and Electronic Equipment (WEEE) by disposing at a designated collection
facility.
Contact your local recycling office or your local distributor for further information.
Safe37 2012−05
Wear dry insulating gloves. Do not touch electrode with bare hand. Do not wear wet or damaged gloves.
Safe2 2012−05
Protect yourself from electric shock by insulating yourself from work and ground.
Safe3 2012−05
Disconnect input plug or power before working on machine.
Safe5 2012−05
Keep your head out of the fumes.
Safe6 2012−05
Use forced ventilation or local exhaust to remove the fumes.
Safe8 2012−05
Use ventilating fan to remove fumes.
Safe10 2012−05
Keep flammables away from welding. Do not weld near flammables.
Safe12 2012−05
Welding sparks can cause fires. Have a fire extinguisher nearby, and have a watchperson ready to use it.
Safe14 2012−05
Summary of Contents for STi 270
Page 26: ...OM 263 706 Page 22 Figure 7 2 Circuit Diagram For STi 270C 956172129_A ...
Page 41: ......
Page 42: ......