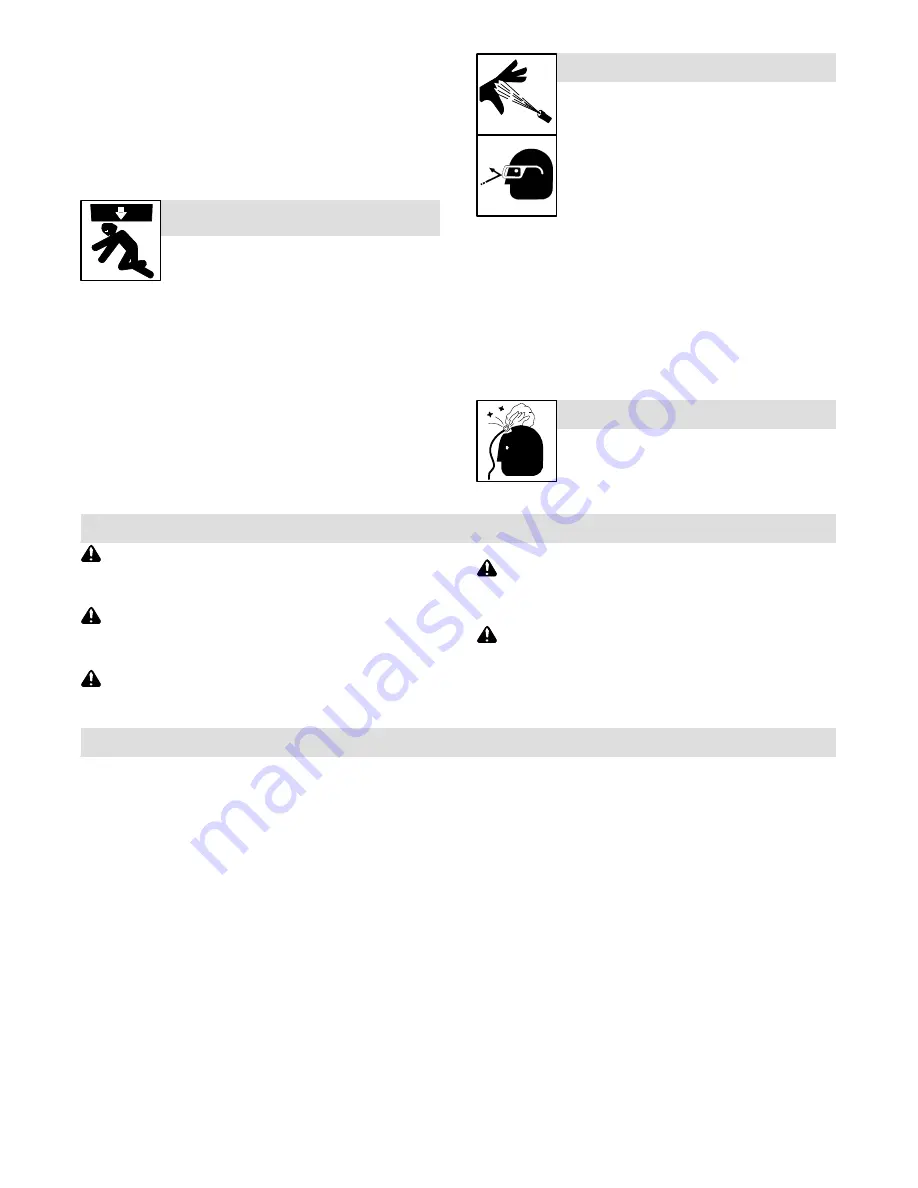
TM-268 819 Page 3
Belt Drive Generator
D
HYDRAULIC FLUID is FLAMMABLE−−do not work on hydraulics
near sparks or flames; do not smoke near hydraulic fluid.
D
Reinstall doors, panels, covers, or guards when servicing is
finished and before starting unit.
