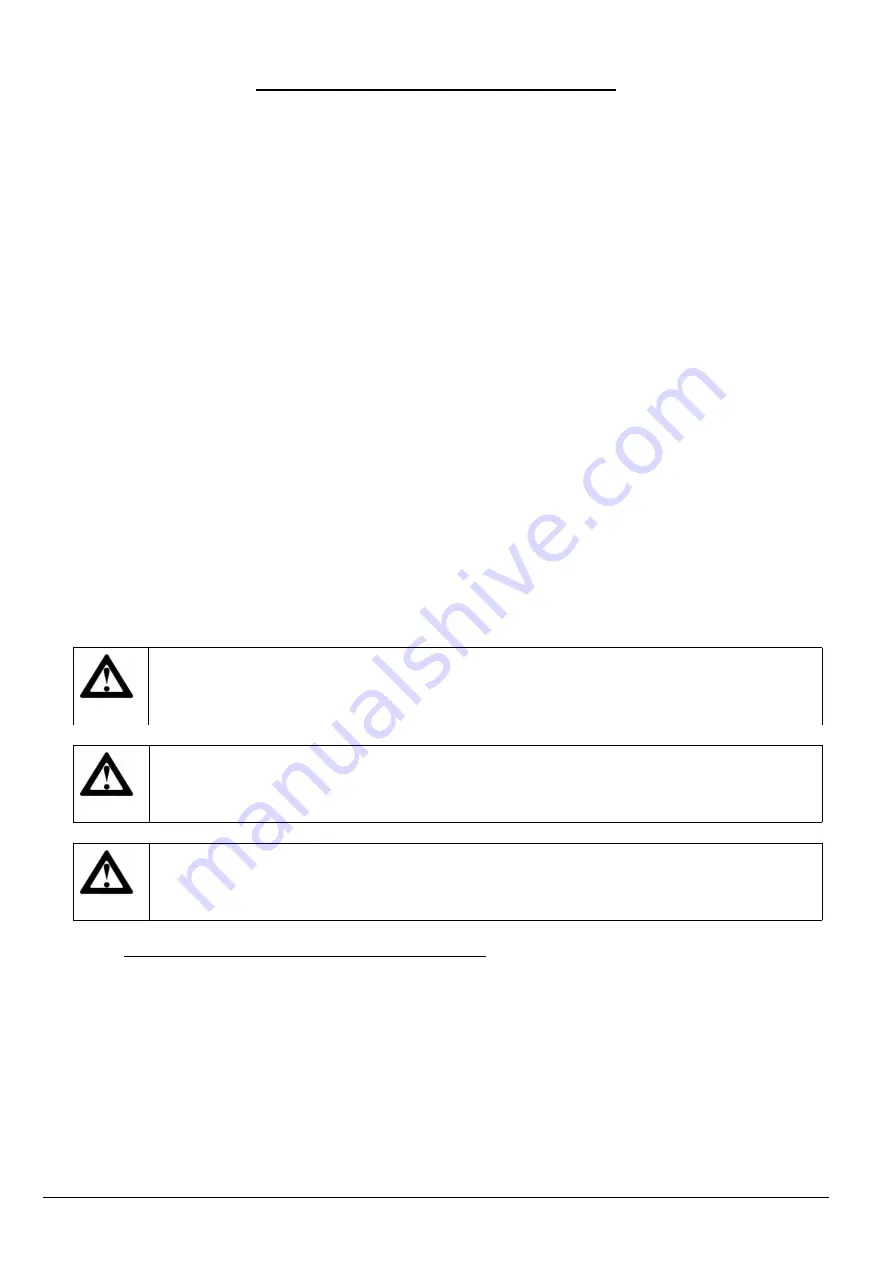
Programming by keyboard or by RS485
1. Sensor and input signal selection:
Variant 1
– RTD or TC selection with linearization in the device.
Linearization is up to 9
th
stage in 4 sub-ranges. In RTD it is necessary its connection to be selected
In TC it is necessary the automatic correction of the cold end to be enabled or disabled. The
dimension have to be set - º C or º F.
The sensor range is set by parameters.
Variant 2
– The input signal is linear current or voltage.
The transmitter range is set by parameters
Variant 3
– The sensor is non-standard nonlinear – it can be linearized by request or by the user by
RS485, MODBUS RTU protocol, by entering polynomial up to degree three coefficients.
Variant 4
- At sensor/transmitters with unknown transmission characteristics it is possible to be set
linear by two points by physical change of the technological quantity and setting of two limit values
in the device.
2. Setting of decimal point and lower and upper limit of the range, set-points parameters, alarms,
bargraph etc.
3. Selection of analogue output and range setting – if it is available / ordered /.
4. System setting of analogue inputs – if it is necessary.
5. System setting of analogue outputs – if it is necessary.
6. Setting of communication parameters – if RS485 is available.
*
It is possible to begin with this procedure
To restore the factory settings – page 20
After changing the decimal point all the parameters related with PV – process variable,
influencing on the range, bargraph, set-points etc. have to be changed
For controller programming Microsyst offers:
•
USB / RS485 Convertor
•
Base software for setting for operating systems Windows
MOST COMMONLY USED ABBREVIATIONS:
RTD - resistance temperature detector
TC
- thermocouple
ATC - automatic temperature correction
PV
- process variable
SP
- set point – set point for regulating of the measured process variable
OFFSET- offsetting the indication of input or output value
Aout - analog output
Document revision 2015-03-20
2