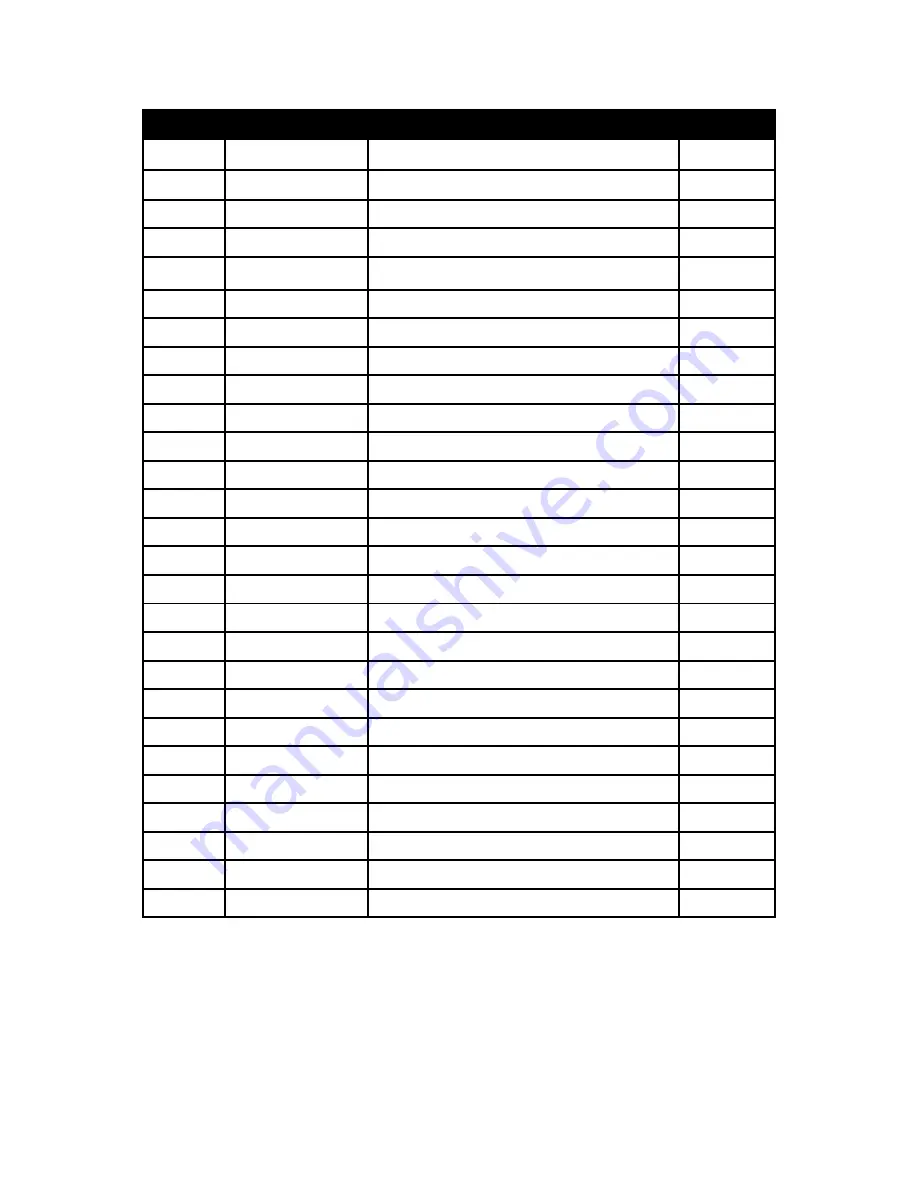
Operators Manual
37
Drive Bracket Assembly Part List
NO
Part Number
Description
QTY
1
87003001
Drive Motor
1
2
87003005
Holding screw
2
3
87003006
Wire inlet guide tube
1
4
87003002
Wire feed bracket
1
5
87003007
Shaft for drive gears
2
6
87003008
Shaft sleeve for drive gears
2
7
87003009
Drive gear
2
8
87003010
Drive gear pin
4
9
87003011
Motor drive gear
1
10
87003012
Sleeve for drive roller
2
11
87003013
Washer for drive gear
1
12
87003014
Drive roller
2
13
87003003
Washer for driving roller
2
14
87003004
Securing screw for drive roller
2
15
87003015
Pressure roller pin
2
16
87003016
Idler arm pin
2
17
87003017
Washer for pressure rollers
4
18A
87003018
Left Idler are Bracket
1
18B
87003019
Right Idler are bracket
1
19
87003020
Tension spring
1
20
87003021
Euro adaptor suit SIM
1
21
87003022
Tension adjusting screw
2
22
87003023
Tension adjusting handle
2
23
87003024
Spring for tension
2
24
87003025
Tension adjusting handle cover
2
25
87003026
Center guide tube
1
26
87003027
Central adaptor guide tube
1