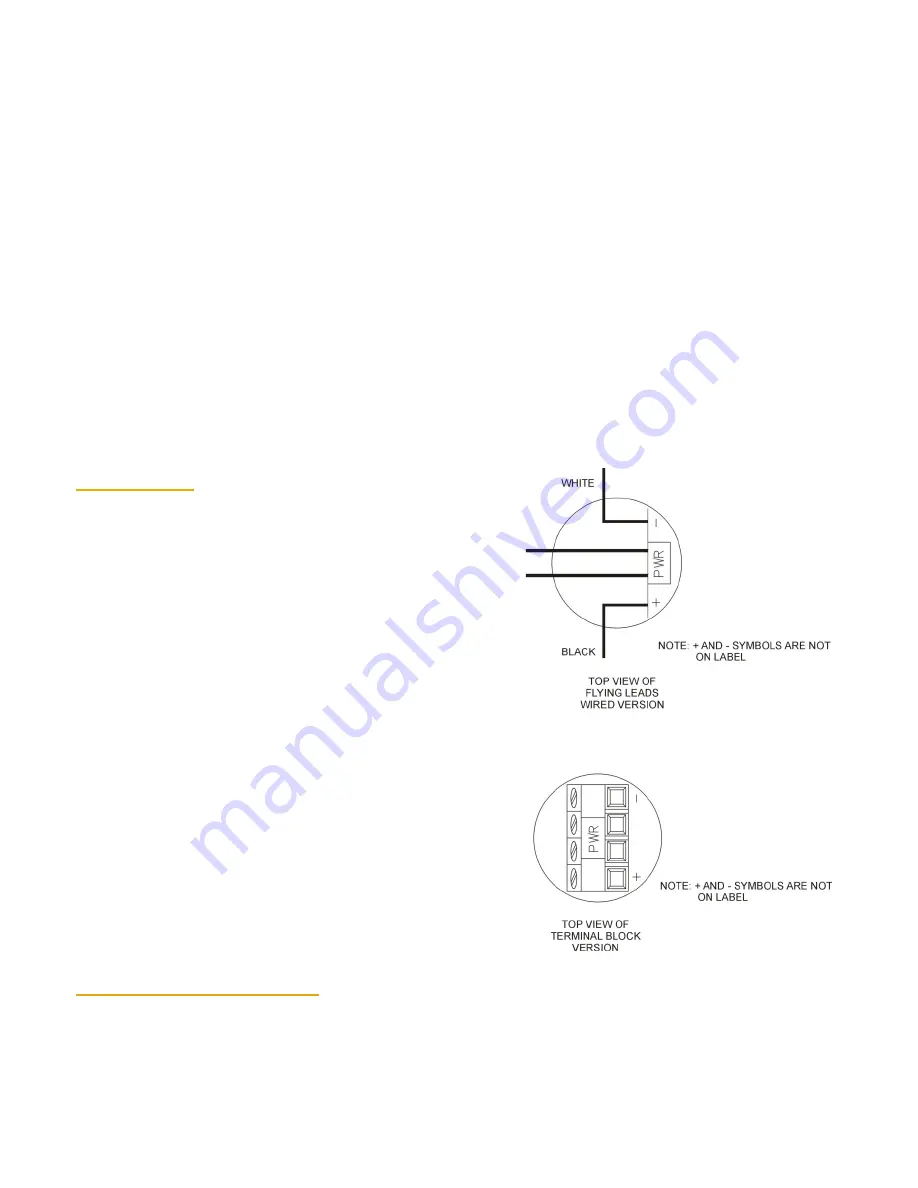
Document 9162
Manual - ST5484E 2-Wire Seismic Vibration Transmitter
Page 6 of 7
Rev. T (Oct 2013)
Figure 5 – Top view showing optional dynamic output
connections on transmitters with terminal blocks
When attaching conduit to the transmitter, observe the following:
•
Because the transmitter is sensitive to vibration, avoid unsupported lengths of conduit and excessive mass (such as
large hubs or junctions) hanging directly off the end of the transmitter. These can introduce unwanted vibrations
that do not reflect actual machinery vibration. These can also introduce mechanical stresses that cause the
transducer to fail prematurely.
•
A “Y” type conduit elbow such as the Metrix 8200 is preferred because it prevents the conduit from extending too
far away from the transmitter, thus limiting the likelihood of breakage by personnel working on or near the machine.
It also precludes long unsupported lengths of conduit directly aligned with the transmitter’s bore (longitudinal axis)
as noted in the bullet above.
•
Avoid attachment of rigid conduit directly to the transmitter; instead, use a small length of flexible conduit to
mechanically isolate the transmitter from vibration that might occur in rigid conduit.
•
If a 1-inch to 3/4-inch reducer is used at the elbow, a smaller diameter flexible conduit can be used.
7. Calibration
The ST5484E transmitter has been factory calibrated for the full scale
vibration level marked on the label. If the calibration is in doubt the
unit can be verified in the field by following the procedures outlined
below. Note that there are no Zero and Span adjustments on the
transmitter. Also note that the transmitter uses a true RMS amplitude
detection circuit; units supplied with a full scale range in peak units
scale the underlying RMS measurement by a factor of 1.414 to provide
a “derived peak” rather than true peak measurement.
7.1 Zero Verification
In the absence of vibration the output
current should be 4 mA ±0.1 mA. If the ambient vibration is more
than 2% of full scale, the transmitter should be removed from the
machine and placed on a vibration free surface for this
measurement. Often a piece of foam can be used to isolate the
transmitter from external motion.
7.2 Span Verification
Subject the transmitter to a known
vibration within the full scale range marked on the label. If using a
portable vibration shaker where it can be tested at full scale, the
output should be 20 mA ±0.5 mA.
8. Optional Dynamic Output
The transmitter can be ordered with an optional dynamic output.
Transmitters supplied with this option can be identified by the
presence of 4 flying leads instead of 2 (Figure 4), or 4 terminal connections instead of 2 (Figure 5).
Figure 4 – Top view showing optional dynamic output
connections on transmitters with flying leads