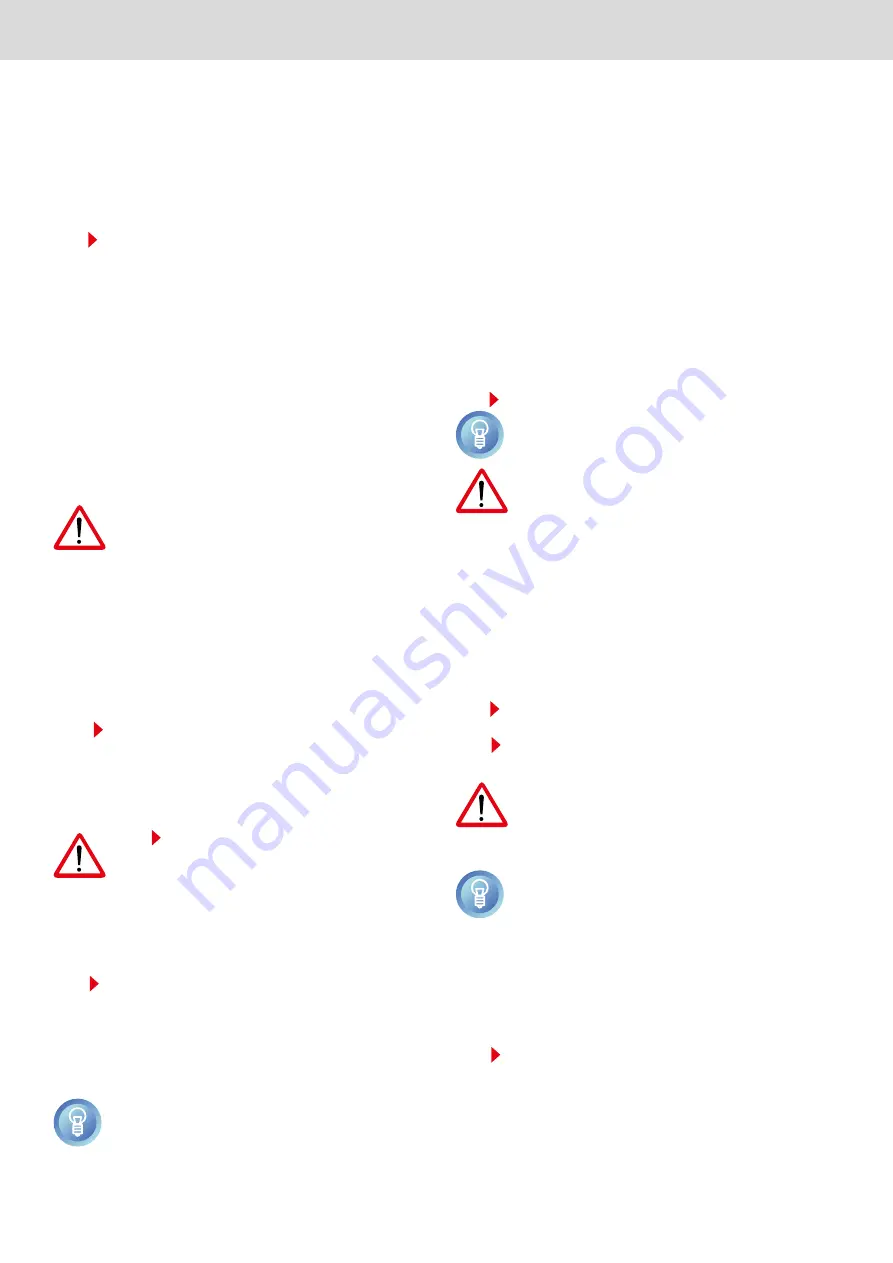
Rev. 02 - 11/2022
12
Characteristics of the installation area
Install the device in areas:
- compliant with industrial food handling;
- with adequate ventilation;
- prepared with electrical and plumbing systems compliant with
the legal provisions in force in the country of use and according
to the workplace safety requirements in the country of use;
- with temperatures from +15° to +43°C;
- that are sheltered against the elements;
- with flooring able to support the device at full load.
