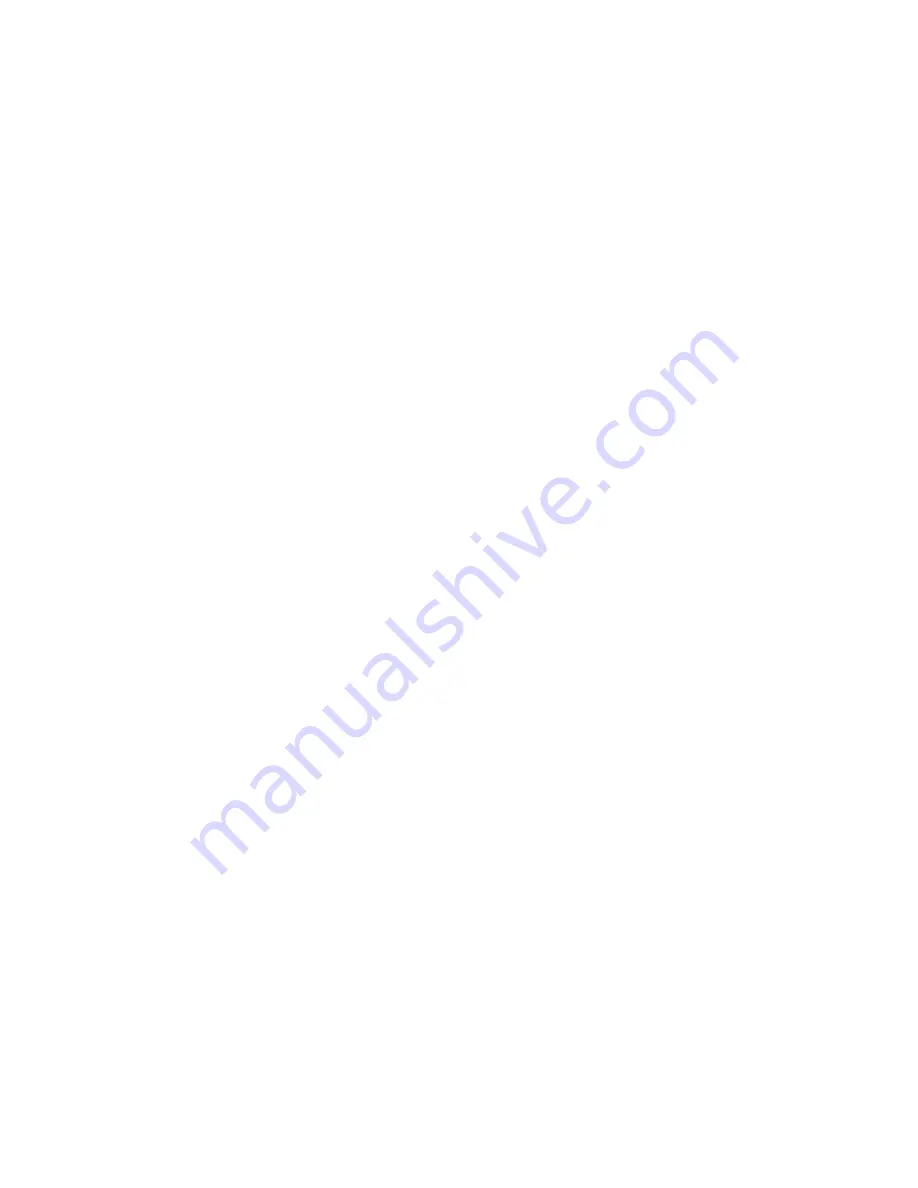
OM-246 466 Page 49
7-2. Troubleshooting Welding Power Source/Wire Feeder Issues
If the welding power source and wire feeder are NOT responding after everything is connected, follow the items listed below before
contacting the nearest factory-authorized service agent:
Welding power source is plugged in and there is no power after turning on unit.
S
If unit is directly connected to a line disconnect box or plugged into a receptacle from a line disconnect box, be sure
that the line disconnect switch or main breaker is in the ON position.
Wire feeder has no power when turned on.
S
Check if the 72-socket plug is connected to the receptacle on rear of welding power source, and check that the
14-pin plug from the wire feeder is connected to the matching receptacle on rear of welding power source.
Wire does not feed from wire feeder to end of gun.
S
Check to see if wire diameter matches the groove size of the drive rolls.
S
Check if tension on drive rolls is too loose or too tight.
S
Check if gun liner is the correct size for the wire size.
S
Check if contact tip is correct size for the wire size, and that end of contact tip is not plugged.
S
Check if gun end is fully inserted into wire drive housing at feeder, and knob is tightened down to secure gun end.
Weld is not consistent from one welding application to another.
S
Be sure that ground is connected to a clean, paint-free area of pipe; otherwise, grind an area if necessary to make
a good ground connection.
S
Keep ground as close as possible to joint being welded.
S
Check if volt sensing lead is connected to the welding power source and that ground connection is secure. Check
for any frayed wires at ground end of volt sensing lead that may prevent a good connection.
S
Be sure that volt sense lead shielding is not touching center conductor.
S
Be sure that wire feeder control cable and volt sensing lead are separated from weld cables.
S
Be sure gun angle during welding is straight in to 15 degrees back at joint.
S
Follow recommended settings in Operation section of manual to select a starting point for welding.
S
Recommended joint preparation and fit-up is 1/32-1/16 in (0.8-1.6 mm) land and a 1/8 in (3.2 mm) root opening.
Porosity in weld bead.
Check shielding gas supply that there is enough gas and supply is turned on.
Check shielding gas flow rate at regulator.
Check that gas pressure to the wire feeder does not exceed 90 psi (621 kPa).
Check all shielding gas fitting and tighten if necessary.
Remove gun end from wire drive housing and check condition of O-rings. Replace any worn or missing O-rings.
Check power pin end of gun and tighten with a wrench.
Be sure that gun end is fully inserted into wire drive housing and knob is tightened down to secure gun end.
Check and clean shielding gas nozzle on gun.
Trouble feeding wire when welding. Check drive rolls and wire guides to make sure they match the wire style
and size.
Check drive roll tension and readjust if necessary.
Be sure that gun end is fully inserted into wire drive housing and knob is tightened down to secure gun end.
Check if hub tension at wire spool is too tight or too loose and readjust if necessary.
Be sure that welding gun cable is as straight as possible from wire feeder to workpiece.
Check if contact tip is correct size for the wire size, and that end of contact tip is not plugged.
Check if gun liner is the correct size for the wire size and liner is not dirty or damaged. Clean or replace gun liner if necessary.
Summary of Contents for OM-246 466B
Page 14: ...OM 246 466 Page 10...
Page 63: ...OM 246 466 Page 59 Notes...
Page 65: ...OM 246 466 Page 61 243 024 B...
Page 74: ...Notes...