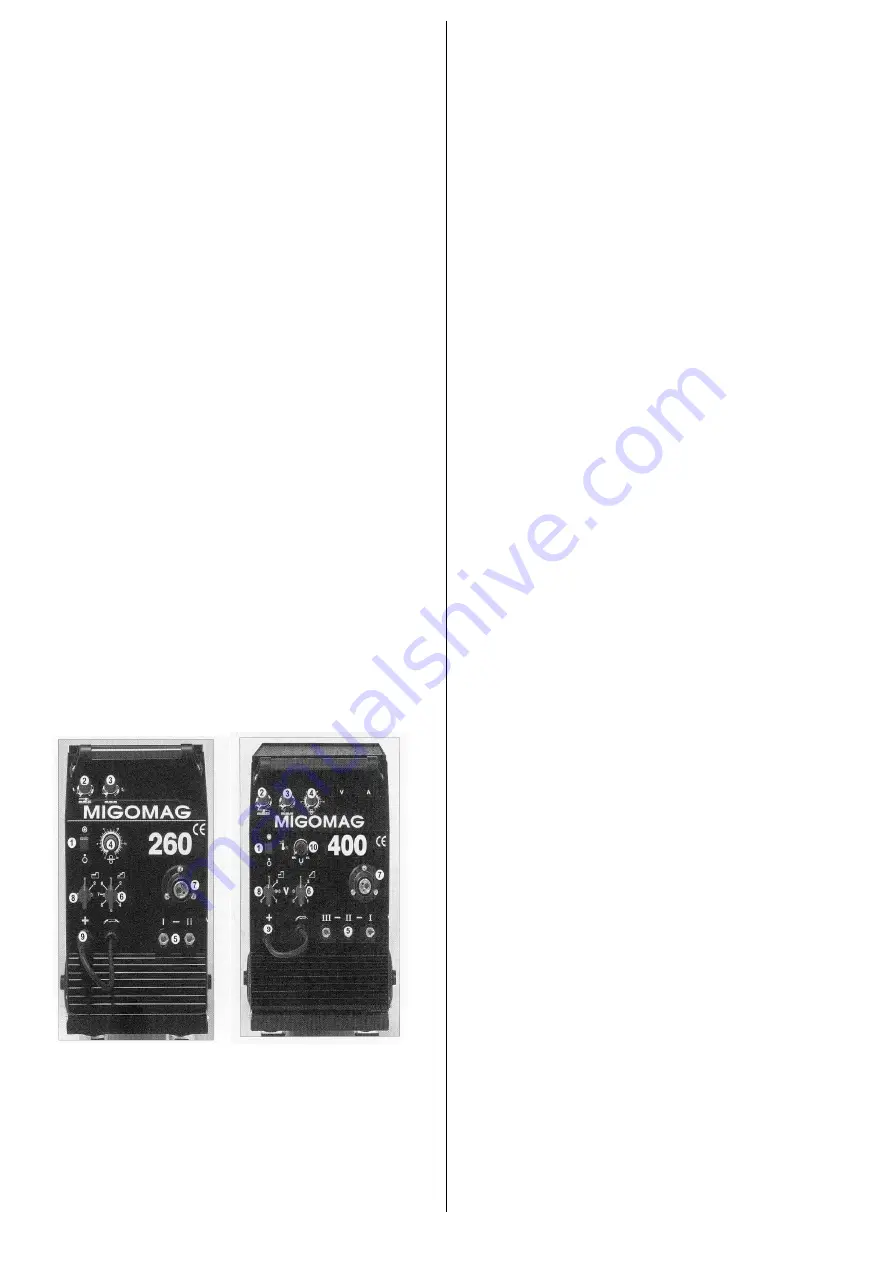
4
MACHINE CONTROLS/ CONNECTIONS
1.
ON/OFF
Switch
With
this
switch in the ON position
,
power is
applied to the fan and control circuits
.
WARNING:
This switch does not isolate the
unit from the mains electrical
supply
.
2.
t1 -'ON' TIME CONTROL for SPOT welding
and
STITCH '
ON’ time
.
3.
t2
-
'OFF' TIME
CONTROL for STITCH 'OFF'
time. M260
,
M300
,
M350,
M400
only
.
4.
WIRE FEED SPEED (Current Control)
.
5.
NEGATIVE
CONNECT
ION
i.
In
ductance
Socket-
Lo
w
.
ii.
Inductance Socket Med High
iii.
Inductanc
e
Socket High
6. VOLTAGE SELECTOR SWITCH Fine
7.
CENTRAL ADAPTOR.
8. VOLTAGE
SE
LE
CTOR
SWITCH Coarse
.
9.
POSITIVE CONNECTION
.
10. BURNBACK CONTROL
Welding Voltage Adjustment
MIGOMAG
260
Th
e welding voltage
is regulated by a
2-position
switch
for
course
control
and an 8-position sw
i
tch for fin
e
control
,
a
total
of 16
.
