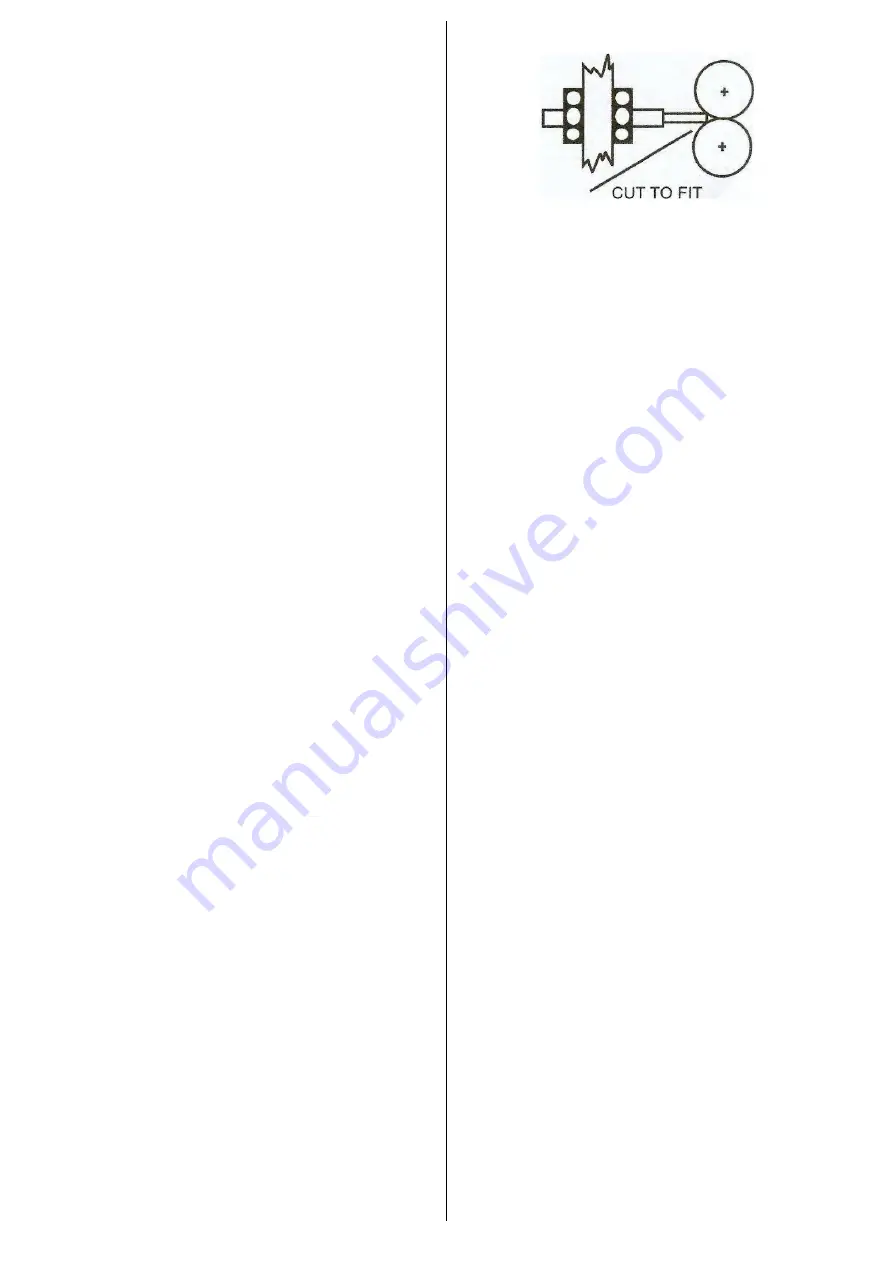
5
Lower
your
helmet and press the
welding gun
trigger
switch
to
init
i
ate an
arc
.
As
the weld is deposited
,
push
the
torch
from
a right to left direction, slowly along
the
seam at
a constant speed. Using
the wire
feed speed
control,
adjust for
a 'crisp'
sounding arc
.
Spot Welding
MIG spot
welding is
made
from
one side of the sheets
placed one
upon
another so
that the high
welding
current
penetrates through
the upper
sheet(max
.
1
.
5mm) and
also a part of the lower
sheet.
A
circular
spot is
produced
each
time the torch trigger
is
pressed
.
The
spot weld
time
't1' can be varied
.
Select 'spot' welding by
turning
switch
't 1"
only
.
Fit
a spot-welding
nozzle
to
the torch
.
See GUN
PARTS LIST.
Set
voltage and wire
feed speed
controls
to near
max
.
settings and carry out test welds on scrap materials as
follows:
Position the legs
of
spot-welding
nozzle over
weld
position and
depress torch
trigger switch
.
At the
termination of the
weld,
check for
weld
penetration (small
dimple
showing on
unders
ide of weld)
,
and
adjust
spot
weld
t
i
me
for best
results
.
