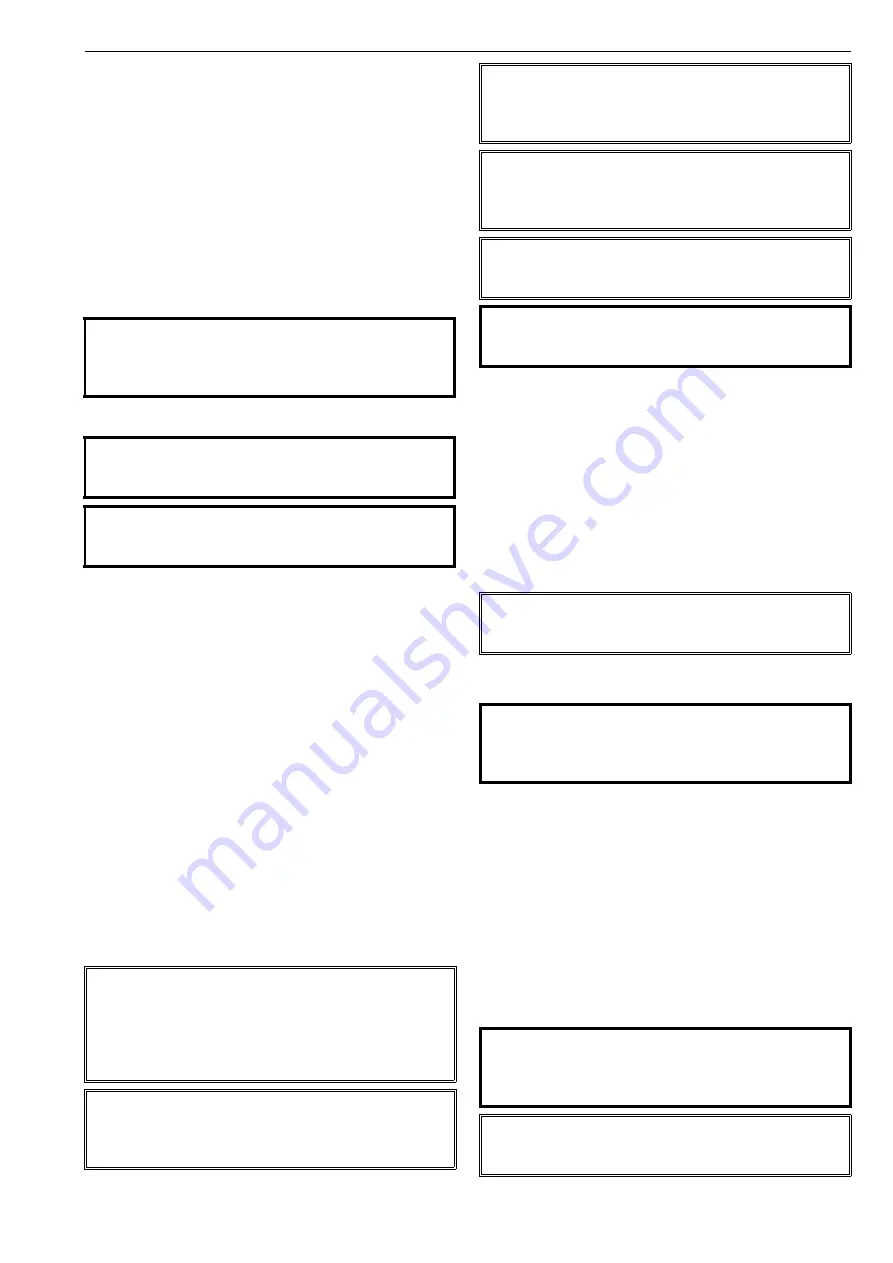
6 DA 70 en
7
3.3.2
Actuator removal for VDR,
Reverse <air to open, stem retract> actuator
See Fig. 5 and exploded view.
Lift up to the valve plug 100 % from the seat ring,
using by specified air pressure.
Loosen the plug stem locknut and the 4 socket head
screws (27) with hexagon nuts (28).
Remove the stem clamp (26).
Shut off and disconnect air supply line.
Support the actuator with the suitable lifting device.
Remove the yoke nut.
Remove the actuator from the valve body assembly.
4
MAINTENANCE
4.1
General
Although the Neles VD actuators require no regular mainte-
nance.
However, check the vent port and the diaphragm with case
and the guide bushing for leakage, proper preventative
maintenance can significantly help to prevent unplanned
downtime and in real terms reduce the total cost of owner-
ship. Metso recommends inspecting the valves at least every
five (5) years. The inspection and maintenance interval
depends on the actual
application and process condition. The inspection and main-
tenance intervals can be specified together with your local
Metso experts. During this periodic inspection the parts
detailed in the Spare Part Set should be replaced. Time in
storage should be included in the inspection interval.
Maintenance can be performed as presented below. For
maintenance assistance, please contact your local Metso
office. The part numbers in the text refer to the exploded
view and to the parts list in Section 8, unless otherwise
stated.
4.2
Replacement diaphragm for VDD,
Air to close
See Fig. 5 and Exploded view.
We recommend that all seals be replaced when the actua-
tor has been dismantled for servicing.
The actuator must be depressurized and the supply air
pipes disconnected.
Detach the actuator.
Check that the actuator has been depressurized, and
remove air tubing from the upper case (20).
Remove the short hexagon screws (23, 24, dia-
phragm case bolts) and the hexagon nuts (25).
Remove the the long hexagon screws (24, tension
bolts) and the hexagon nuts (25). in cross steps to
relies spring tension gradually.
Remove the upper case (20).
Loosen the stem nut (33) and remove the lock
washer (33a) and the stem rod plate (16) with O-ring
(17).
Remove the diaphragm (6) and the diaphragm plate
(13) with the stopper (15) from the top stem (18).
Remove the spring seats (11) and springs (12).
Replace the U-packing (4) and O-ring (5) in the stem
guide (2).
CAUTION:
Avoid to turn the valve plug and stem when plug is on
seat ring to prevent the seating line from being dama-
ged.
CAUTION:
Observe the safety precautions listed in Section 1.6
before starting work!
CAUTION:
When handling the actuator or the control valve
assembly, take its weight into account!
NOTE:
When sending goods to the manufacturer for repair, do
not disassemble them. Clean the valve carefully and flush
the valve internals. For safety reasons, inform the manu-
facturer of the type of medium used in the valve (include
material safety datasheets (MSDS)).
NOTE:
In order to ensure safe and effective operation, always use
original spare parts to make sure that the valve functions
as intended.
NOTE:
For safety reasons, replace pressure retaining bolting if the
threads are damaged, have been heated, stretched or cor-
roded.
NOTE:
If you send the actuator to the manufacturer for repair, do
not dismantle it. For safety reasons, please see the warn-
ing plate on the top side of actuator.
NOTE:
Always use original spare parts to make sure the valve
functions as intended.
CAUTION:
Do not dismantle the actuator or remove it from the
pipeline while the valve is pressurised!
NOTE:
If actuator is equipped with the handwheel, rotate
handwheel to a neutral position.
CAUTION:
Diaphragm case is under spring tension and is equip-
ped with the long hexagon screws (24, tension bolts)
which must be removal last.
CAUTION:
Checking whether scratched on the top stem (18) and
dirty particles inside of the stem guide (2) and the dia-
phragm and O-rings before reassembling.
NOTE:
Lubricate seal space and new O-ring with Unisilikon L250L
or equal silicone grease.