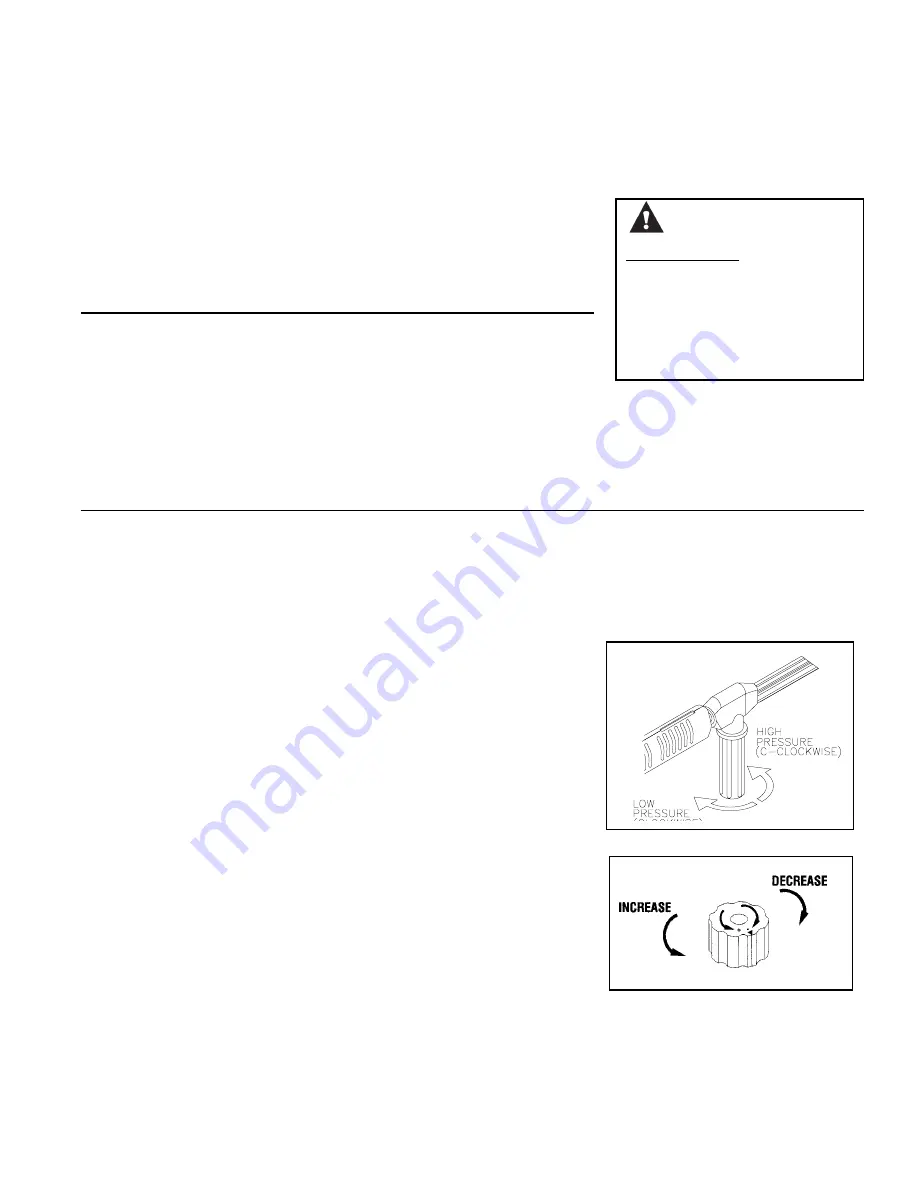
Mi-T-M
HSE-SERIES Operator's Manual
19
HOT WATER OPERATION:
1.
Follow the steps 1-8 outlined for "START-UP/COLD WATER OPERATION".
2.
Move the Switch to the "Burner" position. On initial start-up, water will begin
turning hot in approximately 20 seconds and will reach maximum temperature
in approximately 2-1/2 minutes, provided the trigger remains squeezed. The
burner will stop firing when the trigger is released.
