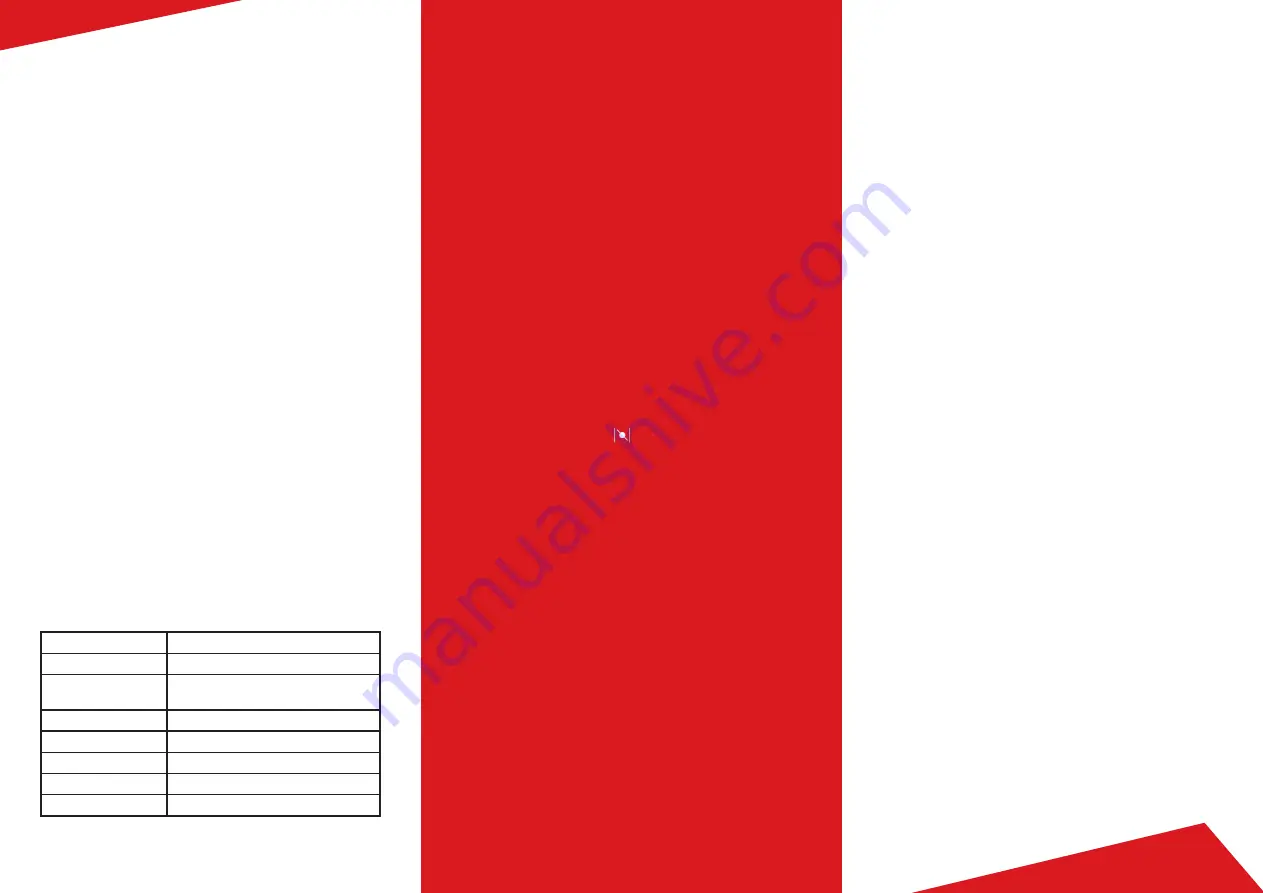
E) Attaching air tools
•
WARNING:
Before connecting air tools, make sure that you
read the instructions supplied with the tool. Ensure that
the air tool is suitable for use with this compressor and
hose specifications
•
Attach the air hose to the air outlet using an appropriate
connector
•
Attach the air tool to the other end of the air hose - if using
snap couplings, use a whip end available from your Clarke
dealer
•
Restart the engine and allow pressure to build up in the
receiver - the gauge will show the available pressure in the
receiver
•
Check the system for air leaks - if any are apparent, stop
the engine and operate the air tool until the air pressure is
at zero before rectifying leaks
•
Note: a self-relieving regulator is fitted which will vent
excess air pressure from the bleed hole when the pressure
reaches the max. operating pressure
•
Turn the pressure regulator (clockwise to increase
pressure) and proceed to use your air tool in accordance
with its own product instructions
F) Checking the safety valve
•
WARNING:
Do not remove or try to adjust the safety valve
•
Check the safety valve to ensure that it works correctly
•
Pull on the ring attached - air will be released when you
pull on the ring and stop when released
•
Do not use the compressor if the safety valve does not
operate in this way - the compressor must be repaired by a
qualified service agent
G) Subsequent starting
•
Connect the air hose to the air outlet and tool and set
the pressure regulator to zero pressure (turned fully
anticlockwise)
•
Start the engine and allow pressure to be built up
•
When the pressure in the receiver has built up and air
is expelled at the vent hole, turn the outlet pressure
regulator clockwise so that the desired pressure is shown
on the pressure gauge
•
Check for air leaks at the air tool and connectors before
proceeding
1. IMPORTANT NOTES
•
For the use of MGF Supplied equipment only.
