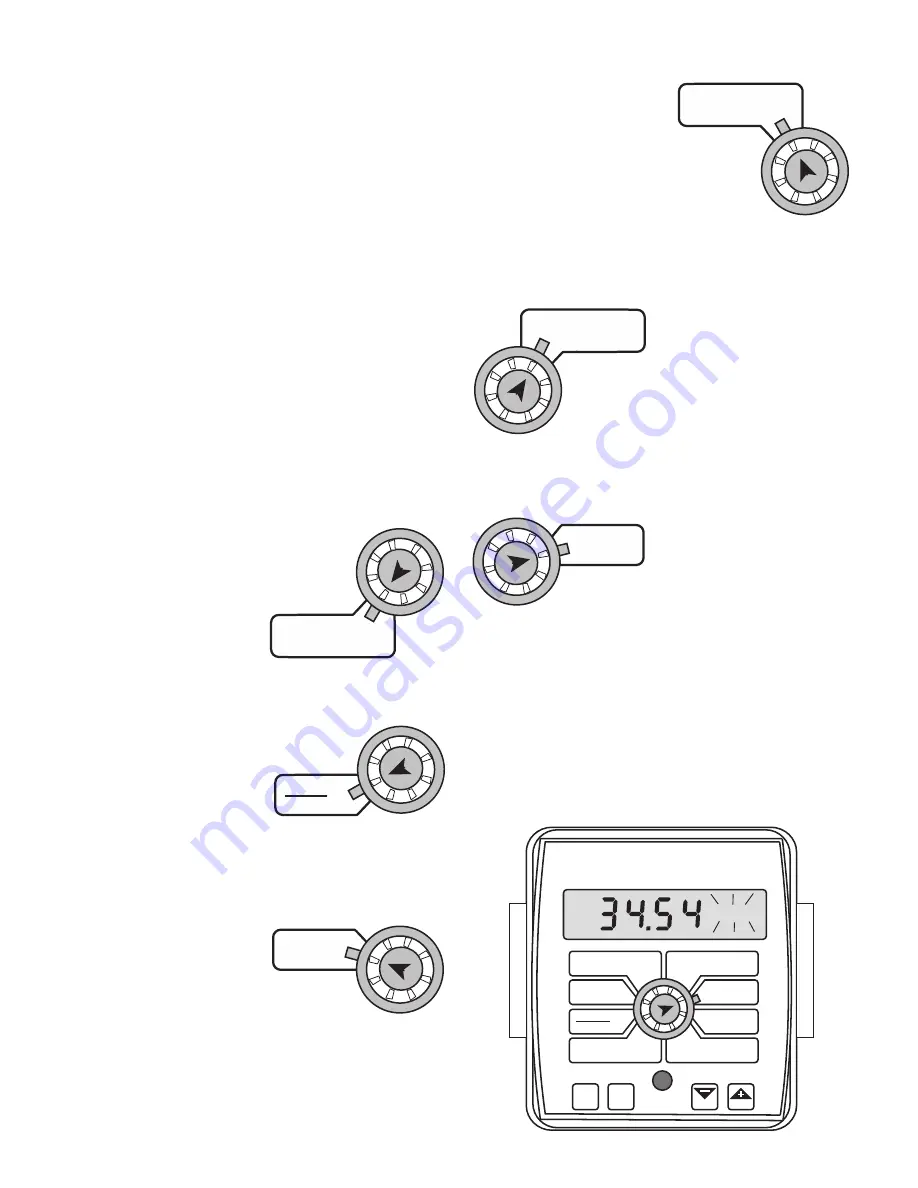
To enter or change any of the system’s calibration values,
you must enter calibration mode. To enter calibration mode,
STOP the vehicle, turn all booms OFF and press and hold
the CAL button until “CAL” lights up
(approximately three
seconds).
NOTE: Calibration may be entered while moving, but it is
not rec om mend ed to attempt calibration while the vehicle
is mov ing.
The console will remain in calibration mode, with the RED
warning light illuminated until you exit calibration or turn
power OFF.
Once in calibration mode, you may change any one, all, or
none of the values, in any order.
*
To select a calibration
position, simply turn the rotary selector to the desired
po si tion. Calibration positions are identified by the WHITE
labelling on each side of the rotary selector. All values are
entered and adjusted using the “+” and “-” but tons on the
front panel.
*
Test speed must be last.
TARGET RATE:
Enter the value for the desired
target application rate in gallons per acre
(liters per hectare). This is the ap pli ca tion
rate that the control console will lock onto
when operating in AUTO.
28
ADJUST RATE:
Enter the value for the desired amount of
change in gallons per acre (liters per hectare) to be used
for making on-the-go rate adjustments when
operating in AUTO. For example, if a value
“1.0” is entered, you will be able to increase
or decrease your
application rate in one-
gallon (liter) increments
during operation in
AUTO. To disable this feature, simply enter “.0” for a val ue.
TEST SPEED:
Enter the value to be used for simulating speed
for per form ing Pre-Field System Checkout. The console
will use this speed for simulating spraying operations. The
test speed value is
only used while in
calibration mode. Once
CAL is exited, the Test
Speed value is reset to zero.
DO NOT ENTER
A TEST SPEED UNTIL ALL OTHER VALUES
ARE PROPERLY ADJUSTED.
Please refer to Pre-Field System
Checkout for details.
BOOM SEL:
This po si tion is used to se lect the boom
sec tion to be cal i brat-
ed. With the ro ta ry
switch in this po si tion,
the dis play will show
the ac tive boom section num ber. Use the
“+” or “-” buttons to select the boom section
to be calibrated. Once the de sired boom
section has been selected, turn the rotary
selector to width to enter the ef fec tive work-
ing width for that boom section. Repeat this procedure
for each boom section.
WIDTH:
Enter the ef fec tive working width, in inch es (meters)
for the boom sec tion
currently shown on
the dis
play. Repeat
this procedure for each
boom sec tion. Enter a value of “0” (.000) for
any unused boom sec tions.
CIRC:
This position is used to calibrate the speed sensor
for ac cu rate speed and dis tance measurement. When this
position is selected, the display will alternately show, every
three seconds, the wheel
circumference value and
the distance value. The
wheel circumference
value is the number shown along with “CAL”
on the display.
See Illustration 33.
The distance
value is the number shown when “CAL” is not shown on the
display. To select either one of the values for calibration,
simply press the “+” or “-” button when the val ue you want
to select is being displayed. Once selected, the display will
stop al ter nat ing between the two figures for one minute to
allow you to make the appropriate ad just ment. After one
minute fol low ing your last adjustment to the value, or after
you move the rotary selector away from the CIRC position and
back again, the display will alternate between the two values
again.
Calibration
(cont)
Entering Calibration Values
BOOM
SEL
TOTAL AREA
TARGET
RATE
APP. RATE
ADJUST
RATE
AREA
HOUR
TEST
SPEED
SPEED
Illustration 33
WIDTH
SUB AREA
CIRC
DISTANCE
WIDTH
CIRC
MIN
FLOW
FLOW
CAL
AREA
HOUR
APP. RATE
TOTAL AREA
SPEED
DISTANCE
FLOW
RATE
TOTAL FLOW
SUB AREA
BOOM
SEL
TEST
SPEED
ADJUST
RATE
TARGET
RATE
AUTO
MAN
CAL
RESET
MANAUTO
CALHOLD
MT-2400
™
LR