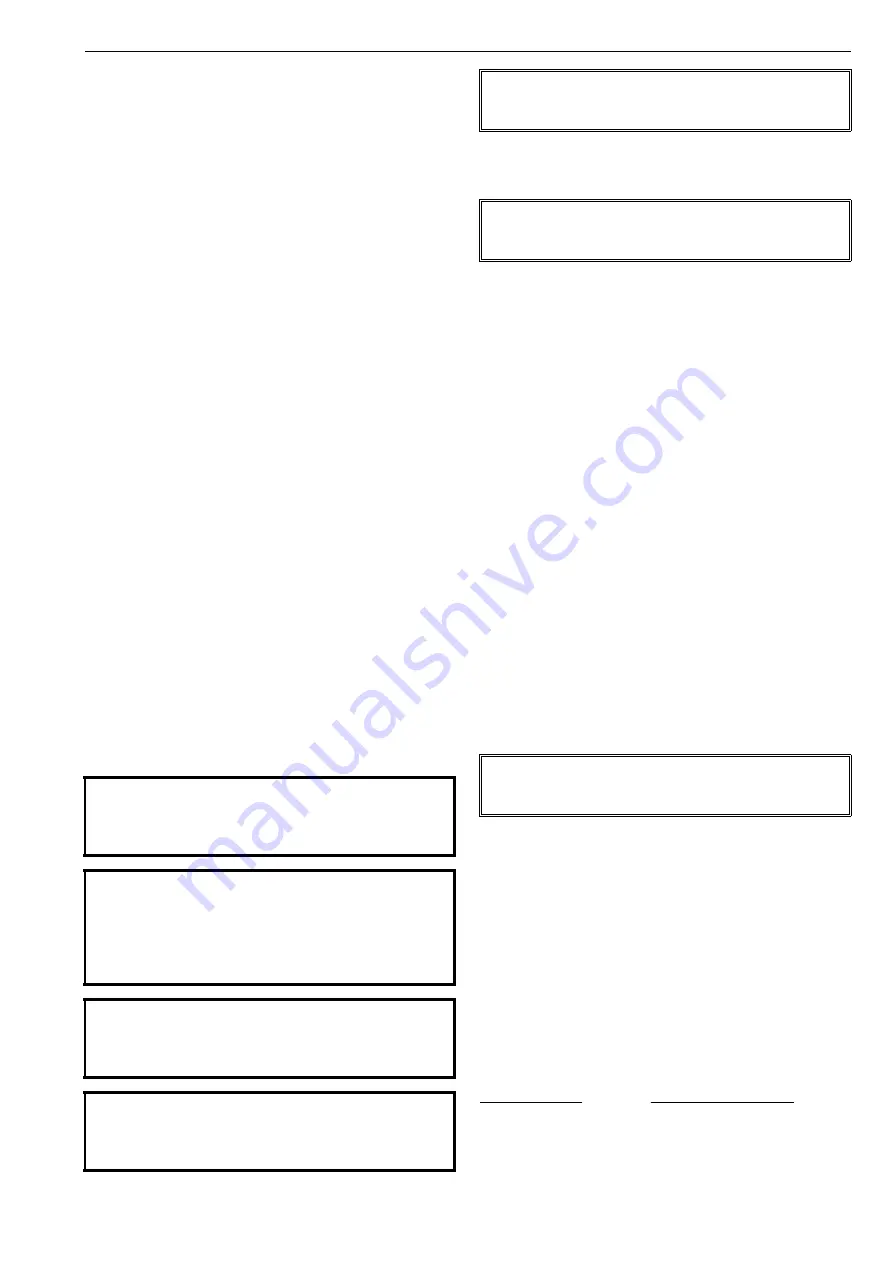
8 ACE 71 en
5
1.4.3
Control unit
Step motor controller type
GSP 92-70
Nominal power
200 W max. motor power
Un
230 V AC (option 110 V AC)
In
2 A, fuse T 2.5 A
(110 V: 4.2 A, fuse T 5 A)
Output power
max. 9 A, when 70 V input
to motor In 6.3 A
Steps
1/1 step
7050 pulses 0–90°
1/2 step
14100 pulses 0–90°
1/4 step
28200 pulses 0–90°
Factory settings
1/2 step, 14100 pulses / 0–90°
local control mode 200 Hz
time duration mode 150 Hz
Operational temp.
0°...50 °C
storage and transportation
-20°...+60 °C
Protection class
IP65
I/O
alarm contact, opening contact
24 V DC, max. 50 mA
manual operation,
closing contact 24 V DC,
max. 50 mA
Control signals
pulse, time duration and option
inputs: 24 V DC / 10 mA
optocoupled
1.5
Recycling and disposal
Most control system parts can be recycled if sorted according to
material. Most parts have material marking. A material list is sup-
plied with the system. In addition, separate recycling and dis-
posal instructions are available from the manufacturer. A control
system can also be returned to the manufacturer for recycling
and disposal against a fee.
1.6
Safety precautions
2
MOUNTING
2.1
Valve mounting
See Installation, Maintenance and Operating Instructions 3
R 71 for valve installation instructions.
2.2
Actuator mounting
Actuator is mounted to valve at the factory.
The actuator is mounted to the valve with either two or four
bolts. Actuator is connected to the valve shaft with a back-
lash-free joint.
2.3
Control unit mounting
2.3.1
General
Dimensions for control unit are: length 400 mm,
width 355 mm and height 150 mm.
The cable between the control unit and the actuator
may be up to 120 m.
The control unit may not be installed above a radiant.
Operating ambient temperature range of control
unit is 0° to 50 °C.
Heat sink (215) must have enough space to ensure
cooling.
Control unit must not be mounted on a vibrating base.
Mount control unit on an even base using the
attachment points of the control unit box.
2.3.2
Control unit connections
Control unit receives maximum of six cables, one or three
from the control system, two from the actuator and one
supply voltage cable. They are connected to the connector
card of controller according to Fig. 3. The cable shields
should be connected to the lead-ins to avoid any interfer-
ence. Leading the cable from the DCS through a ferrite is
recommended.
The internal connections of the control unit between the
step motor controller, display card and connector card are
made using cables with connectors. All cables must be con-
nected to ensure the proper operation of the controller.
Connector card, Fig. 4, connectors X1...X12, and step motor
controller, Fig. 5, connectors X1...X6, are connected as fol-
lows:
Connector card
Step motor controller
X7
—
X1
X9
—
X5
X10
—
X2
X11
—
X6
X12
—
display card
CAUTION:
Follow all marked cautions in Installation, mainte-
nance and operating instructions when handling the
valve.
CAUTION:
Do not exceed the permitted values!
Exceeding the permitted values marked on the control
unit may cause damage to the control unit and to the
equipment attached to it. Damage to the equipment and
personal injury may result.
CAUTION:
Finger covers (170) must be on during operation!
Finger covers may only be removed from the bracket dur-
ing maintenance and when power is switched off.
CAUTION:
The hand wheel (108) handle of actuator must be bent
during operation.
The handle can only be used when power is switched off.
NOTE:
Only authorized persons are permitted to carry out the
electrical connections for the device.
NOTE:
Install the valve with shaft in upright position.
Consult factory for other positions.
ELECTRICAL SAFETY NOTE:
The control unit does not have a main switch. The electrical
installation must provide a main switch or a circuit breaker.