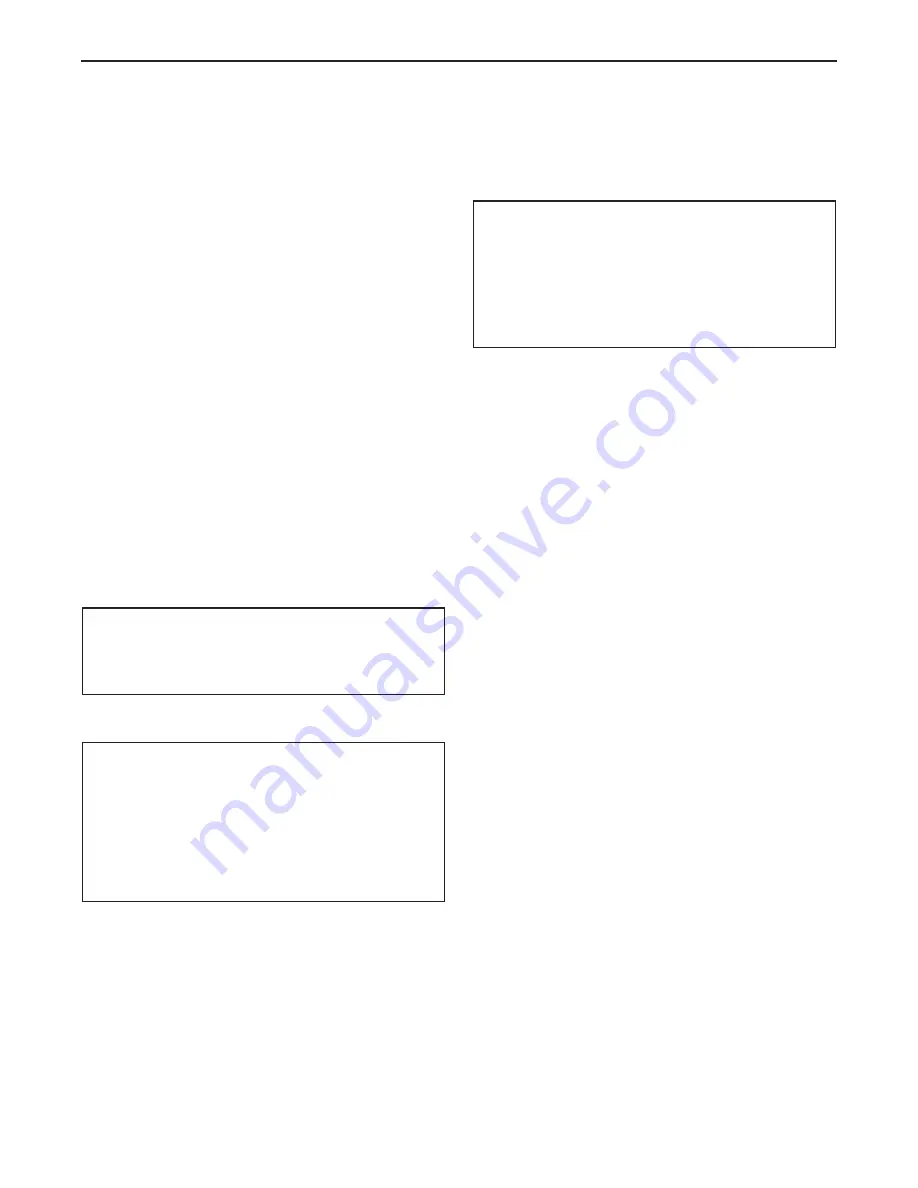
4 IMO-R27
2 TRANSPORTATION AND STORAGE
Check the valve and the accompanying devices for any
damage that may have occurred during transport.
Store the valve carefully. Storage indoors in a dry place is
recommended.
Do not remove the flow port protectors until installing the
valve.
Move the valve to its intended locations just before
installation.
The valve is usually delivered in the open position.
If the valve(s) will be stored for a long period, follow the
recommendations in IMO-S1 to maintain valve’s integrity.
