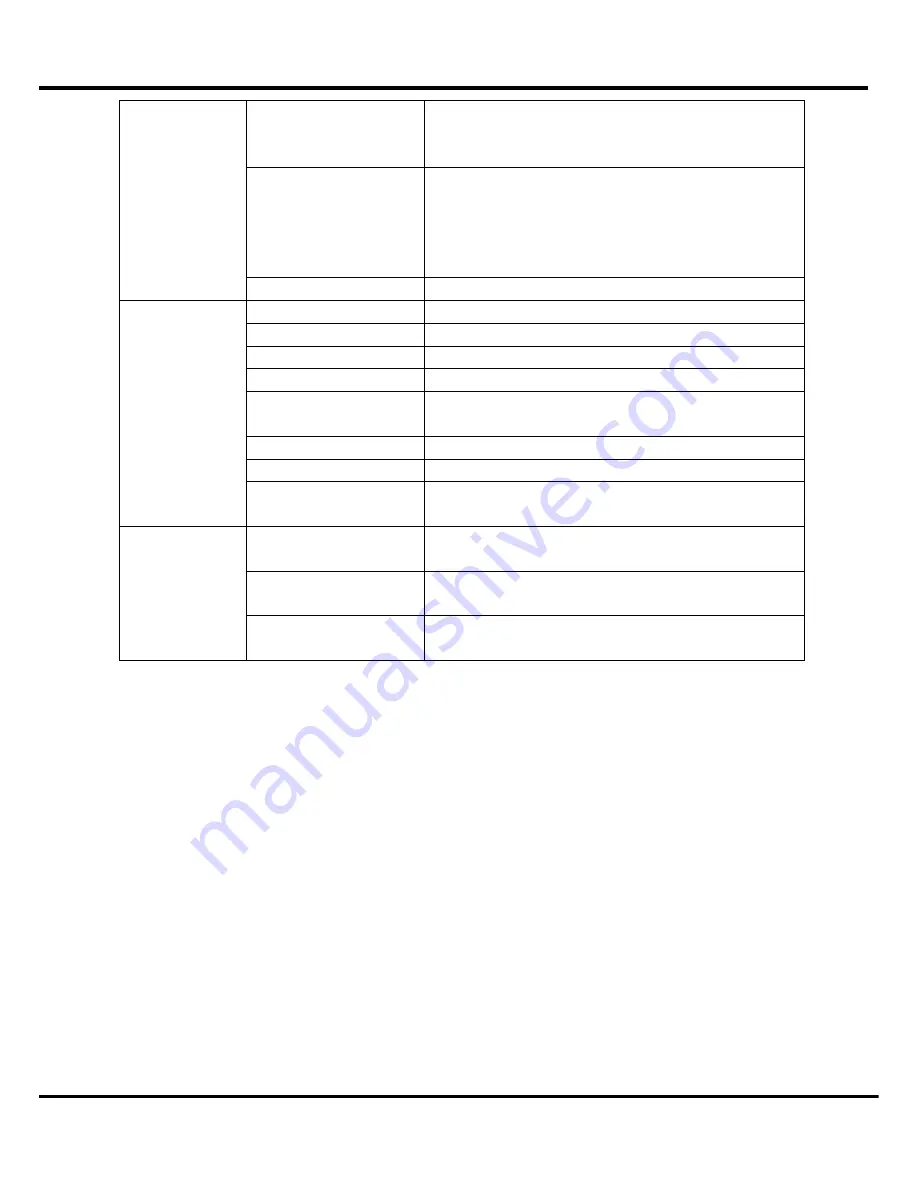
Trouble shooting
29
Capillary tube
Regulate the flow if capillary tube and make the
evaporating temperature appropriate if the evaporator is
frosted. Replace if blocked. Repair joint if leaking.
Compressor
The inlet and outlet valve of the compressor is damaged,
making the low pressure connected with the high pressure.
The refrigerating system can not produce high pressure
and low pressure. Replace the compressor after checking
for the reason.
Heat sources
Reduce if too many.
No cooling or
heating.
No power
Check the voltage. Call an electrician if no within the limit.
Wiring
Check the terminals. Repair and correct if loose.
Temperature setting
Check and adjust the temperature setting.
Mode setting
Check and adjust the mode setting.
Compressor
Check and replace if the compressor, the over-load
protector or wiring is broken.
Electric heater failure
Check and replace if the heater is damaged.
Over heat fuse failure
Check and replace if the fuse is damaged.
Main PCB
Check the voltage of main PCB. Replace the main PCB
when the unit failure in heating mode.
The unit starts
and stops
frequently.
Power supply
The input power supply voltage is too low. Call an
electrician if not within limits.
Main PCB
Check and replace the main PCB if the compressor relay
on PCB is shorted or damaged.
Room temperature
When the room temperature is too high, the compressor
will protect.
Summary of Contents for MPM1-10CEN1-BB6
Page 1: ...Portable air conditioner MPM1 10CEN1 BB6 MPM1 10EEN1 BB6 MPM1 10CRN1 BB6 MPM1 10ERN1 BB6...
Page 7: ...Outer dimension 5 3 Out dimension...
Page 8: ...External view part display 6 4 Display 4 1 LED display 4 2 LCD display...
Page 15: ...Installation detail 13 6 6 4 Cover the hole using the adaptor cap when not in use...
Page 32: ...Exploded view spare part 30 12 Exploded view spare part 12 1 Exploded view of unit...
Page 33: ...Exploded view spare part 31 12 2 Exploded view of accessory part...