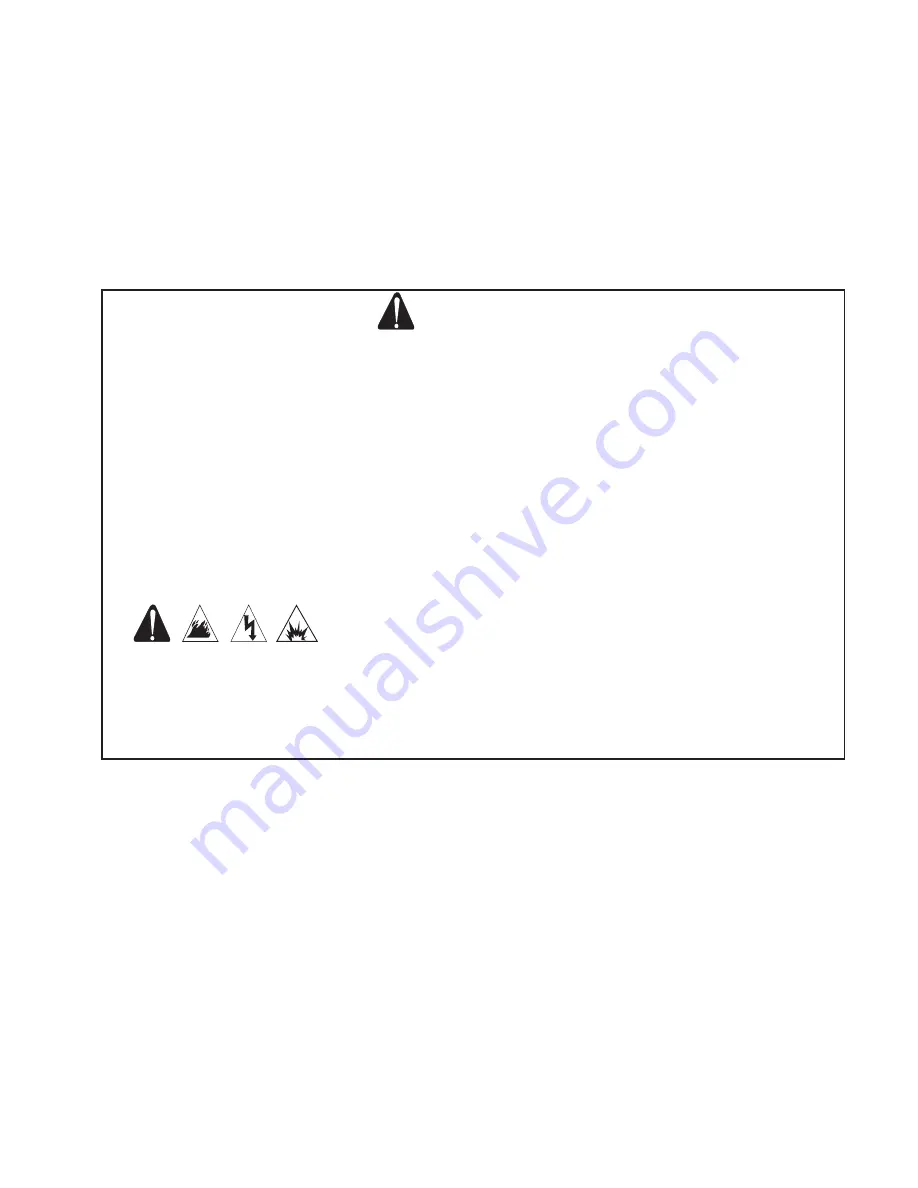
Stationary Electric Air Compressor Manual
3
IMPORTANT!
A "DANGER, WARNING or CAUTION" safety warning will be surrounded by a "SAFETY ALERT BOX". This
box is used to designate and emphasize Safety Warnings that must be followed when operating this air
compressor. Accompanying the safety warnings are "Signal Words" which designate the degree or level of
hazard seriousness. The "Signal Words" used in this manual are as follows:
DANGER: INDICATES AN IMMINENTLY HAZARDOUS SITUATION WHICH, IF NOT AVOIDED, WILL
RESULT IN DEATH OR SERIOUS INJURY.
WARNING: INDICATES A POTENTIALLY HAZARDOUS SITUATION WHICH, IF NOT AVOIDED,
COULD RESULT IN DEATH OR SERIOUS INJURY.
CAUTION: INDICATES A POTENTIALLY HAZARDOUS SITUATION WHICH, IF NOT AVOIDED MAY
RESULT IN MINOR OR MODERATE INJURY OR DAMAGE TO THE AIR COMPRESSOR.
The symbols set below are "Safety Alert Symbols". These symbols are used to call attention to items or
procedures that could be dangerous to you or other persons using this equipment.
ALWAYS PROVIDE A COPY OF THIS MANUAL TO ANYONE USING THIS EQUIPMENT. READ ALL
INSTRUCTIONS IN THIS MANUAL AND ANY INSTRUCTIONS SUPPLIED BY MANUFACTURERS
OF SUPPORTING EQUIPMENT BEFORE OPERATING THIS AIR COMPRESSOR AND ESPECIALLY
POINT OUT THE "SAFETY WARNINGS" TO PREVENT THE POSSIBILITY OF PERSONAL INJURY
TO THE OPERATOR.
INTRODUCTION
Congratulations on the purchase of your new Mi-T-M® Air Compressor! You can be assured your Mi-T-M®
Air Compressor was constructed with the highest level of precision and accuracy. Each component has
been rigorously tested by technicians to ensure the quality, endurance and performance of this air compres-
sor.
This operator's manual was compiled for your benefit. By reading and following the simple safety, installa
-
tion and operation, maintenance and troubleshooting steps described in this manual, you will receive years
of troublefree operation from your new Air Compressor. The contents of this manual are based on the latest
product information available at the time of publication. The Manufacturer reserves the right to make chang-
es in price, color, materials equipment, specifications or models at any time without notice.
Once the unit has been uncrated, immediately write in the serial number of your unit in the space provided
below.
SERIAL NUMBER ________________________________
Inspect for signs of obvious or concealed freight damage. If damage does exist, file a claim with the trans
-
portation company immediately. Be sure that all damaged parts are replaced an that the mechanical and
electrical problems are corrected prior to operation of the unit. If you require service, contact Mi-T-M
®
Cus-
tomer Service.
Mi-T-M
®
Corporation, 8650 Enterprise Drive, Peosta, IA 52068
563-556-7484 / 800-553-9053 / Fax 563-556-1235
Monday - Friday 8:00 a.m. - 5:00 p.m. CST
Please have the following information available for all service calls:
1. Model Number
2. Serial Number
3. Date and Place of Purchase