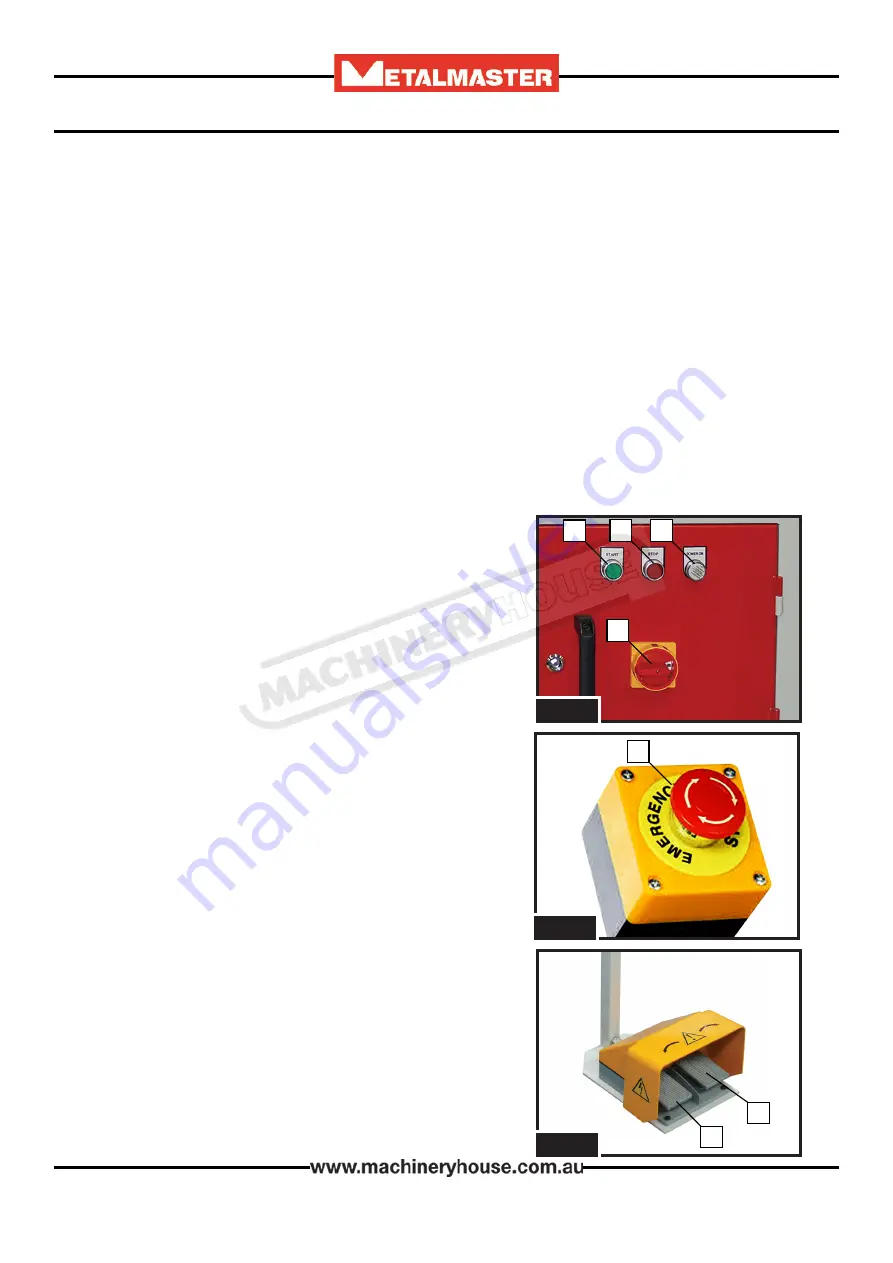
16
OPERATION MANUAL
4. OPERATION
This machine will perform many types of operations that are beyond the scope of this manual.
Many of these operations can be dangerous or deadly if performed incorrectly.
The instructions in this section are written with the understanding that the operator has the
necessary knowledge and skills to operate this machine. If at any time you are experiencing
difficulties performing any operation, stop using the machine!
If you are an inexperienced operator, we strongly recommend that you read books, trade
articles, or seek training from an experienced operator before performing any unfamiliar
operations.
Above all, your safety should come first!
4.1 CONTROLS
The purpose of this control overview is to provide the novice machine operator with a basic
understanding of how the machine is used during operation, and the machine controls and
what they do. It also helps the operator to understand if they are discussed later in this manual.
F
ig
. 4.1
F
ig
. 4.2
F
ig
. 4.3
A. ON Button
. Switches the power ON to the machine.
(Fig.4.1)
B. OFF Button
. Switches the power OFF to the machine.
C. Power Light
. Illuminates when power is switched on.
D. Main Isolating Switch
. Isolates the machine from the
power supply. (Fig.4.1)
E. Emergency Stop Button
. When pressed stops the
machine and locks access to the power supply. To
unlock and reset the stop button twist the red top
in the direction of the arrows to allow the red button
to pop up. (Fig.4.2)
F. Right Pedal.
When pressed and held down the rolls
rotate in a clock wise direction (Fig.4.3)
G. Left Pedal.
When pressed and held down the rolls
rotate in a anti clock wise direction (Fig.4.3)
A
B
C
D
E
G
F
Summary of Contents for SJM-2.5
Page 6: ...6 OPERATION MANUAL 1 4 SJM 2 5 DIMENSIONS...
Page 7: ...7 OPERATION MANUAL 1 5 SJM 4 0 DIMENSIONS...
Page 22: ...22 OPERATION MANUAL ELECTRICAL DIAGRAM...
Page 23: ...23 OPERATION MANUAL SJM 2 5 CABINET SPARE PARTS DIAGRAM...
Page 24: ...24 OPERATION MANUAL SJM 2 5 SPARE PARTS DIAGRAM...
Page 26: ...26 OPERATION MANUAL SJM 4 0 CABINET DIAGRAM...
Page 27: ...27 OPERATION MANUAL SJM 4 0 SPARE PARTS DIAGRAM...