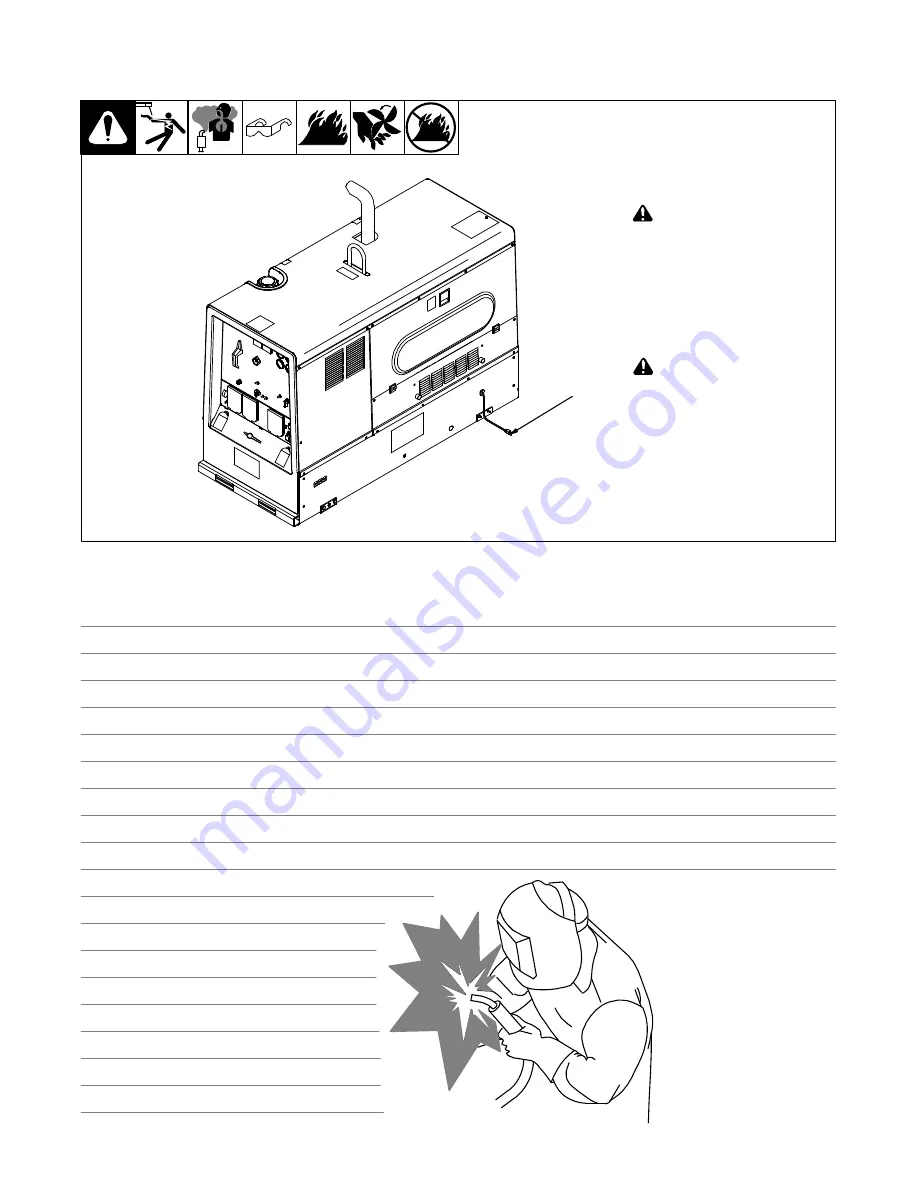
Complete Parts List available at www.MillerWelds.com
OM-4421 Page 39
7-6. Optional Oil Pan Heater Operation
Oil heater1 2012
−
05 803 602 / Ref. 803 145
1
Oil Pan Heater Plug
Use heater to maintain a constant
engine oil temperature.
To turn on heater, connect heater
plug to 120 volts AC receptacle.
Heater rated at 300 watts.
!
Do not run engine while oil
pan heater is on.
NOTICE
−
In extremely cold weath-
er, heater should be connected to
120 volts AC power source when
engine oil is warm to eliminate pos-
sibility of oil coking on heater.
Severe coking on heater element
may cause damage to engine, en-
gine oil, and oil pan heater.
!
The area near the oil pan
heater gets hot.
Disconnect plug to turn off heater.
1
Notes
Work like a Pro!
Pros weld and cut
safely. Read the
safety rules at
the beginning
of this manual.
Summary of Contents for 907186
Page 6: ......
Page 20: ...OM 4421 Page 14 ...
Page 63: ... Complete Parts List available at www MillerWelds com OM 4421 Page 57 Notes ...
Page 65: ...OM 4421 Page 59 240 152 B ...
Page 66: ...OM 4421 Page 60 Figure 11 2 Circuit Diagram For CC CV Welder Generator ...
Page 67: ...OM 4421 Page 61 240 153 B ...
Page 77: ...OM 4421 Page 71 Notes ...
Page 78: ...OM 4421 Page 72 Notes ...