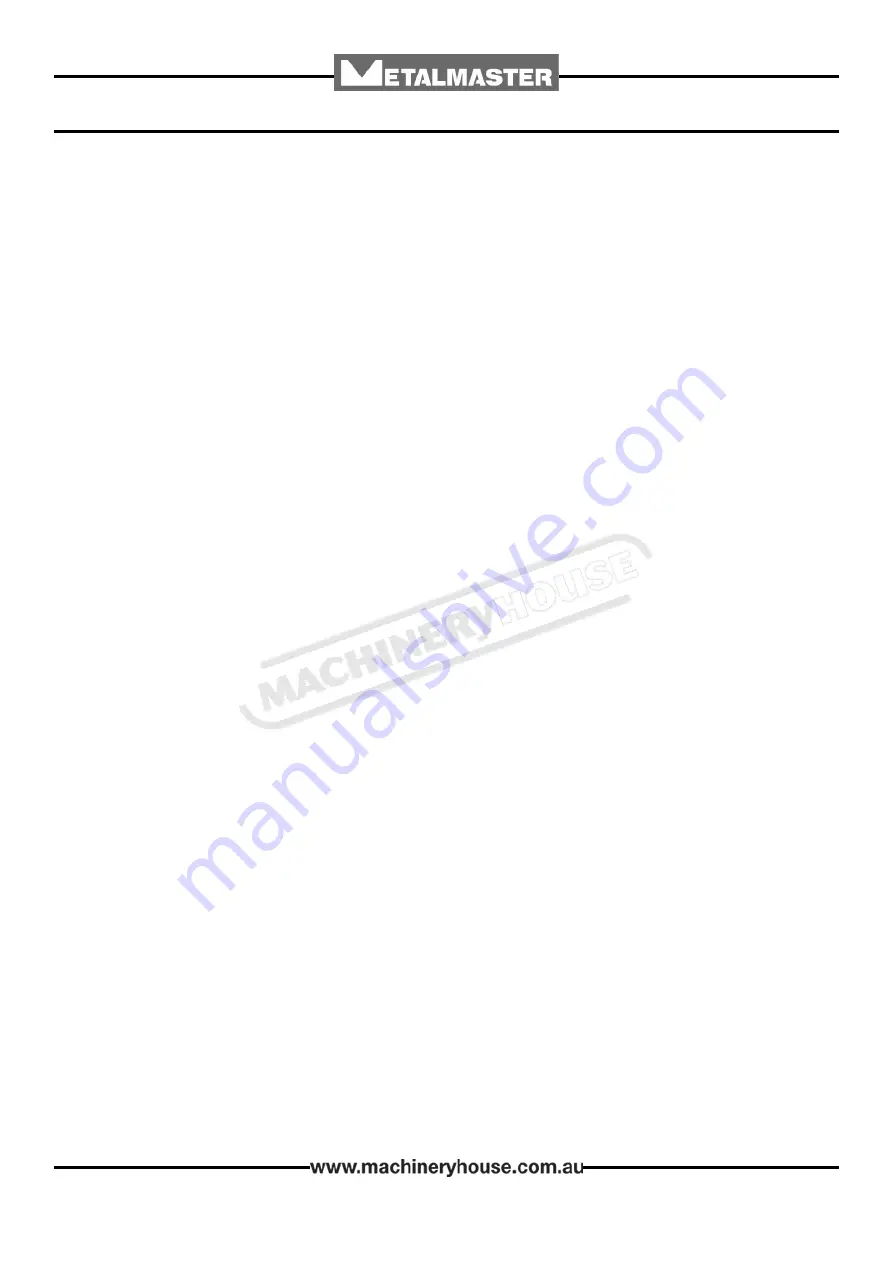
9
OPERATION MANUAL
3. SETUP
3.1 UNPACKING
When unpacking, check to make sure that all parts shown in the Parts Diagram are included. If
any parts are missing or broken, please contact the distributer
3.2 ASSEMBLY
THE METALMASTER Shrinker & Stretcher will require minor assembly prior to operation. It is
important that the entire manual is read to become familiar with the unit BEFORE you
assemble and use the Machine. Before assembling the Metal Shrinker Stretcher, be sure that
you have all parts described in the Parts List. (Fig.3.1)
To assemble the machine:
1. Secure the tool to a workbench or the optional stand (sold separately).
2. For portability, the tool may also be clamped into the jaws of a vise.
3. The more rigidly the tool is secured, the easier it is to be used .
4. Two holes, pre-drilled and tapped into each base, accept M10 bolts.
4 OPERATION
4.1 OPERATIONAL OVERVIEW
1. Before fabricating on the Shrinker & Stretcher, bend the metal to be formed 90° on a Sheet
Metal bender or Press Brake, creating a maximum flange depth that is no greater than
25.4mm/1”.
2. Make a template out of cardboard or a short piece of wire. A template is critical to achieve a
good fit with minimal filler use.
3. Work the leading edge first. This breaks down the maximum resistance and permits easy
and accurate working thereafter.
4. For best results and maximum forming power, insert metal only halfway into the jaws.
5. The bunching or pocketing that typically occurs when shrinking can be quickly hammered
out.
6. Control the pressure exerted on the handle or the foot pedal while forming the metal.
7. Move the metal back and forth until the desired radius is obtained.
8. The jaws of the tools are “toothed” for better grip on the metal. These teeth leave slight
markings, depending on the hardness of the metal, which can be removed with an
abrasive cloth or wheel.
BASIC PANEL FABRICATION
For car and bike restorers, fabricating body parts is often the only way to go. With good plan-
ning, you can reproduce shapes to match the original contours.
Most older cars catch and hold moisture, thus rusting out. Usually so much metal is gone that
there is very little left to rescue. A new, fabricated part is the only way to go.
First, make a cardboard template, then place the flanged section went into the shrinker &
stretcher shrinking jaws. By pressing firmly on the handle or the foot pedal and moving the
metal back and forth, the jaws’ teeth keep drawing the metal closer and closer, creating a
smooth curve. Check the new piece with the cardboard template, and within minutes the
piece will be close to size.