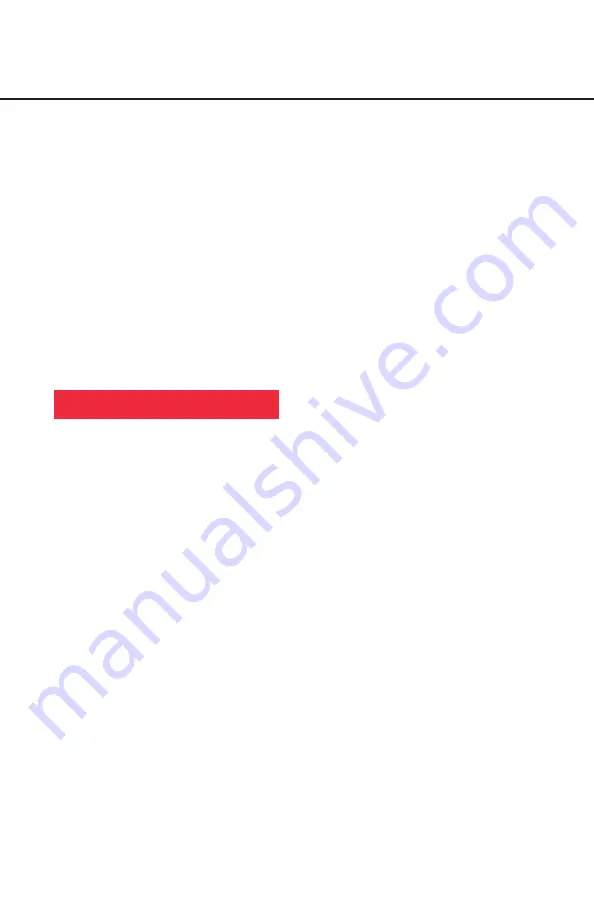
4
internal shut-off to prevent
hose whipping if a hose fails or
coupling disconnects.
• Whenever universal twist
couplings (claw couplings)
are used, lock pins should be
installed to prevent connection
failure. Whip hoses can cause
severe injury. Do not use
damaged, frayed or deteriorated
air hoses and fittings. Check
that all fittings are tight before
applying air pressure.
WARNING
Product Safety
Information – General
Hazards While Tool
In Use
• Always use Personal Protective
Equipment appropriate to the
tool used and material worked.
This may include dust masks
or other breathing apparatus,
safety glasses, ear plugs, gloves,
apron, safety shoes, hard hat
and other equipment.
• Air under pressure can cause
severe injury. Never direct air at
yourself or anyone else.
• Always turn off the air supply.
Bleed the air pressure and
disconnect the air supply
hose when not in use before
performing any maintenance on
this tool or any accessory.
• Keep clear of whipping air
hoses. Shut off the compressed
air before approaching a
whipping hose.
• Do not use power tools when
tired or under the influence of
medication, drugs or alcohol.
• Never use a damaged or
malfunctioning tool or accessory.
• Do not modify the tool,
safety devices or accessories.
Modifications can reduce the
effectiveness of safety measures;
increase the risks to the operator,
and void the warranty.
• Do not use this tool for
purposes other than
recommended.
• Exposed throttles shall not
be used where obstructions
can hold the throttle in the
“on” position.
• When a secondary handle
is supplied ensure it is properly
installed and use two hands to
maintain control when operating
the tool.
• Impact Wrenches are not
torque wrenches. Connections
Safety
Summary of Contents for 750SS Series
Page 27: ...27 Notes...