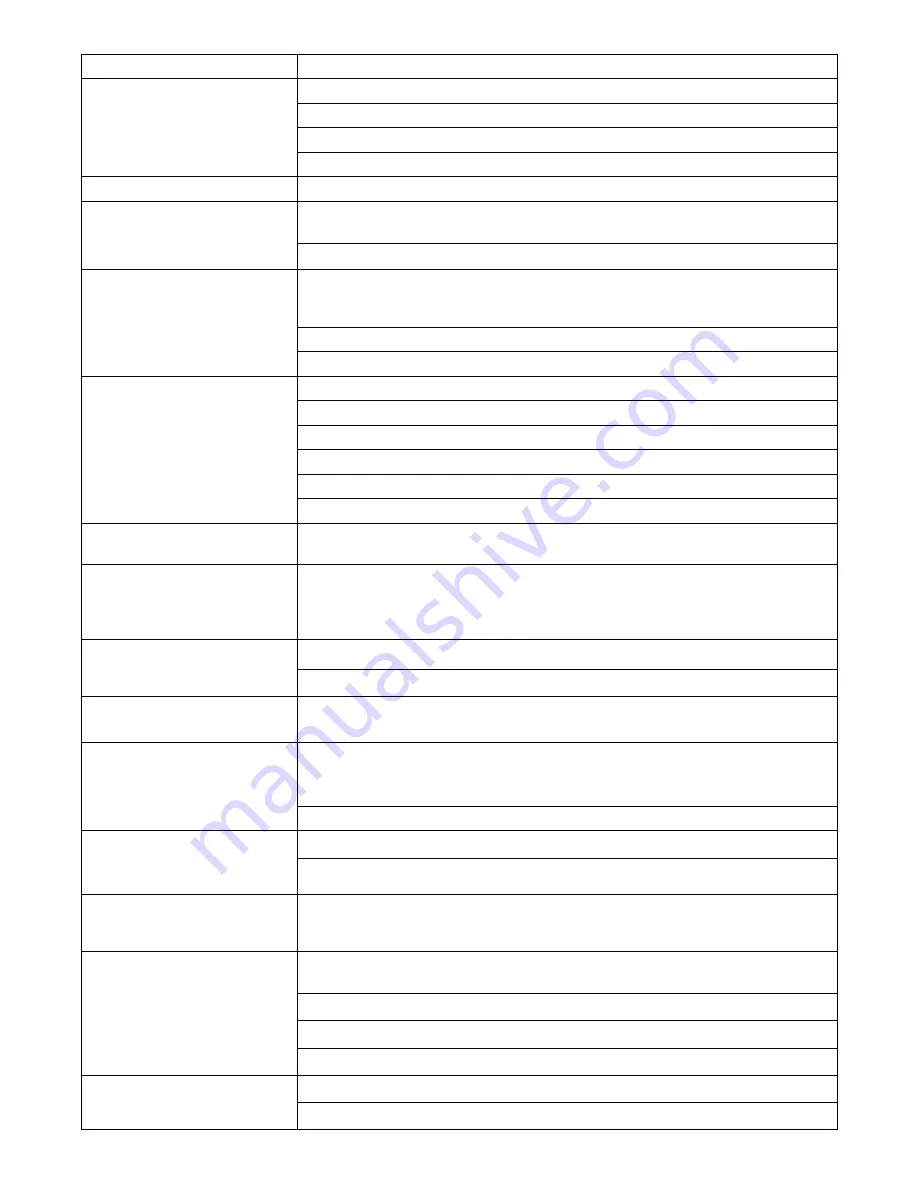
OM-237 323 Page 26
Trouble
Remedy
Motor runs slowly.
Check and replace contact tip or liner if necessary.
Have Factory Authorized Service Agent check Control board PC1.
When soft start is on, motor will run slow until weld current is sensed by HD1.
Hub tension set too high (see Section 4-12).
Unit does not switch out of Soft Start.
Check transducer HD1 and connections, and replace if necessary.
Wire feeds when Jog switch is pressed
but not when gun trigger is pressed.
Check gun trigger connection at wire feeder. Check gun trigger leads and trigger switch. See gun Owner’s
Manual.
Have Factory Authorized Service Agent check Control board PC1.
Wire stubbing on low end using a con-
stant current power source or feeder re-
sets.
Increase power source inductance setting if available.
Ensure that CC/CV switch in feeder is in CC position (see Section 5-1).
Increase output setting of power source or decrease wire feed speed.
Gas does not flow or does not stop flow-
ing; wire feeds.
Clear blockage in gas hose or replace hose.
Clear blockage in welding gun.
Clean blockage in filter (see Section 6-3).
Check gas valve.
Check coil voltage and connections of gas valve GS1. Check continuity of coil. Replace GS1 if necessary.
Have Factory Authorized Service Agent check Control board PC1.
Wire remains energized after trigger is
released.
Check contactor W1 to see if contacts are frozen closed.
Gun trigger is pressed, gas does not
flow, wire is not energized, wire feeds.
If a welding arc is not established in 3 seconds after the gun trigger is activated, the unit will feed wire
without energizing the contactor or gas valve. The unit will feed approximately 35 feet (10.7 meters) of
wire, then stop feeding. This is to prevent complete despoolling of the wire, as in the case of a damaged
gun.
Display on display board does not light.
Have Factory Authorized Service Agent check Control board PC1.
Replace display board.
Segments on the display board are
missing.
Replace display board.
Weld voltage on display board is not
accurate.
Weld voltage on the display board will show weld voltage at the feeder. Due to voltage drops in the weld
cables, weld voltage at the feeder will not match weld voltage at the welding power source. Due to aver-
aging of weld voltage, if weld time is less than 8 seconds the display weld voltage at the feeder may not
be accurate.
Check Motor Control PC1 and connections, replace if necessary.
While not welding − Voltage display al-
ternates between three dashes and
open circuit voltage.
This is normal when unit is connected to a Non−WCC compatible power source (see Section 5-1).
Unit is connected to but not associated to a WCC control or WCC compatible power source
(see Section 4-6).
While not welding − Voltage display al-
ternates between CC and open circuit
voltage.
This is normal when the CC/CV switch is set to CC mode (see Section 5-1).
Weld amperage on display board is not
accurate.
Weld amperage displayed on the feeder will not match exactly with the weld amperage displayed on the
welding power source.
Check DIP switch settings on Display board PC22 (see Section 4-13).
Check transducer HD1 and connections, and replace contactor assembly if necessary.
Check Motor Control PC1 and connections, replace if necessary.
Software and weld time information on
display board is not accurate.
Check DIP switch settings on Display board PC22 (see Section 4-13).
Check Motor Control PC1 and connections, replace if necessary.
Summary of Contents for SuitCase X-TREME 8VS WCC
Page 4: ......
Page 14: ...OM 237 323 Page 10...
Page 27: ...OM 237 323 Page 23 5 2 Gun Consumables Information 235 264 A Notes...
Page 32: ...OM 237 323 Page 28 Notes...