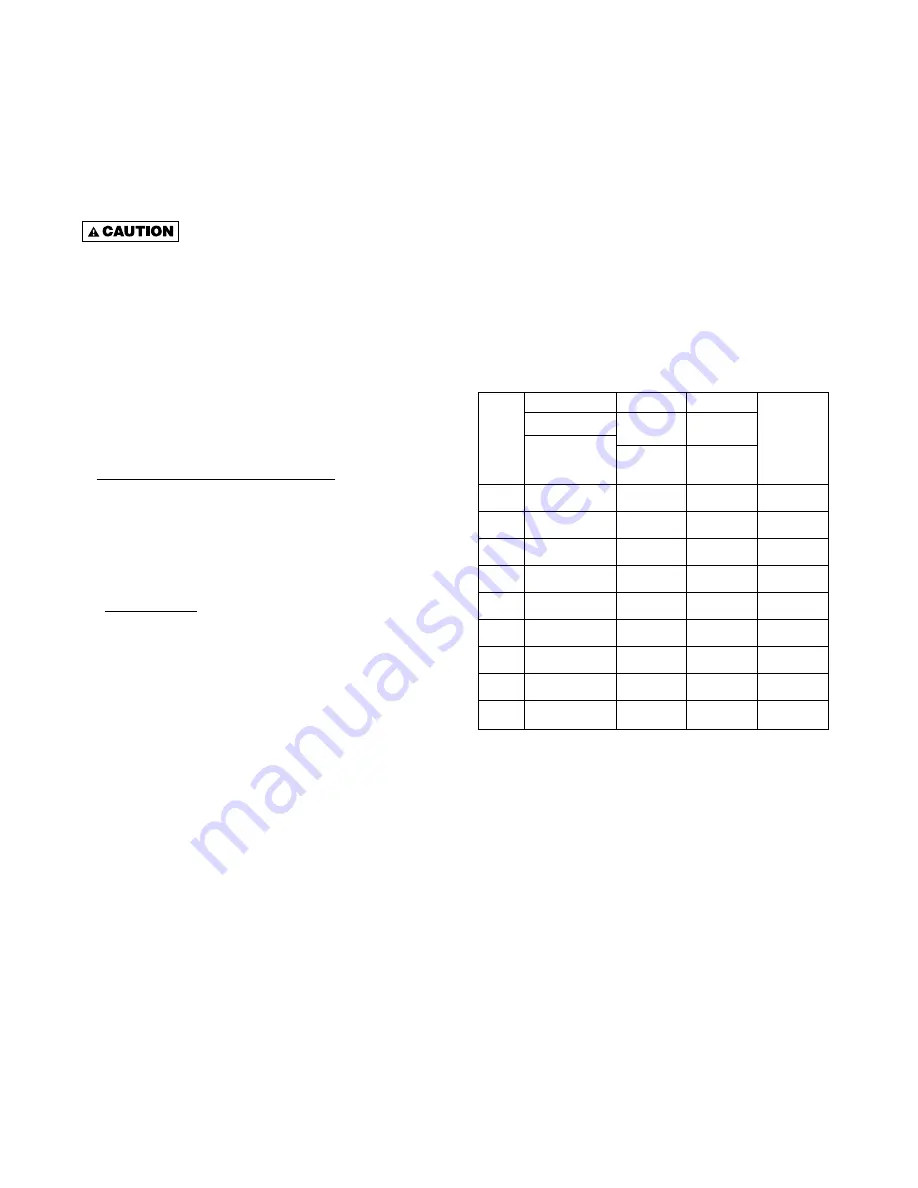
19
OPERATION (continued) - PRIMARY AIR SHUTTER ADJUSTMENT
Primary air adjustment is made at the factory. No fi eld adjustments are necessary.
