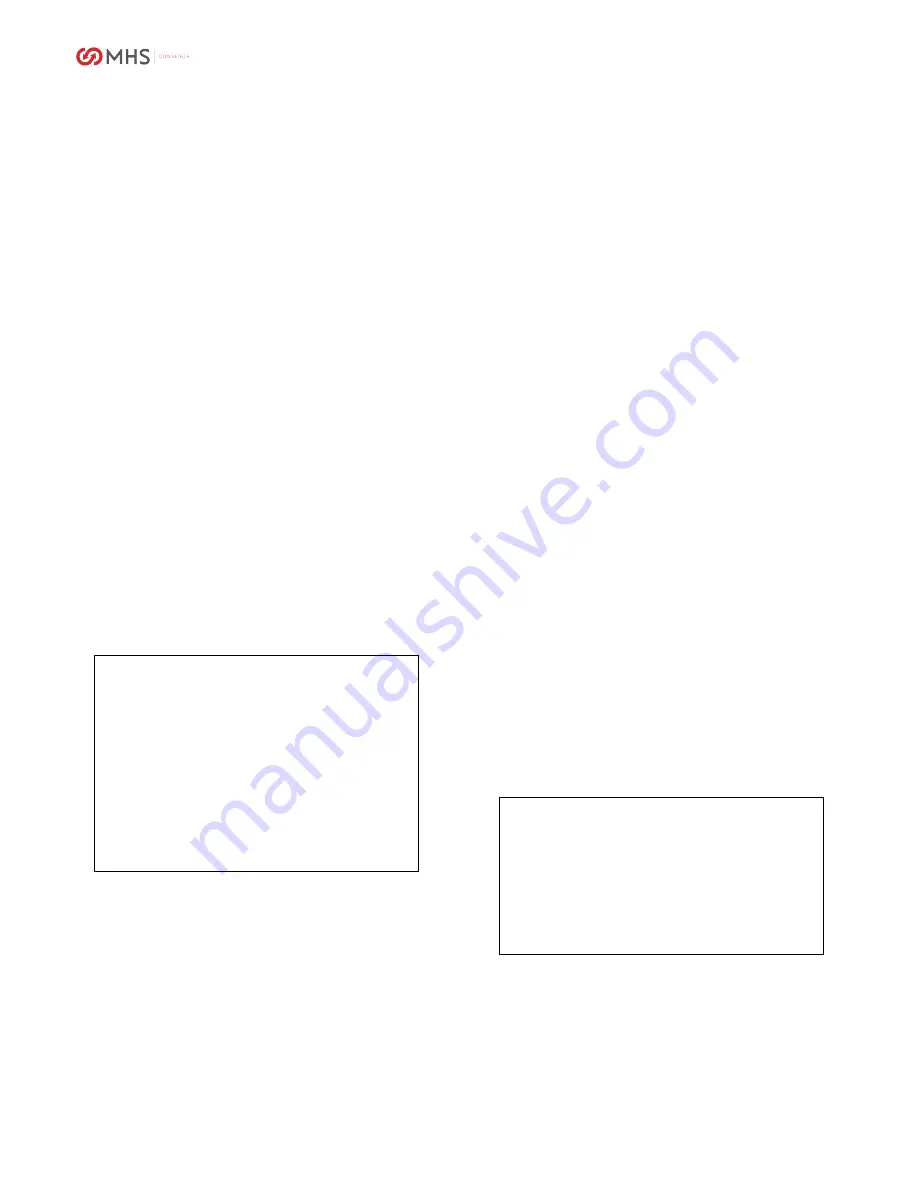
XenoROL®
50
MAINTENANCE SCHEDULE
Periodic maintenance intervals shown may vary with
load, speed, hours of daily operation, ambient
temperature, humidity, etc. Intervals can be
established by fairly frequent maintenance at first,
then lengthen the intervals as justified by
observation of need based on history. The following
is based on 5 days per week, 8 hours per day under
normal conditions.
DAILY
•
Listen to everything for unusual noises or
vibration.
•
Visually inspect to see that conveyor sections
are clear and free of debris.
•
Check to see that all safety guards are in place.
•
Check any oil leakage.
•
Check any unusual noises or vibration.
•
Check for loose bolts or parts.
•
Check air filter bowls for accumulated water.
•
Listen for air leaks.
WEEKLY
•
Inspect bearings, gear reducers and motors for
excessive noise or heat.
•
Clean breather cap on gear motor (if used).
•
Check operation of all electrical controls.
•
Inspect motor mounting bolts.
•
Check for proper PSI on air regulators.
MONTHLY
•
Check air filters for cleanliness.
•
Check coupler chains for cracks.
•
Clean chains and sprockets and lubricate with
SAE 30 weight oil or equivalent. (Check chain
tension and tightness of all adjusting screws.)
•
Check drive unit for leaking seals and oil level in
gearcase (if applicable), unusual noises,
vibration and stress cracks.
•
Check drive belts for wear, cracks or breaks.
•
Lubricate U-joints.
SEMI-YEARLY
•
If dry sounding, lubricate unsealed bearings in
rollers with light oil. Check free spin of rollers.
•
Drain and flush gearcase after each 2,500 hours
of normal operation or at least every 6 months (if
applicable).
•
Grease motor shaft bearings.
•
Inspect and clean motor control centers.
•
Grease regreasable bearings.
•
Inspect timing belts for pulley alignment and belt
wear.
YEARLY
•
Change oil in gearboxes.
•
Inspect tightness of all nuts and bolts on units.
Readjust and, if necessary, retighten.
•
Check for plumb and level. Shims have been
known to vibrate out from under supports in
isolated incidents.
Touch up paint that has been chipped.
Unpainted surfaces will rust.
•
Inspect for stress/fatigue cracks in frame and
supports.
WARNING
•
Prohibit riding on conveyor by anyone.
•
Think before making any adjustments. It
may prevent an injury. Remember, all
moving components are potentially
dangerous.
•
Protect yourself from unexpected starts
when working on a stopped unit by
locking and tagging the control panel or
disconnect switch that supplies power to
the unit.
CAUTION
•
Check to confirm tools and foreign
objects have not been left on or inside
the conveyor.
•
Check to confirm all loosened parts have
been retightened.
•
Check to confirm all guards have been
installed.
90480006rev092010
Summary of Contents for XenoROL XR40
Page 1: ...XenoROL 1 INSTALLATION OPERATION MAINTENANCE MANUAL XenoROL XR40 and XR48 90480006rev092010...
Page 9: ...XenoROL 9 90480006rev092010...
Page 56: ...XenoROL 56 90480006rev092010...
Page 59: ...XenoROL 59 Input shaft key missing or defective Replace key 90480006rev092010...
Page 70: ...XenoROL 70 PARTS IDENTIFICATION INTERMEDIATE BEDS CURVES 90480006rev092010...
Page 74: ...XenoROL 74 PARTS IDENTIFICATION WHEEL DIVERTER ASSEMBLY MERGE ASSEMBLY 90480006rev092010...
Page 75: ...XenoROL 75 PARTS IDENTIFICATION GATE XENOSWITCH ASSEMBLY 90480006rev092010...