Position (8)
a
nd
(6)
on
the
front
pane
l.
MIGOMAG 400
The welding voltage is
reg
ula
ted by
a 6-position switch
for course control
and
a 6-position switch
for
fine
control
,
a
total
of 36
.
Position
(8)
and (6) on the front panel.
WARNING
: I
f the
welding
voltage
is
set
too high
,
the
weld
can burn through
l
ight
gauge sheet
metal. I
n
t
h
is
case,
the voltage
should
be
reduced.
If
set
too
low,
the
weld
w
ill
have little pe
n
etration
and will just
"s
i
t
on
"
the plate
FIGURE 3.
Wire Feed Speed
Th
e
wir
e f
e
e
d
s
p
ee
d
is
r
e
gul
a
t
e
d fr
o
m 0
-
18mm
/
m
i
n by the
potentiometer dial (4) above
the
vo
lt
age switch.
It
is most
important
to
se
l
e
ct
th
e
wir
e
f
ee
d
s
p
ee
d
in r
e
l
a
tion
to
the
vol
ta
ge
se
ttin
g.
Th
e c
orr
ec
t
w
i
re
f
e
ed speed/vo
lt
age
setting
is
recognisable by
:
-
1.
A continuou
s
r
eg
ul
a
r 'cr
a
ckling
' so
und
w
h
e
n
welding
,
the character
i
stics
of dip
trans
f
er o
f s
hort-
arc welding m
e
thod
norm
a
lly us
e
d
by
sm
a
ll
m
e
d
i
um
s
i
z
e
d
MIG
/
MAG
we
ld
e
r
s
.
2. A correct shape weld bead not too high, or low, with
correct fusion along the edge of the weld without
undercut in the heat-affected zone.
Welding Mode Switch/Timer
Controls
't1'
and
't2'
are fitted to all models
.
Both 't1' and 't2'
controls are used
to
control the
welder
ON/OFF times
during stitch
welding
and 't1' is used
alone to
control
spot
welding
time
(ON)
For normal
continuous (trigger controlled) welding,
ensure both 't1' and 't2'
controls
are turned
fully
anticlockwise to the OFF
positions
.
Protection Device
Protection against the
effects of
overheating
is
provided
by
thermal protection devices
mounted on the
transformer
assembly
and rectifier.
In the event of overheating, power to the unit
is
interrupted
.
The
protection
device automatically resets
once the unit cools
.
SHIELDING GAS
The
gas
provides a
shield
over the
weld
pool to
prevent
contamination from the
surrounding
air
.
The shield gas
also contributes
to
arc stability, weld
strength,
and
appearance,
so
care should be
taken to
ensure
that the
correct gas
type/mixture
is selected for
the metal being
welded
.
(Refer
Table
page
9).
The gas
flow
rate,
adjusted
by the regulator
,
increases
with variations in welding
gun
nozzle
diameter
,
and should
be
15
litres per minute
for the
MB24 welding gun to
25
litres
per minute
for the
MB36
welding gun with cylindrical
nozzle.
Excessive gas flow rates
should
be
avoided as they are
wasteful
,
and in some instances, can cause weld porosity
.
WORK ENVIRONMENT
The
machine
should
be used indoors away from
strong
draughts which
may
cause gas
dissipation
.
If the
machine is
to
be covered
,
the
natural
cooling
air
circulation must
not
be interrupted
.
Before
commencing
welding
,
clear area of
flammable materials
.
OPERATION
Continuous Welding
Ensu
r
e that
both timer switches
't1'
and
't2'
are
in the
'OFF'
position
.
Set
the
voltage and wire
feed
controls to
positions suitable for welding
the
thickness of the material
being welded.
Welding
current varies in direct relat
i
on
s
hip
to wire feed
speed
.
For low
welding curr
e
nt
output
,
th
e
wir
e
f
e
ed
sp
e
ed control should
be
set at
the low
end
of the wire
feed
speed scale
.
Turning
the wire
feed speed control knob clockwise
,
will
result
in
increased wire feed speed and welding current.
Welding voltage is adjusted
to
match
the
wire
feed
speed
(w
e
lding
current)
.
For
w
e
lding in the low
current range
,
set
the
voltage switch to position
number (1)
(number 1 on both
voltage switches for MIGOMAG 260+300+350+400)
.
These MIGOMAG
machine
s
hav
e
two voltag
e
s
e
l
e
ction
switches
,
a coar
s
e
c
ontrol (8)
a
nd fin
e
volt
a
g
e s
election (6).
Progressively select higher voltage positions with increases
in wire speed.
Low
wire
feed speed settings for a given voltage will
cause
a large ball to form on the end of the
welding
wire and
cause excessive spatter.
High wire
feed
speed
settings for
a
given
voltage will
cause
w
i
re stubbing
.
Position the torch
over the seam to be
welded with
the nozzle approximately
70° to the
work
surface.
The nozzle
to work
distance should
be approximately 10mm
.
WARN BYSTANDERS TO SH
I
ELD THEIR EYES.