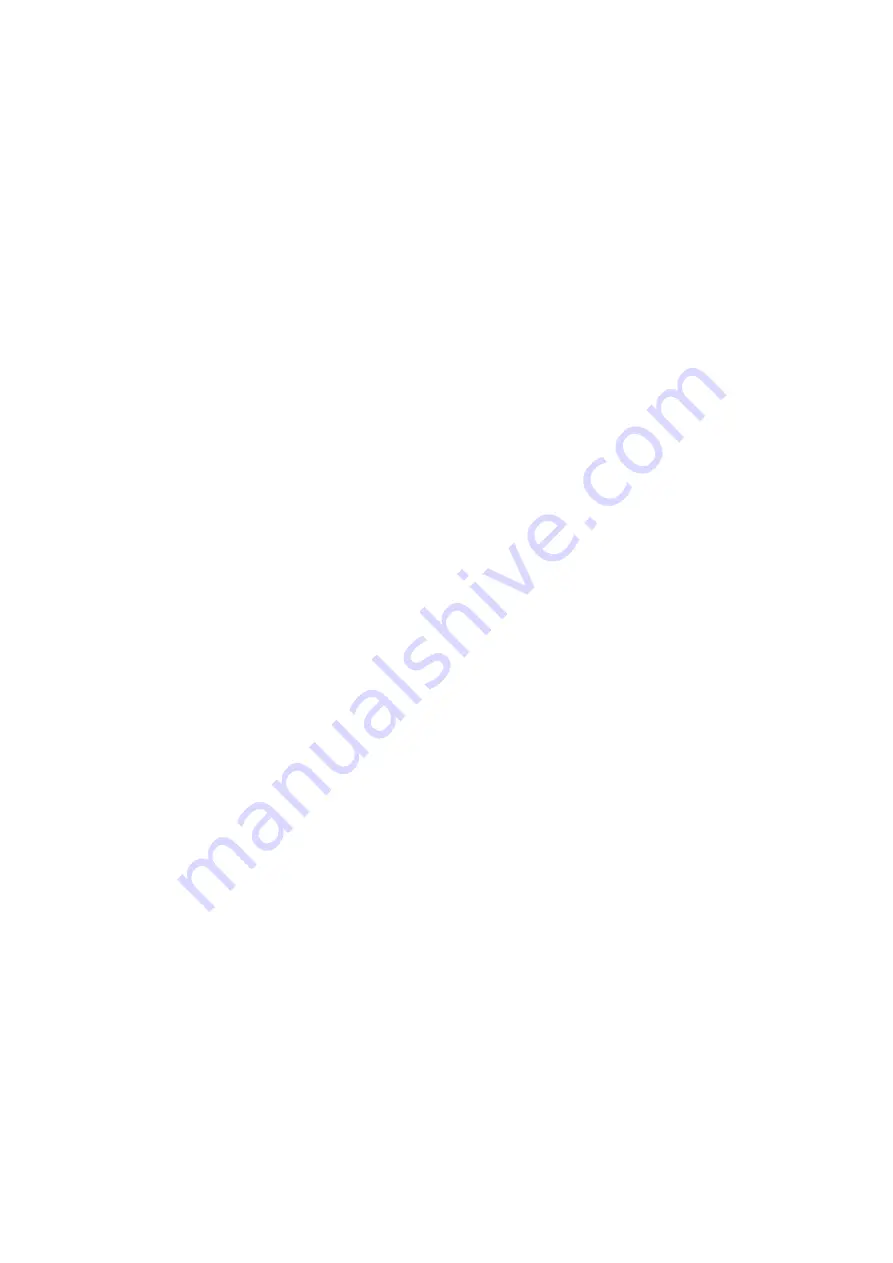
10
Maintenance of MIG welding hoses
- Switch off the welding machine before check-up or
repair of the welding hose.
- Check welding hose and cables for damage to the
insulation.
- Make sure that the cables are as stretched out as
possible during the welding operation. The welding
hose must not be bent sharply.
If the welding wire sticks to the contact tip, the contact tip
must be cleaned or exchanged. If the welding wire is
damaged between the wire drive rolls, the defective part of
the wire must be rejected as otherwise it may cause the
electrode to stick to the contact tip again.
Upon installation of a new wire reel, the liner must be
blown clean using compressed air or shielding gas to
remove any dust and wire residues.
-
Prior to welding, make sure that there is sufficient flow
of gas and cooling water.
-
Check the gas hose and cooling hose for leaks, fire
damage and sharp bends.
- Use Migatronic "red cooling liquid" of type 23%
propan-2-ol and 77% demineralized water. The cooling
liquid should be exchanged every year to preserve its
optimal properties.
If the welding hose is not used for more than 10 minutes,
the shielding gas in the hose must be renewed prior to
resuming welding, by pressing the trigger repeatedly.
Gas nozzle, insulator, gas diffuser and contact tip should
be dismounted at intervals for cleaning purposes and
check for wear and defects. Defective parts must be
exchanged immediately, in particular defective insulation
parts, as otherwise short circuits between swan neck and
workpiece may occur. If the hole in the contact tip is worn
or defective in any way, the contact tip must be
exchanged. Regular use of Migatronic MIG spray is
recommended in order to prevent weld spatter from
sticking to the gas nozzle.
Repair of welding hoses should only be carried out by
qualified staff.
Installation of a liner:
To ensure stable wire feeding, the liner must be firmly
fixed towards the contact tip/nozzle holder. To install the
liner, proceed as follows:
1. Stretch the welding hose out to its full length.
2. Remove gas nozzle and contact tip.
3. Remove the nut holding the liner and the old liner.
4. Put in a new liner and a new nut.
5. Shorten the liner to a length 2.5-3.0 mm shorter than
the runout in the torch handle after installation of the
inlet nozzle.
6. On all liners with phosphorus bronze neck liners, the
neck liner must be ground for correct centering with the
contact tip.
7. Remove all inside and outside burrs on the liner prior
to installing the contact tip/tip adaptor. Make sure there
are not burrs or squeezed turns in the internal diameter
of the liner; the specified internal diameter
measurements apply for the finished liner.
WARRANTY
Basically, welding hoses are regarded as wear parts.
Therefore, the warranty covers only manufacturing
defects and defects in the material found immediately
upon taking the product into operation.