NOTE:
While spraying, it is normal for the burner to fire intermittently. The high
limit switch will cause combustion to cease when the temperature of the
discharged water exceeds the temperature setting of the switch.
Combustion will begin again when the water temperature drops below
the minimum setting .
At this point, the unit is operating as a hot water pressure washer. Be extremely
cautious when adjusting the pressure and controlling the trigger gun/dual lance
assembly to avoid the possibility of burns.
STEAM OPERATION:
1.
Follow steps 1-8 outlined for "START-UP/COLD WATER OPERATION".
2.
Ensure the quick-connect at the end of the dual lance is cool enough to touch,
then remove the high pressure nozzle and replace it with the steam nozzle.
3.
Turn unloader knob completely counterclockwise to the minimum setting.
4.
Turn the Burner/Steam switch to "Steam".
NOTE:
The burner will shut down if the switch is moved to "Steam" without first
setting the unloader to minimum or operating in the high pressure mode.)
At this point, the unit will operate as a steam pressure washer. Be extremely
cautious when adjusting the pressure and controlling the trigger gun/dual lance
assembly to avoid the possibility of burns.
CLEANING WITH DETERGENTS:
NOTE:
This feature is designed for use with mild detergents only. Since the
cleaning solution travels through various parts of the pressure washer,
do not use corrosives as they will cause extensive damage as well as
pose a considerable safety hazard.
1.
Refer to "Risk of Bodily Injury / Detergents" pg. 7. Be certain to wear
protective safety attire as stated on pg. 12.
2.
Prepare detergent solution according to label directions. (Never pump acids,
alkalines, abrasive fluids or solvents through the unit. Due to the unknown
and often corrosive characteristics of many detergents commonly used in
the pressure washer cleaning industry, it is recommended to use only
Mi-T-M detergents with this unit.)
3.
Fully immerse the
strainer end of the clear vinyl detergent hose into the
detergent solution.
4.
DIRECT FEED: Be certain the adjustable grip on the dual lance is turned
completely
clockwise
for low pressure detergent operation.
NOTE:
This injection system is designed to apply detergents under low pressure
only. It will not allow detergent solutions to be introduced into the system
unless the dual lance is set in the low pressure mode.
FLOAT TANK: Adjust the amount of detergent desired. Turn the metering
valve completely counterclockwise to set at maximum siphon rate.
5.
To apply solution; unlock the trigger gun and squeeze the trigger. In a few
moments a detergent/water mixture will exit the nozzle. Start spraying the
lower portion of the surface being cleaned and move up, using long
overlapping strokes. Applying from the bottom up helps avoid streaking.
Allow to soak briefly. Avoid working on hot surfaces or in direct sunlight to
minimize the chances of the detergent drying, which may result in damaging
surfaces. Be certain to apply cleaning solution to a small section at a time.
6.
To rinse; lock the trigger gun in the "OFF" position,
DIRECT FEED: Rotate the adjustable grip on the dual lance
counterclockwise
for high pressure.
FLOAT TANK: Turn the detergent metering valve to the "OFF" position.
Unlock the trigger gun and spray. It will take about 30 seconds to purge
all detergent from the line. For best rinsing results, start at the top and
work down.
7.
Siphon a gallon of water through the detergent injection system after each
use. This prevents the possibility of corrosion or detergent residue causing
mechanical problems during the next use.
OPERATING INSTRUCTIONS
WARNING
RISK OF BURN!
THE WATER TEMPERATURE
COULD BECOME VERY HOT
DURING HOT WATER/STEAM
OPERATION. BE CAUTIOUS
WHEN ADJUSTING PRESSURE
OR CONTROLLING THE
TRIGGER GUN/DUAL LANCE
ASSEMBLY.
OMGEN215
DETERGENT METERING VALVE
DETMTRVL.TIF.D1
ADJUSTABLE GRIP