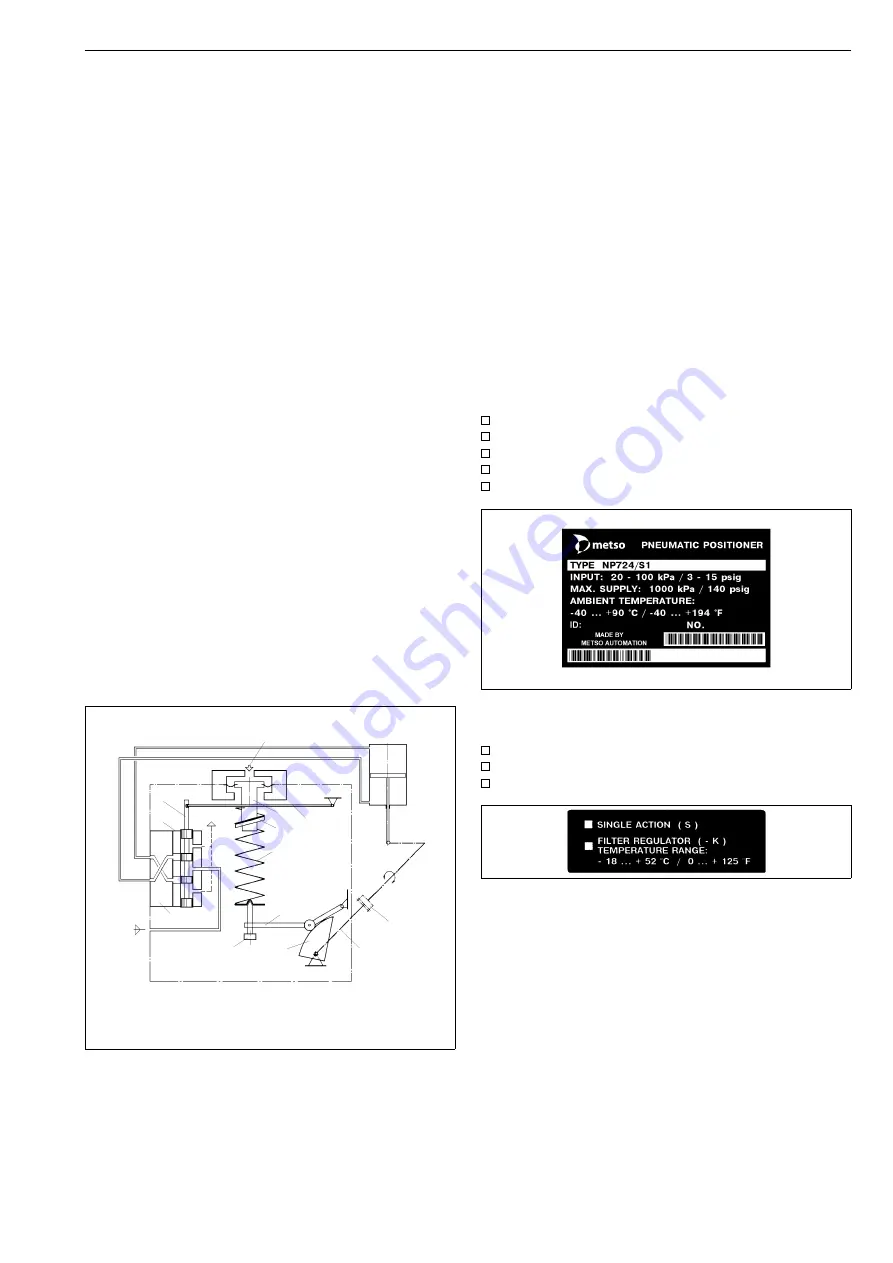
1
INTRODUCTION
1.1
General
The NP700 positioner is used for positioning double or single acting
actuator.
1.2
Operating principle
Operation is based on the force balance principle. One force is
caused by the signal pressure (IN) and acts on the diaphragm (8),
and the other is the compression force caused by the feedback
spring (60.1). The latter is directly proportional to the position of
the lower end of the spring, which is in turn dependent solely on
the position of the actuator shaft via the lever (33), the cam (29),
the positioner shaft (26) and the coupling (52).
When the equilibrium between the forces mentioned above is
disrupted, the beam (5) moves in the direction of the stronger force.
The end of the beam moves the spool (44.2) in the bore of the
body (44.1). When diverted from the equilibrium position, the spool
guides the supply air to one side of the actuator piston and the air
on the other side of the piston outside.
When the spool is in the equilibrium position the small volume of leakage
past the spool creates an equal pressure on either side of the unloaded
cylinder piston. This pressure is roughly 0,7 x the supply pressure.
If the signal pressure is altered, the spool moven out of the
equilibrium position and causes a pressure difference in the cylinder.
The piston moves in the direction of the difference pressure until
the compression force of the feedback spring generated by the
change in position is in equilibrium with the force generated by the
signal pressure.
Thus each signal pressure value corresponds to a single actuator
position. If an external force acts on the actuator shaft, the shaft
tends to move in the direction of the torque. This alters the position
of the spool via the feedback system so that the pressure difference
arising in the cylinder offsets the effect of the external torque.
Parts list for Figure 1:
Item
Part
5
Beam
8
Diaphragm piston
26
Shaft
29
Cam plate
33
Lever
44.1
Pilot valve body
44.2
Pilot valve spool
46
Changeover piece
52
Coupling
60.1
Feed-back spring
60.3
Range adjustment
67
Zero adjustment
1.3
Marking of positioner
The positioner has an adhesive ID plate, see Fig. 2.
The ID plate contains the following information (from top to
bottom):
Full type designation of the positioner
Input signal
Max. supply presssure
Ambient temperature range
Manufacturing series number
An additional plate, Fig. 3, has markings:
Single action (S)
Filter regulator (-K)
Temperature range
1.4
Technical specifications
Signal pressure ranges
20-100 kPa / 0.2-1.0 bar
(3-15 psi)
Split ranges
20-60 kPa, 60-100 kPa
(3-9 psi, 9-15 psi)
Turning angle of feed-back shaft
max. 90°
Relation between angle and signal
linear
Supply pressure p
s
0.14-1 MPa
(20-145 psi)
5
52
26
C2
67
46
IN
C1
29
44.2
8
60.1
33
60.3
44.1
S
Fig. 1.
Schematic diagram
Fig. 2.
ID plate
Fig. 3.
Additional plate
3