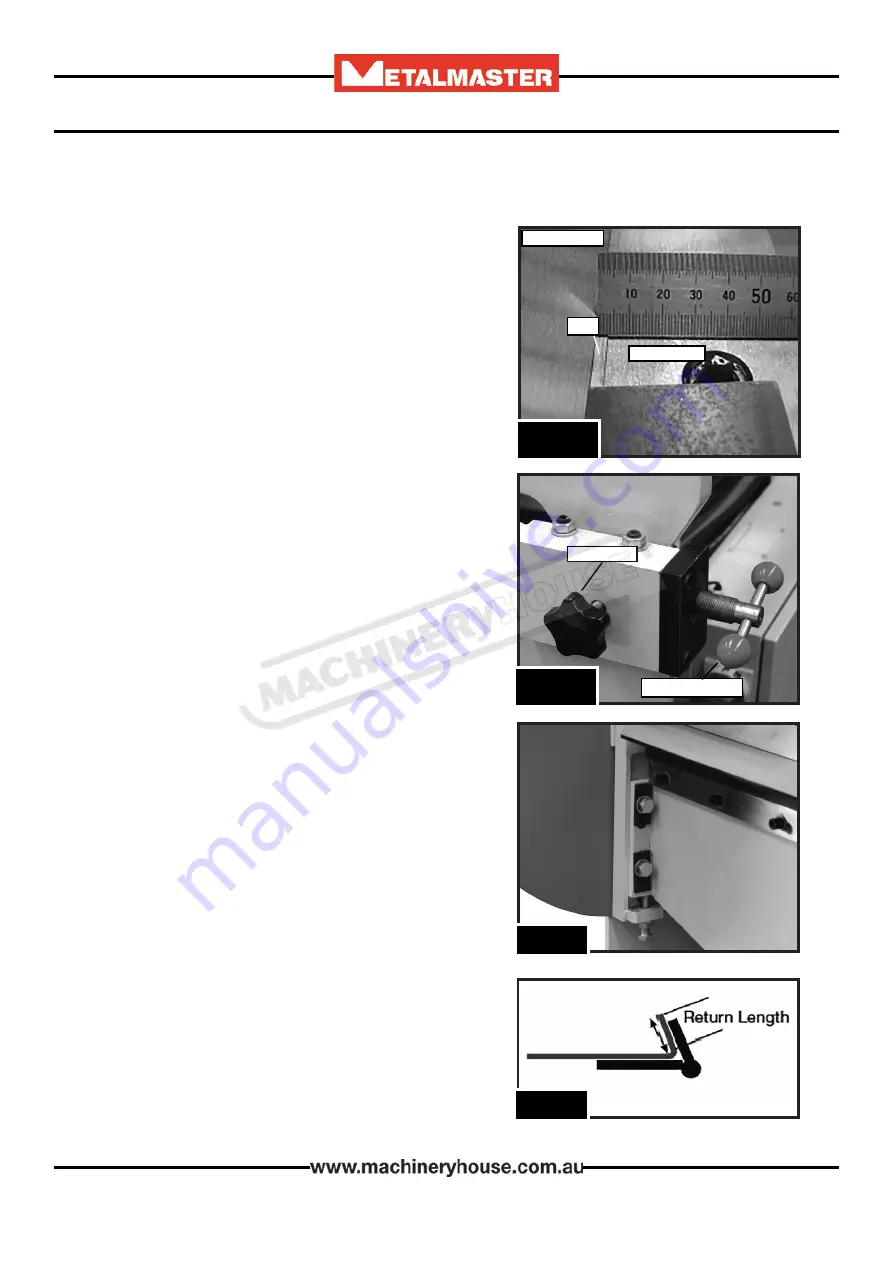
15
OPERATION MANUAL
4. OPERATION
4.1 SETTING THE CLAMP GAP
Before operating the machine the clamp gap needs
be set to match the material thickness
The Clamp gap must be set to a minimum of 1.5 x
material thickness. (Fig. 4.1)
Example: If the material that is to be bent is 2mm
then the clamp gap must be set to a minimum of
3mm.
Each panbrake may have different mechanisms for
adjusting the clamp gap but the formula of 1.5 x
Material Thickness must be maintained to prevent
overload and possible damage.
These machines are fitted with an easy to use clamp
beam adjustment. There are two adjustment screws
(Fig.4.2) on the machine situated on each side of
the machine.
To adjust
1. Loosen the lock screws on both sides
2. Turn the two adjusting screws until the gap
(Fig.4.2) is correct.
3. Tighten the two lock screws and recheck the gap
If needed, a combination of top clamp adjustment
and apron adjustment can be applied.
NOTE:
The locking bolts on the apron must be re-
leased before adjusting, then tightened when the
correct height is reached.
RETURN LENGTH - LIMITATION
Caution
- There is a minimum “Return Length” of 15
x Thickness of Material when bending thicker mate-
rial over 1mm. Damage could occur to the machine
if the return is too short.
Example: If bending 2mm the minimum return
length must be 30mm (Fig. 4.4)
F
ig
. 4.1
C
lamp
Finger
F
olding
arm
g
ap
F
ig
. 4.2
l
oCk
sCrew
a
djusting
sCrew
F
ig
. 4.3
F
ig
. 4.4
22/07/2019
Instructions Manual for PB-422L (S576)
15