GAS INPUT RATE
2. PROPANE GAS: An exact manifold pressure of 10.0
inches WC (2.5 kPa) must be maintained for proper
operation of the unit heater. If the unit is equipped
with a pressure regulator on the combination gas
valve, follow steps "a" through "d" above. If the unit
is not so equipped, the propane gas supply system
pressure must be regulated to attain this manifold
operating pressure.
3. The adjusted manifold pressure should not vary
more than 10% from pressure specifi ed in Table 6.
Table 6 - Main Burner Orifi ce Schedule*
*
INPUT
IN
1000
BTU
2500 BTU/Ft
3
(93.1 MJ/m
3
)
PROPANE
TYPE OF GAS
NATURAL
HEATING VALUE
1050 BTU/Ft
3
(39.1 MJ/m
3
)
3.5 INCH WC
(0.87kPA)
10 INCH WC
(2.49 kPA)
NUMBER
OF BURNER
ORIFICES
MANIFOLD
PRESSURE
4
5
6
7
8
9
10
11
12
100
125
150
175
200
250
300
350
400
FT
3
/HR
ORIFICE DRILL
FT
3
/HR
ORIFICE DRILL
FT
3
/HR
ORIFICE DRILL
FT
3
/HR
ORIFICE DRILL
FT
3
/HR
ORIFICE DRILL
FT
3
/HR
ORIFICE DRILL
FT
3
/HR
ORIFICE DRILL
FT
3
/HR
ORIFICE DRILL
FT
3
/HR
ORIFICE DRILL
93
42
116
42
140
42
163
42
186
42
233
42
280
42
326
42
372
42
40
53
50
53
60
53
70
53
80
53
100
53
120
53
140
53
160
53
*This schedule is for units at operating at normal altitudes of 2000 feet
(610m) or less.
When installed in Canada, any references to deration at altitudes in excess of
2000 feet (610m) are to be ignored. At altitudes of 2000 to 4500 feet (610 to
1372m), the unit heaters must be fi eld derated to 90% of the normal altitude
rating, and be so marked in accordance with ETL certifi cation. See Table 6A
for fi eld deration information.
Check the gas input rate as follows (Refer to General
Safety Information section for metric conversions).
Never overfi re the unit heater, as this
may cause unsatisfactory operation, or shorten the
life of the heater.
1. Turn off all gas appliances that use gas through the
same meter as the unit heater.
2. Turn the gas on to the unit heater.
3. Clock the time in seconds required to burn 1 cubic
foot of gas by checking the gas meter.
4. Insert the time required to burn one cubic foot of
gas into the following formula and compute the input
rate.
3600 (Sec. per Hr.) X BTU/Cu. Feet
= Input Rate
Time
(Sec.)
For example:
Assume the BTU content of one cubic foot of gas is
1000, and that it takes 18 seconds to burn one cubic
foot of gas.
3600 x 1000
= 200,000
18
NOTICE: If the computation exceeds, or is less than
95% of the gas BTU/hr. input rating (see Table 5),
adjust the gas pressure.
Adjust the gas pressure as follows:
1. NATURAL GAS: Best results are obtained when
the unit heater is operating at its full rated input with
the manifold pressure of 3.5 inches WC (0.9 kPa).
Adjustment of the pressure regulator is not normally
necessary since it is preset at the factory. However,
fi eld adjustment may be made as follows:
a. Attach manometer at the pressure tap plug
adjacent to the control outlet.
b. Remove the regulator adjustment screw cap,
located on the combination gas valve.
c. With a small screwdriver, rotate the adjustment
screw counterclockwise to decrease pressure, or
clockwise to increase pressure.
d. Replace regulator adjustment screw cap.
Summary of Contents for TUBULAR GAS FIRED DIRECT SPARK PROPELLER UNIT HEATERS
Page 16: ...16 Figure 8A Figure 8B VENTING continued D3620F D3619C...
Page 17: ...17 VENTING continued Figure 9A Figure 9B D3661F D3662D...
Page 29: ...29 NOTES...
Page 30: ...30 NOTES...