If the device is assembled on wheels (kit sold separately), it can-
not be levelled. Therefore the surface must be perfectly horizon-
tal, flat and completely smooth.
Protective film removal
Fig. 5
If the machine is intact, remove the protective film slowly.
Any glue residue can be removed with a proper sol-
vent. Do not use tools or abrasive or strong detergents
that might ruin the surfaces.
The removed protective films are potentially danger-
ous for children and animals. DO NOT LEAVE THEM UN-
ATTENDED IN THE INSTALLATION AREA AND CORRECT-
LY DISPOSE OF THEM IN ACCORDANCE WITH LOCAL
STANDARDS.
Positioning
The machines must be positioned on the ground only, on floors:
- that are not sensitive to heat or flammables;
- perfectly levelled;
- with a regular surface and completely smooth;
- that can support the device at full load.
Fig. 6
Keep the illustrated minimum clearances around the de-
vice: this will facilitate connections to utilities and maintenance.
Fig. 7
Always check for perfect levelling: if this is not the case,
rotate the feet until achieved.
DO NOT INSTALL THE DEVICE:
- NEAR OTHER MACHINES THAT REACH HIGH TEM-
PERATURES (E.G. OVENS OR FRYERS);
- NEAR WALLS OR FURNITURE THAT IS EITHER FLAM-
MABLE OR SENSITIVE TO HEAT.
Only use the manufacturer’s wheel kit to make the de-
vice movable. For assembly, if necessary, read the in-
structions supplied with the kit.
Spacer installation
The devices require ventilation at the back, where the vents and
refrigerating unit are found.
Therefore, do not place them against the wall but keep them ap-
proximately 5 cm away.
Fig. 8
In order to prevent accidental movements from shifting
the device too close to the wall, install the provided spacers on
the back of the device (especially if the device is assembled on
wheels). Use supplied spacers and screws only.
Drawings on page 8
Product transport, handling
Warning markings are printed on the packaging. They indicate
the limitations that must be observed to ensure safe device load-
ing, unloading and transport.
Fig. 1
Device transport and handling must be done exclusively
as follows:
- keep the packaging in the vertical position, as per the indications
printed on it (this precaution is necessary to prevent the oil con-
tained in the compressor from circulating, which may damage
the valves and cause problems when starting the motor);
- use suitable handling means. Do not handle the goods by hand.
If hoisting systems are used, such as forklifts or pallet jacks, the
weight must be carefully balanced.
The packaging usually consists in polystyrene and stretch film on
a wooden pallet, which is secured to the bottom of the device for
safer transport and handling.
The manufacturer cannot be held liable for problems due to
transport in conditions other than those previously specified.
PAY PARTICULAR ATTENTION TO THE PACKAGING IN-
CLINATION DURING TRANSPORT SINCE THE DEVICE
BARYCENTRE DOES NOT CORRESPOND TO ITS GE-
OMETRICAL CENTRE.
Stacking limits
The devices, regardless of the model, CANNOT be stacked during
transport or during storage.
Device check
Fig. 2
We recommend, after removing the packaging, you
check device integrity and make sure it was not damaged during
transport. If damage or anomalies are found, do not install the
device and promptly inform the carrier. In any case, damaged
devices cannot be returned to the manufacturer without prior
notice and without prior written authorisation.
Fig. 3
AFTER UNPACKING, WHEN MOVING THE DE-
VICE DO NOT PUSH IT OR PULL IT IN ORDER TO
AVOID THE RISK OF OVERTURNING OR DAMAGING
SOME PARTS (FOR EXAMPLE THE FEET).
NEVER TILT THE DEVICE FROM THE DOOR SIDE.
Systems preparation
Fig. 4
Systems must comply with the legal provisions in force
in the country of use and meet the specifications on the serial
number plate.
There must be:
-
A
: a circuit breaker with high sensitivity (30 mA);
-
B
: a point of connection to the power mains;
-
C
: a point of discharge (optional).
Please see the specific chapters for their specifications
(for example, the chapter “Electrical connection”).
INSTALLATION