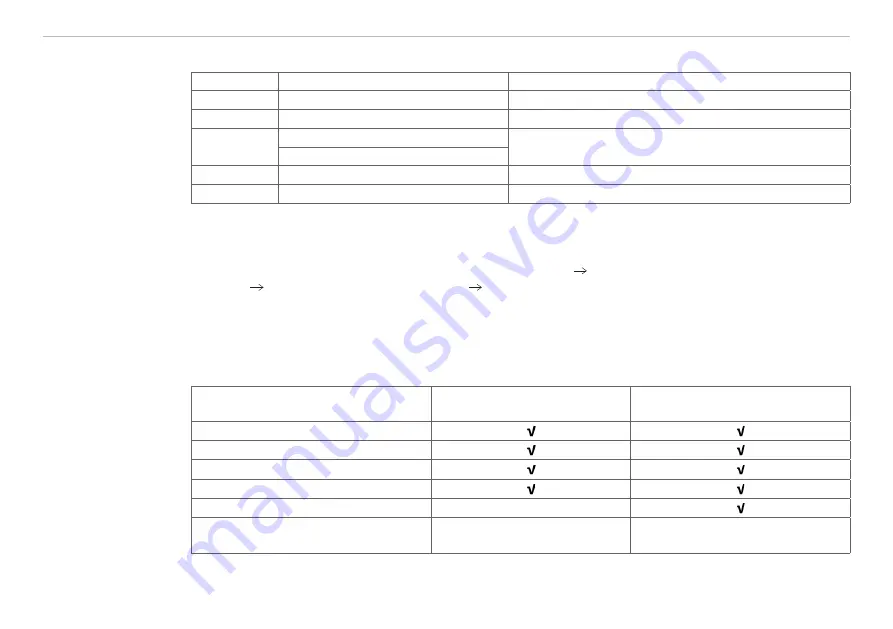
Page 75
Appendix | Industrial Process Interface (Optional)
thermoIMAGER TIM
The industrial process interface offers the following inputs and outputs:
Designation Description
max. range
1
/ status
A IN 1 / 2
Analog input 1 und 2
0 - 10 V
2
D IN 1
Digital input (active-low = 0 ... 0.6 V) 24 V
AO1 / 2 / 3
Analog output 1, 2 and 3
0/4 - 20 mA
Alarm output 1, 2 and 3
DO1 / 2 / 3
Relay output 1, 2 and 3
3
open/ closed (red LED on) / 0 ... 30 V, 400 mA
FS
Fail-safe relay
open/ closed (green LED on) / 0 ... 30 V, 400 mA
i
The alarm output can be configured as a threshold between 0 - 4 mA for no alarm and between
10 - 20 mA as alarm. For values outside the respective range, the relay does not switch on a DO.
1) Depending on supply voltage; for 0 - 20 mA on the AO the PIF has to be powered with min. 5 V < (1.5 +
working resistance * 0.021) < 24 V; Example: R
Load
= 500 ohm
U
min
= 1.5 + 500 * 0.021 = 12 V, R
Load
=
100 ohm
U
min
= 1.5 + 100 * 0.021 = 3.6 V
min. 5 V
2) The AI is designed for max. 24 V, the voltage level above 10 V is not interpreted.
3) Active if AO1, 2 or 3 is/ are programmed as alarm output.
The process interface has an integrated fail-safe mode. This allows to control conditions like interruption of
cables, shut-down of the software etc. and to give out these conditions as an alarm. The time constant of the
fail-safe is 1.5 seconds.
Controlled conditions on camera
and software
Standard process interface
TM-PIF-TIM
Industrial process interface
TM-PIFCxx-TIM
Interruption USB cable to camera
Interruption data cable camera - PIF
Interruption power supply - PIF
Shut-down of TIM Connect software
Crash of TIM Connect software
-
Fail-safe output
0 V at analog output (AO)
Open contact (Fail-safe relay)/
green LED off