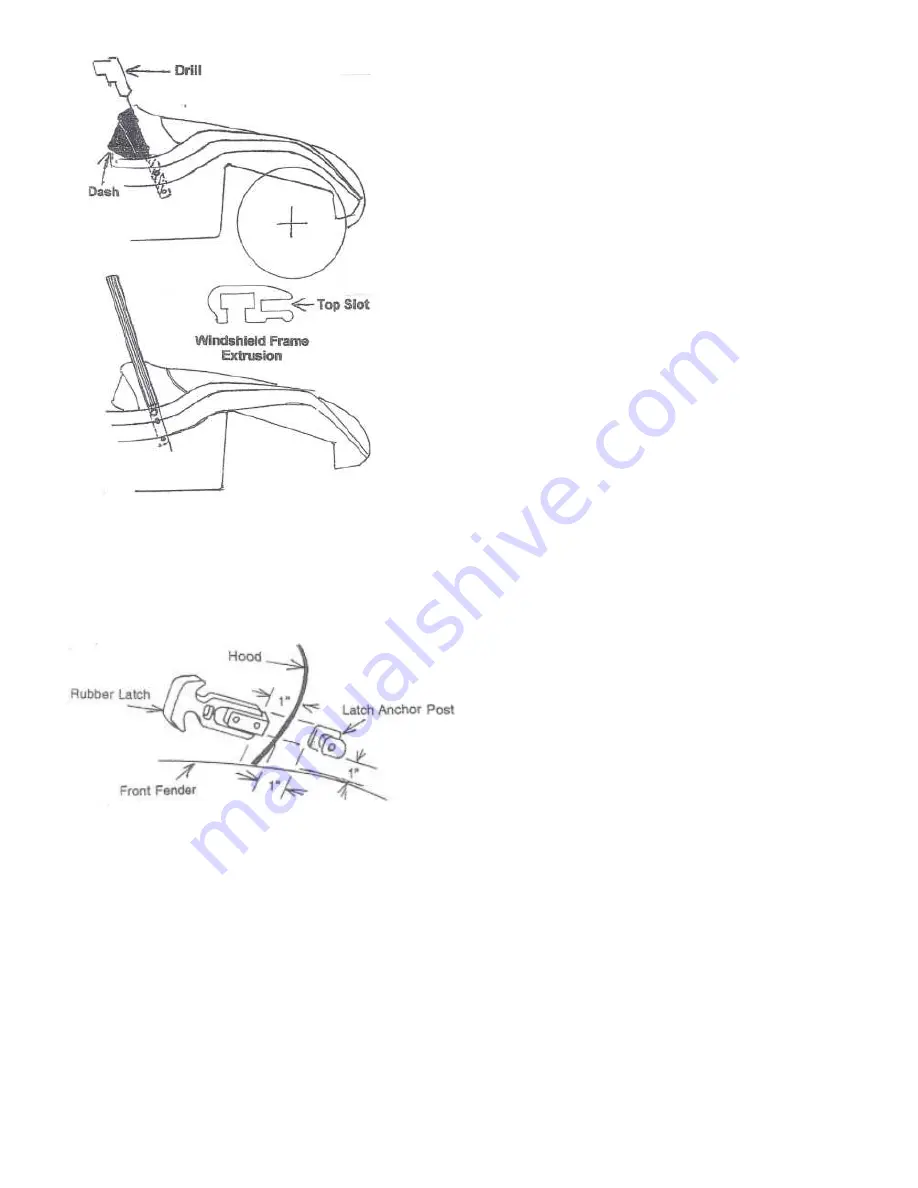
Step #12 – Dashboard Assy – Part #K-234
Lifting the cowl up slightly, the dash is fitted
under the top edge of the cowl. The ends of
the dash will reach around the ends of the
dash frame to butt the ends of the cowl at
the dash frames centerline. Using the 7 holes
in the cowl as a guide, drill down through the
dash which is just below. Using the seven
10/32” x 1” long bolts, nuts and washers,
secure the top of the dash and cowl to the
dash frame. The three ¼ /20” bolts are
temporarily removed at the bottom of the
dash frame to drill and reassemble the
bottom of the dash.
Step #13 – Windshield Assy – Part #K-255
With the small top slot facing forward on the
windshield frame, the two 6” long bars with
studs attached must be trial fitted. That is, slid
up into the open ends of the windshield
frame. Once satisfied as to their final
positioning, with drill, clean out any fiberglass
obstructions in the four holes at the cowl
ends. Carefully transfer from windshield, the
bars to the awaiting holes at the cowl ends.
Loosely attached, you and a helper should
lower the windshield down onto its new
home, sliding the bars up into the windshield
frame. The “H” rubber must be shipped into
place between the windshield and the body
before a rubber mallet might be used to help
bonk it down before tightening the four 5/16”
nyloc nuts.
Hood Latch Installation:
Step #14 –
Next, the rubber hood latches can be installed using
Hood Assy – Part #mxtr-1004.
This
is a two-part assembly using the six 10/32” x ¼” button head socket bolts. The smaller anchor post
part uses only one bolt with a locating pin on its underside. Place the anchor post on the cowl
approximately one inch from the rear edge of the closed hood and approximately one inch
above the upper rear corner of the front fender. Note, the anchor post’s small hooked upper
edge enabling the rubber catch from slipping off the anchor post. Note also, the nearly hidden
locating pin underneath to keep the post from revolving around while under pressure. Mark this
spot to drill a 3/16” dia. hole for the locating pin. Placing the anchor post with pin in this hole,
align for placement and drill the second hole for the 10/32” x ¼” button head socket mounting
bit. Repeat this process on the opposite side of the car. Next, after hooking the handle of the
catch over the anchor post, stretch it slightly with the hood solidly closed, and with proper
alignment insert the 3/16” dia. drill bit in one of the two holes and drill through, bolt it down and try
the rubber catch for alignment insert the 3/16” dia. drill bit in one of the two holes and drill
through, bolt it down and try the rubber catch for alignment. If there is a good result, drill the
second hole and finish bolting the rubber latch to the hood, both sides.