D
If ANY fluid is injected into the skin, it must be surgically removed
within a few hours by a doctor familiar with this type of injury or gan-
grene may result.
COMPRESSED AIR EQUIPMENT can
injure or kill.
D
Before working on compressed air system, turn
off and lockout/tagout unit, release pressure,
and be sure air pressure cannot be accidentally
applied.
D
Do not work on compressed air system with unit running unless
you are a qualified person and following the manufacturer’s in-
structions.
D
Do not modify or alter compressor or manufacturer-supplied
equipment. Do not disconnect, disable, or override any safety
equipment in the compressed air system.
D
Keep away from potential pinch points or crush points created by
equipment connected to the compressed air system.
D
Do not work under or around any equipment that is supported only
by air pressure. Properly support equipment by mechanical
means.
COMPRESSED AIR can injure or kill.
D
Before working on compressed air system,
turn off and lockout/tagout unit, release pres-
sure, and be sure air pressure cannot be acci-
dentally applied.
D
Relieve pressure before disconnecting or con-
necting air lines.
D
Check compressed air system components
and all connections and hoses for damage,
leaks, and wear before operating unit.
D
Do not direct air stream toward self or others.
D
Wear protective equipment such as safety glasses, hearing pro-
tection, leather gloves, heavy shirt and trousers, high shoes, and a
cap when working on compressed air system.
D
Use soapy water or an ultrasonic detector to search for
leaks−−never use bare hands. Do not use equipment if leaks are
found.
D
Reinstall doors, panels, covers, or guards when servicing is
finished and before starting unit.
D
If ANY air is injected into the skin or body seek medical help imme-
diately.
TRAPPED AIR PRESSURE AND WHIPPING
HOSES can injure.
D
Release air pressure from tools and system be-
fore servicing, adding or changing attach-
ments, or opening compressor oil drain or oil fill
cap.
1-3.
California Proposition 65 Warnings
Welding or cutting equipment produces fumes or gases
which contain chemicals known to the State of California to
cause birth defects and, in some cases, cancer. (California
Health & Safety Code Section 25249.5 et seq.)
Battery posts, terminals and related accessories contain lead
and lead compounds, chemicals known to the State of
California to cause cancer and birth defects or other
reproductive harm. Wash hands after handling.
This product contains chemicals, including lead, known to
the state of California to cause cancer, birth defects, or other
reproductive harm. Wash hands after use.
For Gasoline Engines:
Engine exhaust contains chemicals known to the State of
California to cause cancer, birth defects, or other reproduc-
tive harm.
For Diesel Engines:
Diesel engine exhaust and some of its constituents are
known to the State of California to cause cancer, birth
defects, and other reproductive harm.
1-4.
EMF Information
Electric current flowing through any conductor causes localized electric
and magnetic fields (EMF). The current from arc welding (and allied pro-
cesses including spot welding, gouging, plasma arc cutting, and
induction heating operations) creates an EMF field around the welding
circuit. EMF fields may interfere with some medical implants, e.g. pace-
makers. Protective measures for persons wearing medical implants
have to be taken. For example, restrict access for passers−by or con-
duct individual risk assessment for welders. All welders should use the
following procedures in order to minimize exposure to EMF fields from
the welding circuit:
1.
Keep cables close together by twisting or taping them, or using a
cable cover.
2.
Do not place your body between welding cables. Arrange cables
to one side and away from the operator.
3.
Do not coil or drape cables around your body.
4.
Keep head and trunk as far away from the equipment in the
welding circuit as possible.
5.
Connect work clamp to workpiece as close to the weld as
possible.
6.
Do not work next to, sit or lean on the welding power source.
7.
Do not weld whilst carrying the welding power source or wire
feeder.
About Implanted Medical Devices:
Implanted Medical Device wearers should consult their doctor and the
device manufacturer before performing or going near arc welding, spot
welding, gouging, plasma arc cutting, or induction heating operations.
If cleared by your doctor, then following the above procedures is recom-
mended.