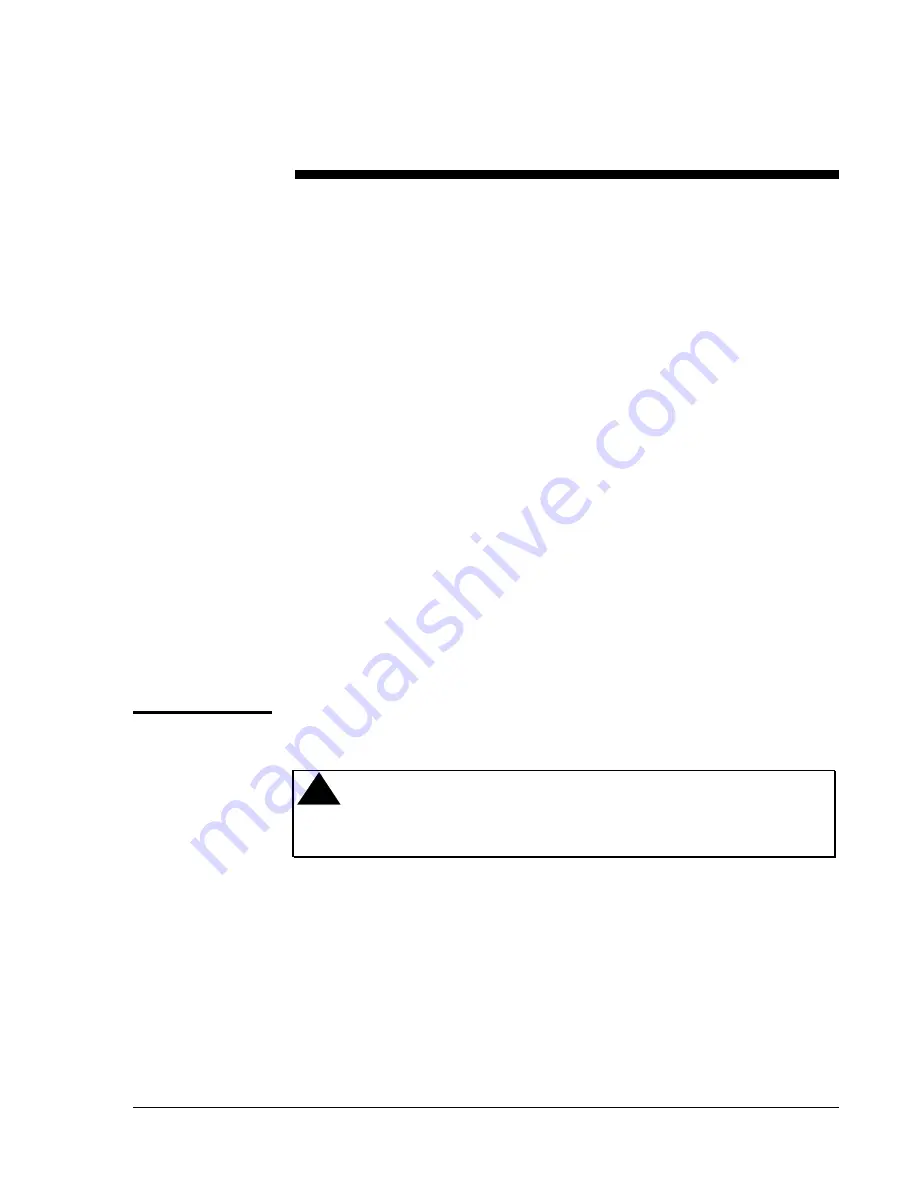
Conventional Products—2412, 2412TH, 2424, and 2424TH Direct Wire Photoelectronic Smoke Detectors 3
Introduction
This document contains important information about installing and
operating direct wire smoke detectors. These conventional detectors are
manufactured by System Sensor for use with Johnson Controls systems. If
you install this detector for someone else to use, you must leave a copy of
this document with the user.
These instructions apply to System Sensor detectors for mounting, wiring,
installation, testing, and maintenance. Follow only those instructions that
apply to the model you are installing.
Before you install any direct wire smoke detectors, read and be familiar
with:
●
The Guide for Proper Use of System Smoke Detectors Technical
Bulletin in the Fire Initiating Devices and Notification Appliances
Technical Manual (FAN 408) that provides detailed information on
detector spacing, placement, zoning, wiring, and special applications
●
or, for non-United States installations, applicable codes and standards
specific to the country and locality of installation
Failure to follow these directions may result in failure of this device to
report an alarm or trouble condition or respond properly to an alarm
condition. Johnson Controls is not responsible for devices that have been
improperly installed, tested, or maintained by others.
!
CAUTION: Equipment hazard. Do not use in potentially
explosive atmospheres. Do not leave unused
wires exposed.
The 2412 and 2424 photoelectronic smoke detectors utilize state-of-the-art
optical sensing chambers. These detectors are designed to provide open
area protection, and are to be used with UL Listed control panels only.
The 2412 applies to 12 volt panels and operates at 12 VDC, and
the 2424 applies to 24 volt panels and operates at 24 VDC. The detectors’
operation and sensitivity can be tested in place. Models 2412TH and
2424TH have the same specifications as models 2412 and 2424; however,
they feature a built-in fixed temperature (135°F) thermal detection unit.
General
Description
2412 and 2424
Direct Wire
Detectors