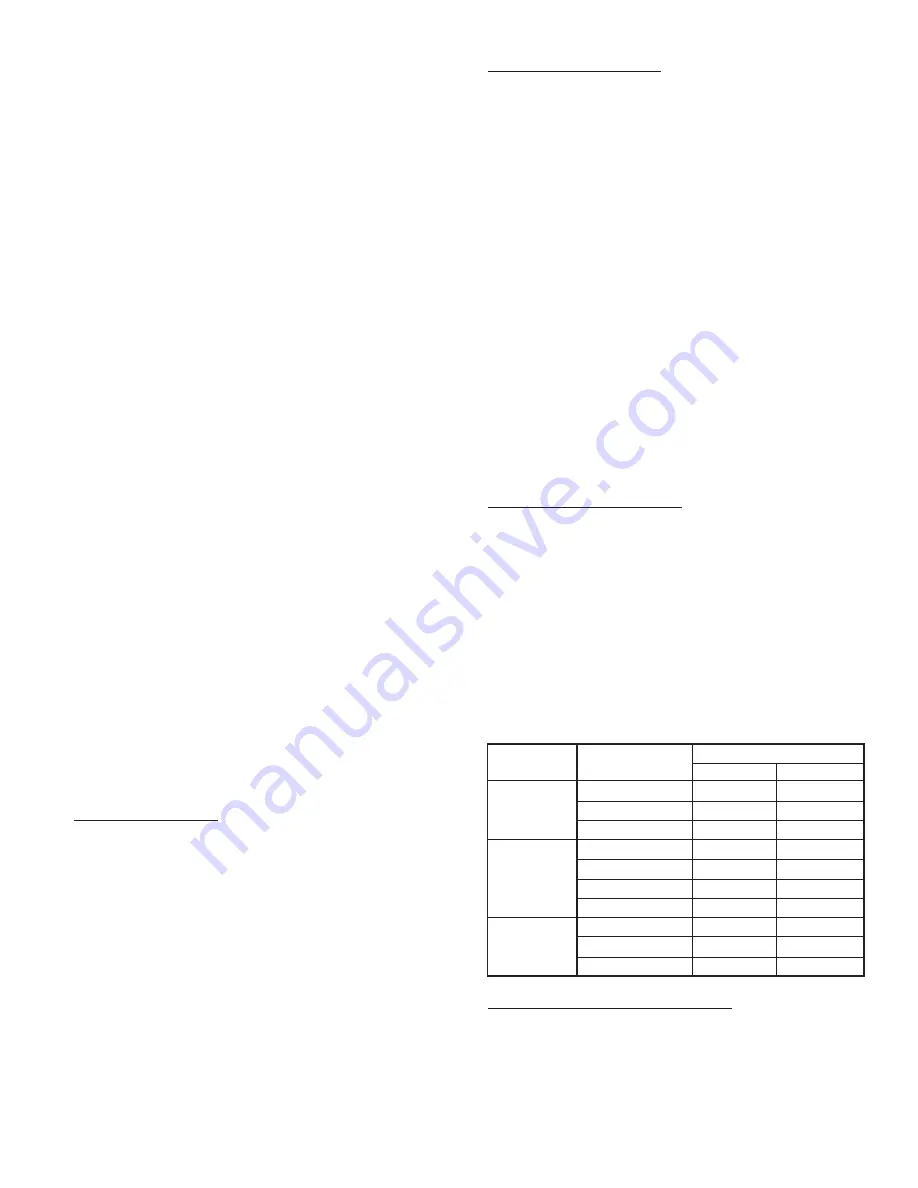
Prior to starting pump recheck installation
procedures with the operational start-up checklist
found on page 19 of this manual.
Start pump and bring up to speed, open discharge
valve to the rated flow.
WARNING: DO NOT RUN PUMP WITH A CLOSED
DISCHARGE VALVE AS THE LIQUID IN THE PUMP
WILL RAPIDLY INCREASE IN TEMPERATURE,
POSSIBLY CAUSING DAMAGE TO PUMP.
Check flush water to mechanical seal, if not
lubricated from the pump discharge.
Check oil levels in the bearing frame.
If the pump is provided with packing, the gland
should be adjusted (while running) to allow leakage
of approximately 60 drops per minute.
EXERCISE EXTREME CAUTION.
OPERATIONAL CHECK LIST
A) Periodically check stuffing box for leakage with
packing, and no leakage with mechanical seals.
B) Periodically check lubrication to the pump and
driver bearings.
C) Periodically check for excessive vibrations and
oil temperatures. Correct if necessary.
MAINTENANCE
Fybroc pumps are designed for a long service life.
The only scheduled maintenance items are the
lubrication intervals for the pump and motor.
Please refer to the lubrication procedures given
in the start-up section.
PUMP
Oil Bath Lubrication
The frequency with which the oil in the power-
frame should be changed depends greatly on the
operating temperature and the cleanliness of the
environment. For power-frames running at approxi-
mately 122°F (50°C), typically the lower speed
pumps, the oil should be changed once a year.
For power-frames running at approximately 167°F
(75°C) the oil should be changed every six months.
If the environment is hostile, the lubrication
intervals should be reduced.
Re-Greasable Bearings
The frequency with which the grease in the power-
frame should be changed depends greatly on the
operating time and the cleanliness of the environ-
ment. For power-frames running at 2900-3500 rpm
the bearings should be re-lubricated every 5,000
hrs, for all other speeds every 10,000 hrs.
Before greasing, be sure fittings are clean and free
from dirt. Remove the 1/8" grease relief plugs for
the front and rear bearings. Using a standard
grease-gun inject grease into the bearing using the
grease fittings until grease comes out of the bleed
holes. Allow the pump to operate approximately
2 hours before replacing the pipe-plugs, this will
allow any excess grease to purge itself.
WARNING: FAILURE TO REMOVE THE PURGE
PLUGS WHEN FILLING THE BEARINGS WITH
GREASE MAY RESULT IN DAMAGE TO THE
BEARING SEALS.
Greased For Life Bearings
Greased for life bearings require no maintenance.
MOTOR
The motor re-lubrication intervals are greatly
influenced by the environment it is in and the
length of time it runs. Refer to the following chart
for typical re-lubrication values for motors.
Standard duty is when the motor is operated eight
hours a day and the environment is free from dust.
Severe duty is when the motor runs twenty-four
hours per day with exposure to dirt and dust.
I
nstructions For Lubricating Motors
Before greasing, be sure fittings are clean and free
from dirt. Remove grease relief plug or plate and
using a low pressure grease gun pump in the
required grease. Do not over-grease. After
relubricating allow motor to run for an hour before
replacing relief hardware.
Sync RPM Motor Frame Type of Service
Range Range
Standard Duty Severe Duty
143T - 256T 5 Yrs 3 Yrs
3600 284T - 286T 1 Yr 4 Mos
324T - 365T 9 Mos 3 Mos
143T - 256T 7 Yrs 3 Yrs
284 - 326T 4 Yrs 1.5 Yrs
364T - 365T 2.5 Yrs 10 Mos
404T - 447T 2 Yrs 8 Mos
143T - 256T 7 Yrs 3 Yrs
1200 284T - 326T 4 Yrs 1.5 Yrs
364T - 447T 3 Yrs 1 Yr
1800
8