3 INSTALLATION
3.1 General
Remove the flow port protectors and check that the valve
is clean inside. Clean valve if necessary.
Flush the tankcar carefully before installing the valve.
Foreign objects, such as sand or pieces of welding
electrodes, will damage the ball and seats.
3.2 Handles
If the valve handle (31) has to be removed for any reason,
the handle must be remounted properly. (See
Figure 8
)
3.3 Installing on Tank Car
The valve may be installed in any position and offers
tightness in both directions. It is recommended, however,
that the valve be installed with the insert (2) towards the
tank car.
Refer to
Section 4, MAINTENANCE
, for stem seal
adjustment. If there is weepage past the stem seals upon
installation, it means the valve may have been subject to
wide temperature variations in shipment. Leak-tight
performance will be restored by a simply stem seal
adjustment described in the
MAINTENANCE
section.
3.4
Commissioning
Ensure that there is no dirt or foreign objects left inside the
valve or tank car. Flush the tank car carefully. Make sure
that the valve is fully open when flushing.
Ensure that all nuts and fittings are properly fastened.
3.5 Steam Jacket Connections
(if applicable)
The steam-jacketed valve should be firmly attached to the
tank car prior to fitting and welding of steam jacket
connections. See
Section 3.3
.
The valve does not need to be disassembled prior to
fitting or welding of steam jacket connections; however,
the valve must be in either the fully open or fully closed
position.
Carefully fit the steam lines to the valves steam jacket
connections. There should be no side loads on the valves
steam jacket connections due to misalignment of the
steam line piping.
Welding connections should only be made by ASME,
Section IX qualified welders. Additional AAR welder
qualifications may apply.
An AAR certified welding inspector should inspect the
steam jacket connection prior to pressure testing.
Following approval of the welds, pneumatically test the
pressure tightness of the steam jacket connections to the
pressure rating of the steam system on the tank car, but do
not to exceed 250psig (17.2 barg.). Cover the welds with a
leak detection fluid and observe for three (3) minutes. Any
indication of leakage is cause for rejection.
4 MAINTENANCE
4.1 General
Although Metso’s
Jamesbury
valves are designed to work
under severe conditions, proper preventative
maintenance can significantly help to prevent unplanned
downtime and in real terms reduce the total cost of
ownership. Metso recommends inspecting valves at least
every five (5) years. The inspection and maintenance
frequency depends on the actual application and process
condition. Routine maintenance consists of tightening the
hex nuts (18) in (
Figure 8
) periodically to compensate for
stem seal wear.
Overhaul maintenance consists of replacing seats and
seals. A standard repair kit consisting of these parts may
be obtained through your authorized Metso Distributor.
WARNING:
FAILURE TO PROPERLY MOUNT THE HANDLE MAY RESULT IN
IMPROPER VALVE OPERATION, DAMAGE OR PERSONAL INJURY.
WARNING:
THE VALVE SHOULD BE TIGHTENED ON FLANGES USING
APPROPRIATE GASKETS AND FASTENERS COMPATIBLE WITH THE
APPLICATION, AND IN COMPLIANCE WITH APPLICABLE PIPING
CODES AND STANDARDS. CENTER THE FLANGE GASKETS
CAREFULLY WHEN FITTING THE VALVE BETWEEN FLANGES. DO NOT
ATTEMPT TO CORRECT MISALIGNMENT BY MEANS OF FLANGE
BOLTING.
WARNING:
GOOD PRACTICE DICTATES THAT ONCE INSTALLED, BUT PRIOR TO
FIRST USE, THE VALVE IS LEAK TESTED IN PLACE TO ASSURE LEAK-
TIGHTNESS HAS NOT BEEN COMPROMISED BY THE INSTALLATION
PROCESS. INSTALLATION ACTIONS THAT CAN CAUSE LEAKAGE
INCLUDE, BUT ARE NOT LIMITED TO; WRENCHING, SOLDERING,
WELDING AND/OR HOISTING. SEE
SECTION 4.5
.