When welding sheets of
unequal
thickness
,
the thinner sheet must be on top
.
Th
i
cker
sheets can be welded
together by drilling
a
hole in the top
sheet
and
directing the
wire
into hole-this is known
as
'plug
welding'
.
Spot welding
requires
ONLY LIGHT PRESSURE
;
the
sheets are
pressed
against
each other
with
the
legs o
f
the welding
no
z
zle
.
Switch Welding All Models
The wire feed output
is
switched
on
and off
repeatedly
.
This
produces a
lower
heat input which
is
part
i
cularly
advantageous
when
welding
thin or poor-quality
materials
as well as bridging gaps
.
Select
'stitch'
welding by
turning 't1'
and 't2' controls to the
halfway
setting
.
Vary time to
obtain
best results
.
They do
not have to
be equal
.
't1' control
s
the
welding or working cycle
.
't2' control
s
the
p
a
u
s
e cycle between w
e
lding
.
Note
: T
he t
r
igger on the gun must be kept dep
r
esse
d
during
both cycles.
Welding
occurs during
th
e
working (ON) cycle
.
During the
pause
cycle
,
the
wire feed STOPS, and the arc will
extinguish
.
During the pause cycl
e
the
molt
e
n pool will cool down
.
T
he
arc will ignite again automatically at
the beginning
o
f
the
following working cycle when the filler wire makes contact
with the
molten
pool.
The weld
i
ng
current i
s a
utomatically
s
wit
c
h
e
d on and off
and the shielding gas supply will rem
a
in on during the
pau
s
e cycl
e
.
Note: Spot welding and stitch welding of aluminium is
not possible.
SETTING UP GUN FOR ALUMINIUM WELDING
The Welding Gun
Remove the liner positioner nut from the adaptor block at the
wire feed end of the gun cable. Remove the gas nozzle,
contact tip holder, gas diffuser/ contact tip from the welding
torch and remove existing liner if fitted.
Carefully push the Teflon liner with brass neck liner attached,
through the gun cable until the end of the liner protrudes from
the swan neck.
Adjust the contact tip holder, gas diffuser/ contact tip and gently
push the liner to seat it into the back of the contact tip holder/
contact tip. Replace the gas nozzle.
At the adaptor block end of the gun cable, slide the brass nipple
and “O” ring over the liner until they are located om the recess
in the adaptor block and replace the liner retaining nut.
DO NOT CUT THE TEFLON LINER YET!!
FIGURE 4.
The
Welding
Machine
With a pair of long-nosed pliers, remove the steel inlet
guide tube from the central adaptor on the front face of the
welding machine
.
With the Teflon liner st
i
ll protruding from the adaptor
block
feed the
l
iner
through
the
i
nlet of the central adaptor until
the adaptor block is butted against the central
adaptor.
Fasten into position
with
adaptor block lock nut.
Cut the liner in the shape of a 'V', using a sharp knife so that
it butts up to the feed rollers as pictured. (FIG.4
.
) Remove
the welding gun from the machine and cut the brass
support tube so that it is 3mm shorter than the protruding
Teflon liner
.
Slide the brass support tube over the l
i
ner and enter the
Teflon liner
with
brass support tube fitted into the inlet in the
central adaptor. Feed through until the adaptor block is
butted against the central adaptor and tighten the lock nut.
Replace the
wire
hub tension by backing off the nut
in
the
centre of the hub until the nut is positioned at the end of
the
stud.
After confirming
the
wire feed roll is the correct size for the
aluminium wire being used
,
and that the
wire
is fed through
the gun cable
,
back off the
wire
feed roll pressure screw until
the feed roll no longer
feeds the wire
and re-tighten
approximately
2 turns
.
Too much pressure will deform the soft
aluminium
wire
and
cause
the wire
to
jamb
in
the contact tip
.
Note
:
To help prevent wire deformation
‘
U'
groove
feed roller is a better
al
t
ernative
than a
'V'
groove feed rolle
r
.
Contact Tip
Aluminium welding
requires
a contact tip with greater
clearance than that used for steel. Special clearance contact
tips are available for welding aluminium
and
are des
i
gned
with A suffix
.
e.
g.
0
.
9A, 1
.
2A.
PARTS LIST
Part No.
Description
1260005
Teflon Liner 1.0mm
1260021
Teflon Liner 1.2mm
1290461
Brass Support Tube for Teflon Liner
1310001
Nipple for Teflon Liner
86003033
Drive Roll 0.9/1.0-1.2mm AI (195 230 260
300)
86003066
Drive Roll 0.9/1.0-1.2mm AI (350 400)
1410004
Contact Tip 0.9mm Aluminium
1410006
Contact Tip 1.0mm Aluminium
1410010
Contact Tip 1.2mm Aluminium
86007001
Brass Neck Liner