•
Ensure potential users are fully trained in the operation of
this equipment and a site specific safe system of works is in
place and adhered to.
•
It is essential site specific risk assessments are undertaken.
•
If in doubt concerning the integrity of any part of the
equipment DO NOT USE IT.
2. AIR COMPRESSOR
•
The MGF CFP10H is powered by a reliable 5HP 4 stroke
Honda petrol engine, and is ideal for powering staple guns,
riveters and spray guns. It also features a tough steel frame
making it perfect for use on construction sites, plant hire
and mobile repairers.
•
This unit can deliver 7 bars of pressure with an integrated
air pressure relief valve/ gauge and is completed with a
robust build making it always ready for many tasks.
•
The air compressor pump has a highly durable cast iron
cylinder. The engine is Euro 5 compliant and has oil alert.
•
This portable machine is ideal for a multitude of uses
including fibre optic blowing.
3. MGF EXAMINATION AND TESTING
•
Upon return to MGF the equipment will be cleaned,
inspected and function tested by a competent and trained
MGF safety technician.
4. VISUAL INSPECTION/FUNCTIONAL
TEST - PRIOR TO USE
•
Before the start of each use ensure that the equipment is
clean and free from debris and there are no obvious defects.
Air Tank Volume
2.5 litres
Air Displacement
9 cfm
Max. Working
Pressure
101 psi
Engine
5 hp
Wheel Mounted
No
Start Method
Recoil
Fuel
Petrol
Engine Manufacturer Honda
mgf.co.uk
5. OPERATION INSTRUCTIONS
A) Positioning the Air Compressor in the workplace
• Always carry the compressor using the handle
• Do not lift by (or put strain on) valves or hoses
• Before starting, ensure the compressor is standing on a
firm level surface which does not exceed 10° incline, either
transversely or longitudinally
• Ensure the environment is dry and dust free
• Ensure there is adequate ventilation for:
• Air intake to the compressor pump and engine
• Cooling for the compressor pump and engine
• Engine exhaust gases
B) Adding fuel
• Remove the filler cap and fill the tank with unleaded fuel
(max. capacity 1.8l)
• Use a funnel to avoid accidental spillage of fuel
• If fuel is spilled it must be cleaned from the unit and
surrounding area before attempting to start the engine
• Do not overfill
C) Starting the engine for the first time
• Note: for the first time operation, do not connect the air
hose or any tools and proceed as follows
• Turn fuel valve to the on position
• Set the choke lever to the (starting) position
• Set the engine switch to the ‘I’ (on) postition
• Hold the starting handle firmly and pull lightly until you start
to feel resistance, then pull sharply to start the engine
• Note: you may have to do this more than once
•
WARNING:
Once the engine has started, allow the starting
handle to recoil slowly to avoid injury/damage as it whips
back
• When the engine is running steadily, gradually return the
choke lever to the normal running position (to the right)
• When the engine is running steadily, turn off and attach an
air hose to the compressed air outlet and to the air driven
tool.
D) Oil alert system
• An oil alert system is fitted to prevent engine damage
caused by insufficient oil in the crankcase. Before the
oil can fall below a safe limit, the oil alert system will
automatically stop the engine although the throttle level
remains in a running position
• If the engine stops and will not re-start, check the engine oil
level before troubleshooting other areas