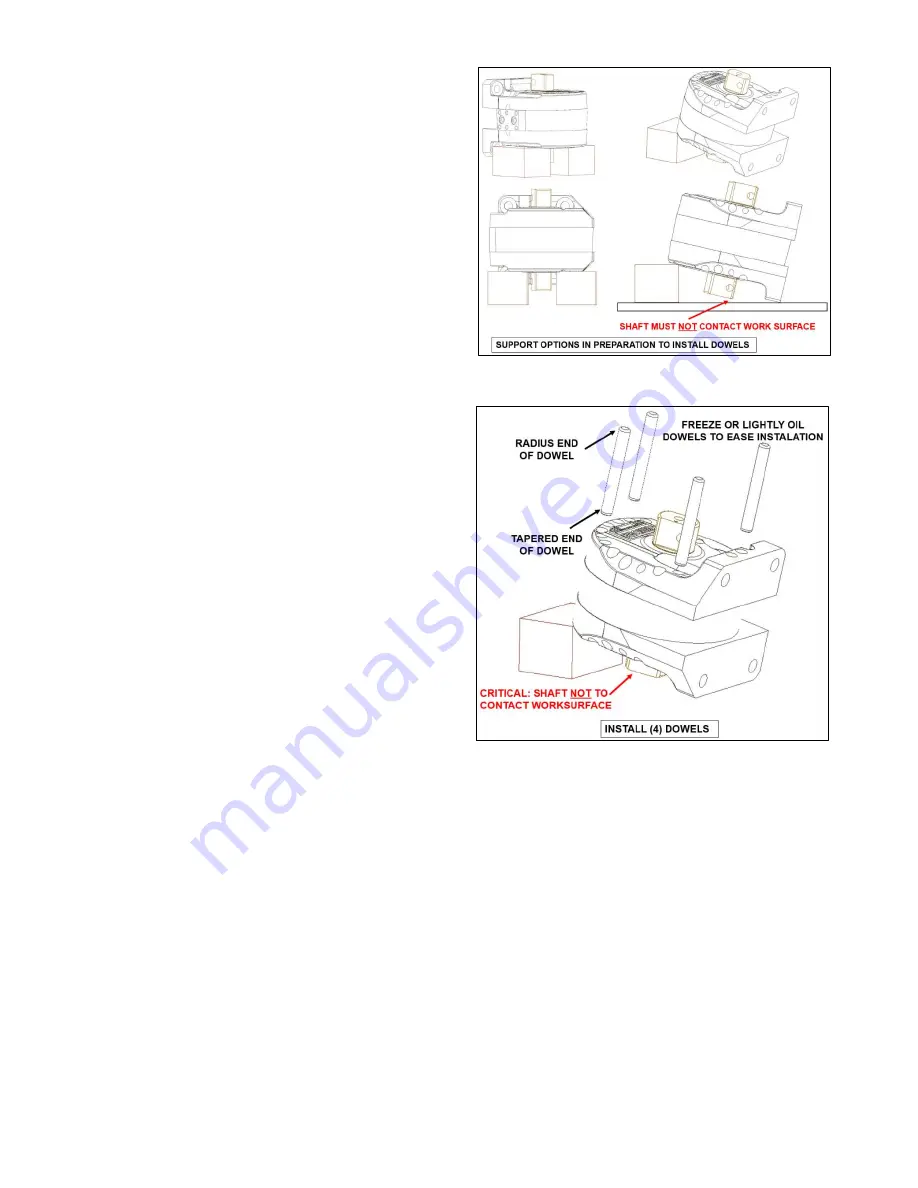
RM – 26-10-7707 Rev.
E
Page
27
of
39
(1) In preparation to install dowel pins
the assembly will require significant
support to counteract the forces
required to drive in the dowel pins
that have an intentionally tight fit.
(2) Refer to image for suggested
options to support assembly using
one or two of the support blocks
fabricated previously.
(3) It is
CRITICAL
that the shaft NOT
be in contact with the worksurface or
have support / contact in any way.
Doing so will damage the internals
of the actuator while driving in
dowels.
(4)
CAUTION
: The actuator assembly is heavy.
vii) Install four (4) long dowels:
(1) Head dowels are to be a slight
press fit.
DO NOT
ream or enlarge
dowel holes in actuator to make
dowel installation easier. Doing so
will void warranty and result in poor
actuator performance and likely
failure.
(2) It is recommended that the dowel
pins be frozen to -67°C to ease
installation.
(a) Alternatively, the dowel holes
can be lubricated with oil.
(3) Place one dowel into dowel hole
with the slight chamfered end being
put into hole and the large radiused
/ curved end outward. The Radiused end of the dowel is the end that is to be
hammered / pounded on.
viii) Install head bolts:
(1) Apply medium strength thread lock to remaining head bolts.
(2) Install the remaining head bolts into each side of the actuator.
(3) Using calibrated torque wrench - top torque ALL head bolts on BOTH sides of the
actuator to torque specified in the Torques chart located in
SECTION 7.
ix) Install four (4) Head Plugs NOTE: Older actuators will not have these plugs
(1) Two (2) plugs per side into the head. Tighten until snug,
DO NOT
overtighten.
(2) Using a calibrated torque wrench, top torque EVERY head bolt on EACH side of the
actuator to the torque specified in Torques chart located in
SECTION 7
.