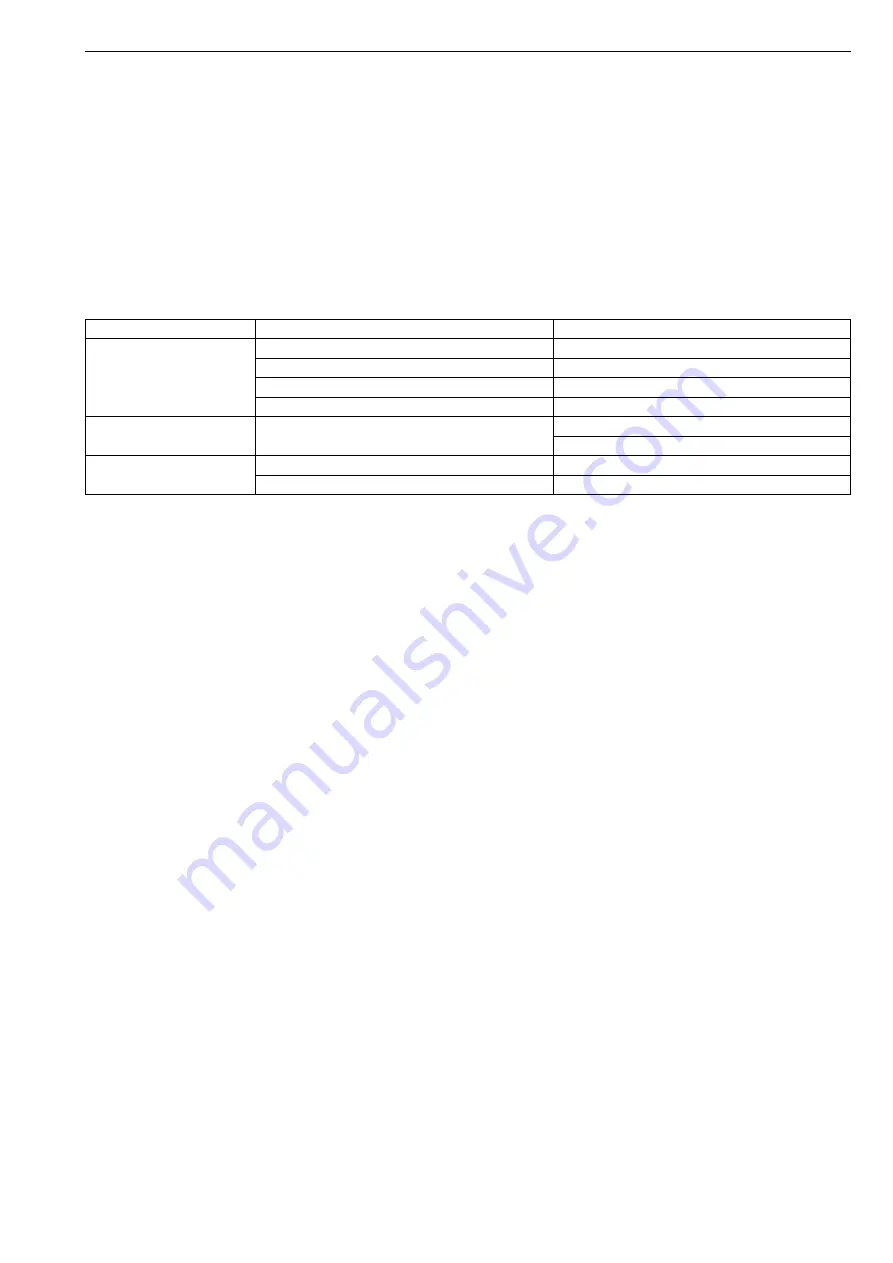
11
7
MALFUNCTIONS
The following Table 4 lists malfunctions that might occur
after prolonged use.
8
TOOLS
In addition to standard tools, the following special tools are
needed.
For removal of the actuator:
- extractor
This tool can be ordered from the manufacturer. Always give
the valve type designation when ordering.
9
ORDERING SPARE PARTS
When ordering spare parts, always include the following
information:
type code, sales order number, serial number
number of the parts list, part number, name of the
part and quantity required
This information can be found from the identification plate
or documents.
Table 3
Possible malfunctions
Symptom
Possible fault
Actions
Leakage through a closed
valve
Wrong stop screw adjustment of the actuator
Adjust the stop screw for closed position
Damaged ball surface
Turn the ball by 180°
Damaged seat(s)
Replace seat(s)
Ball cannot move freely
Clean the inside of the valve
Irregular valve movement
Impurities between the ball and seats
Flush the valve from the inside
Clean the sealing surfaces and seats mechanically
Leakage through gland
packing
Loose packing
Tighten the nuts
Worn-out or damaged packing
Replace the gland packing
Summary of Contents for NELES XH Series
Page 15: ...15 ...